Effect of Al 2 O 3 Additive on Ability of WC–8 Co Anode Material to Form Coating Layer Using Electrical Spark Alloying
Inorganic materials applied research(2023)
摘要
Anode materials based on WC–8 wt % Co are explored. The materials containing 1, 3, and 6 wt % Al 2 O 3 are used to deposit an electric spark coating layer on samples made of steel grade 35. Specifically, mechanisms underlying anode erosion and cathode gain are explored. The mass transfer factor is estimated. The method of X-ray phase analysis of coating layers confirms that tungsten subcarbide is dominant in the layer composition. The data gathered using scanning electron microscopy and energy dispersion analysis indicate that aluminum oxide is present in the form of micron-size and finely dispersed inclusions in the coating structure. Moreover, the amount of aluminum oxide in coating layers increases when the content of Al 2 O 3 grows in anodes. Potential sweep tests indicate an increase in corrosion potential and decrease in corrosion current density when the content of Al 2 O 3 increases in the coating layer. The heat resistance of coating layers gradually increases at a temperature of 700°C with growing concentration of aluminum oxide. For 100 h of testing, the weight gain in coated samples is 4 to 11 times less than that of uncoated steel grade 35. The microhardness of alloyed layers ranges from 13 to 15.6 GPa, which is 4.6 to 5.4 times higher than that in steel grade 35. The coating having the highest concentration of aluminum oxide exhibits the highest hardness. The wear rate of the coating layers is 3.9 to 12.5 times lower than that in steel grade 35. The wear of electrical spark coating layers gradually decreases from 1.45 × 10 –5 to 0.45 × 10 –5 mm 3 N –1 m –1 with growing concentration of Al 2 O 3 in anode material.
更多查看译文
关键词
electric spark alloying,WC–8% Co,Al2O3,hardness,corrosion,friction coefficient,wear resistance,heat resistance
AI 理解论文
溯源树
样例
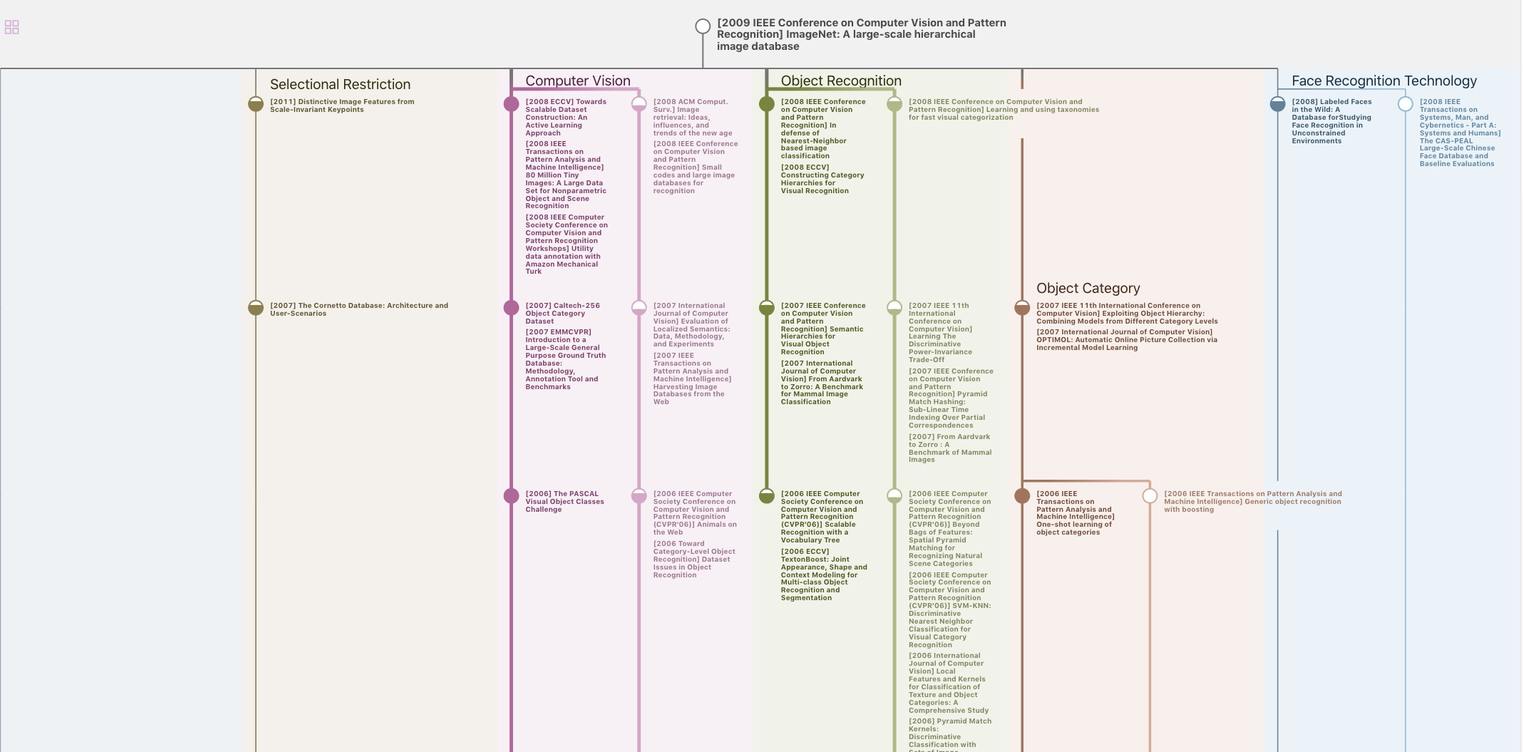
生成溯源树,研究论文发展脉络
Chat Paper
正在生成论文摘要