Research on the Wear of Groove Structured Grinding Wheel Based on the Simulation and Experiment of Single Abrasive Particle Scratching
International journal of precision engineering and manufacturing/International Journal of the Korean Society of Precision Engineering(2024)
摘要
In order to comprehend the abrasive wear mechanism of CBN grinding wheels with varying structural characteristic parameters, the influence of these parameters on abrasive wear was transformed into the impact of undeformed chip thickness on abrasive wear. Subsequently, a two-dimensional finite element simulation model of single CBN abrasive scratching was established. The effects of different maximum undeformed chip thicknesses, scratching speeds, and abrasive rake angles on wear morphology and normal scratching force were analyzed. Furthermore, the simulation model was validated through single abrasive scratching experiments. The results indicate that the predominant form of CBN particle wear is crushing and fracture. During the scratching process, wear consistently initiates with micro-crushing and micro-cracks between the particle tip and front tool face. As this process continues, cracks propagate within the particle until ultimately causing its fracture. When holding constant both scratching speed and abrasive rake angle, an increase in maximum undeformed chip thickness (i.e., intermittent ratio of grinding wheel) leads to elevated normal scratching force and greater degree of abrasive wear. Moreover, an increase in scratching speed exacerbates abrasion while an increase in abrasive rake angle reduces scratching force thereby alleviating the abrasion process.
更多查看译文
关键词
Structured grinding wheel,Grinding wheel wear,Single CBN abrasive scratching
AI 理解论文
溯源树
样例
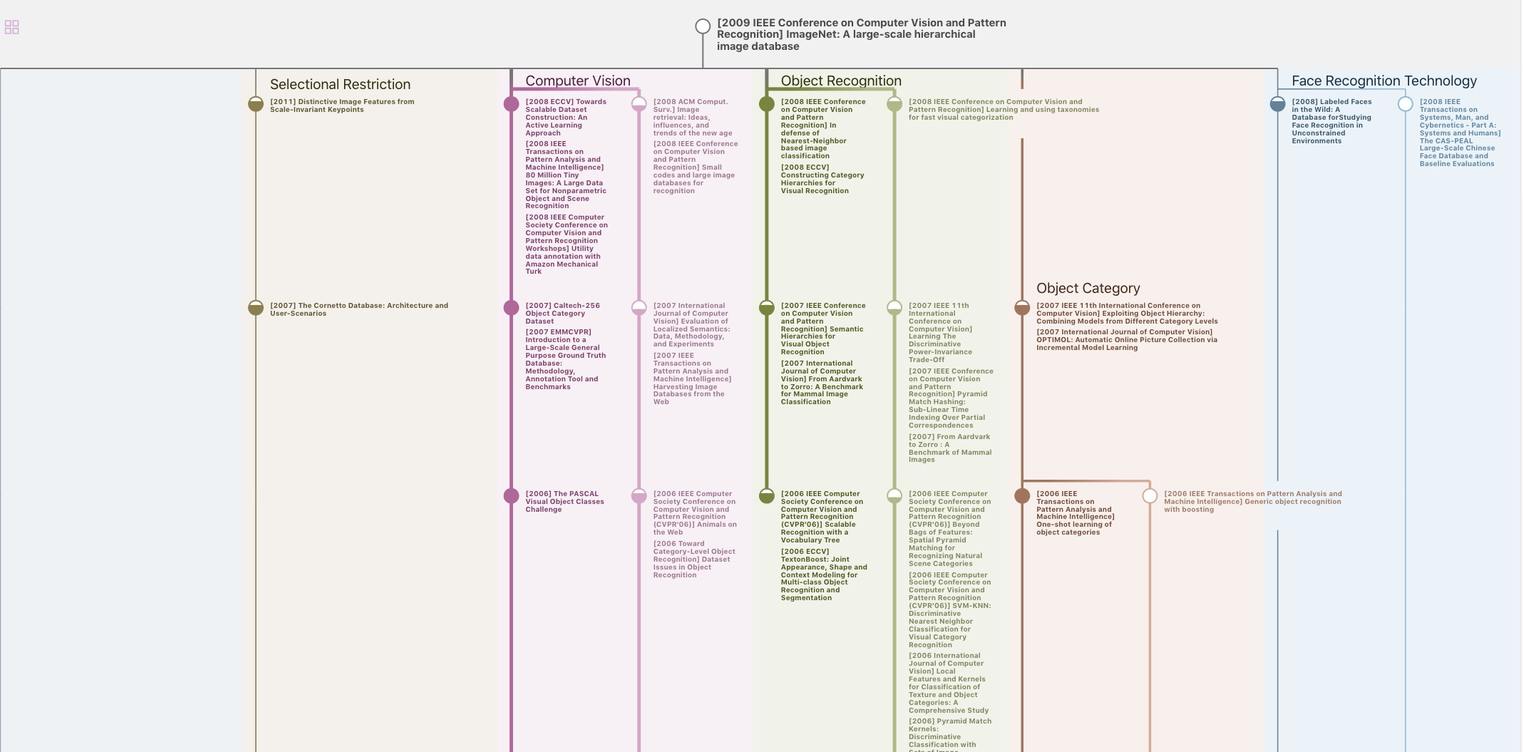
生成溯源树,研究论文发展脉络
Chat Paper
正在生成论文摘要