Experimental Investigation on the Effect of Forced Assembly on Fatigue Behavior of Single-Lap, Countersunk Composite Bolted Joints
INTERNATIONAL JOURNAL OF FATIGUE(2024)
摘要
Forced assembly is a common countermeasure for eliminating the interface gap during composite airframe assembly, which modifies the bolt-hole bearing behavior and brings failure risks. In this study, an experimental investigation on the effect of forced assembly on the fatigue behavior of single-lap, countersunk composite bolted joints is presented. The hole elongation and dynamic stiffness are obtained based on ASTM D6873. The S-N curves are fitted according to ASTM E739. The fatigue damage is observed through microscopy, and the residual strength is acquired by static tensile tests. The results indicate that forced assembly significantly shortens the fatigue life of joints. After forced assembly, the hole elongation evolves faster and reaches the fatigue failure threshold earlier. In addition, the initial dynamic stiffness is reduced, and the loss of stiffness is accelerated. Apart from the designed hole bearing failure, another failure mode, i.e., bolt head cracking, is observed under low fatigue load level (70% of 2% offset bearing static strength), leading to faster degradation of fatigue property. Under equal hole elongation (4% of the hole diameter), the joints with forced assembly display severe hole bearing damage, and visible shearing cracks are observed, lowering the residual strength.
更多查看译文
关键词
Composite bolted joints,Forced assembly,Fatigue tests,Failure modes,Residual strength
AI 理解论文
溯源树
样例
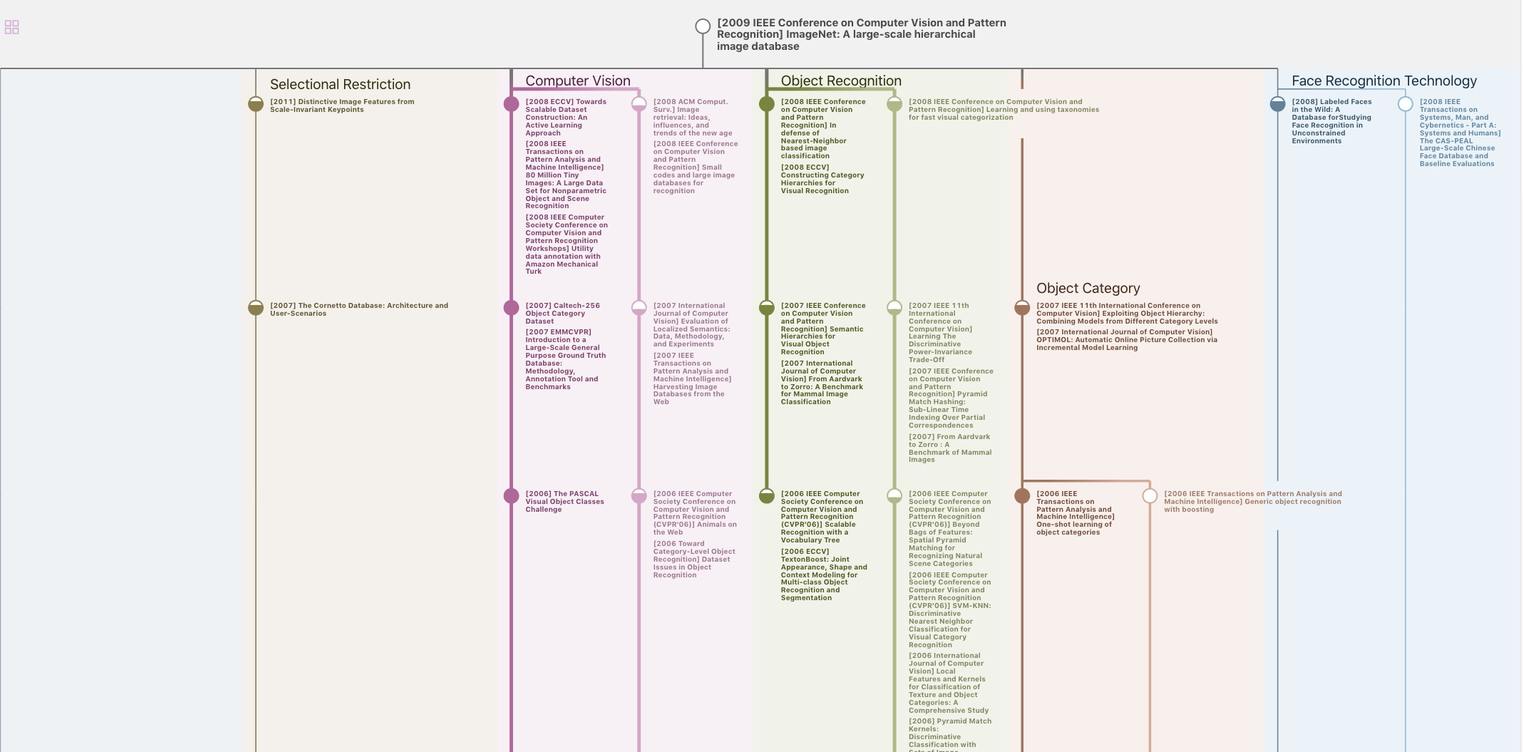
生成溯源树,研究论文发展脉络
Chat Paper
正在生成论文摘要