Microstructure evolution, failure mechanism and life prediction of additively manufactured Inconel 625 superalloy with comparable low cycle fatigue performance
INTERNATIONAL JOURNAL OF FATIGUE(2024)
摘要
During hot end components service, i.e., startup and shutdown processes, the cyclic stress caused by the asymmetry loading conditions is introduced. To study the effect of mean stress on the cyclic response, the low cycle fatigue, failure mechanism and life prediction model of additively manufactured (AMed) Inconel 625 superalloy at room temperature (RT) and service temperature (600 degrees C) with strain ratio R = -1 and 0.1 are conducted. Experimental results indicate that the different cyclic softening and hardening behavior at RT and 600 degrees C is the result of competition between dislocation slip, back stress hardening and second phase precipitation. According to the evaluation of the internal stress variables, the long-range back stress plays a crucial role to control the cyclic behavior of the alloy. At RT, the heterogeneous grain structure introduced by additive manufacturing causes the back stress hardening, making the material exhibit high fatigue performance. But this hetero-deformation induced (HDI) strengthening is inhibited at high temperatures due to the uniform distribution of dislocations. In addition, a low cycle fatigue life prediction model based on critical plane method is established which presents an easily assess to evaluate the low cyclic fatigue life of an AMed material under various test condition.
更多查看译文
关键词
Additive manufacturing,Low cycle fatigue,Strain ratio,Microstructure-sensitive,Back stress
AI 理解论文
溯源树
样例
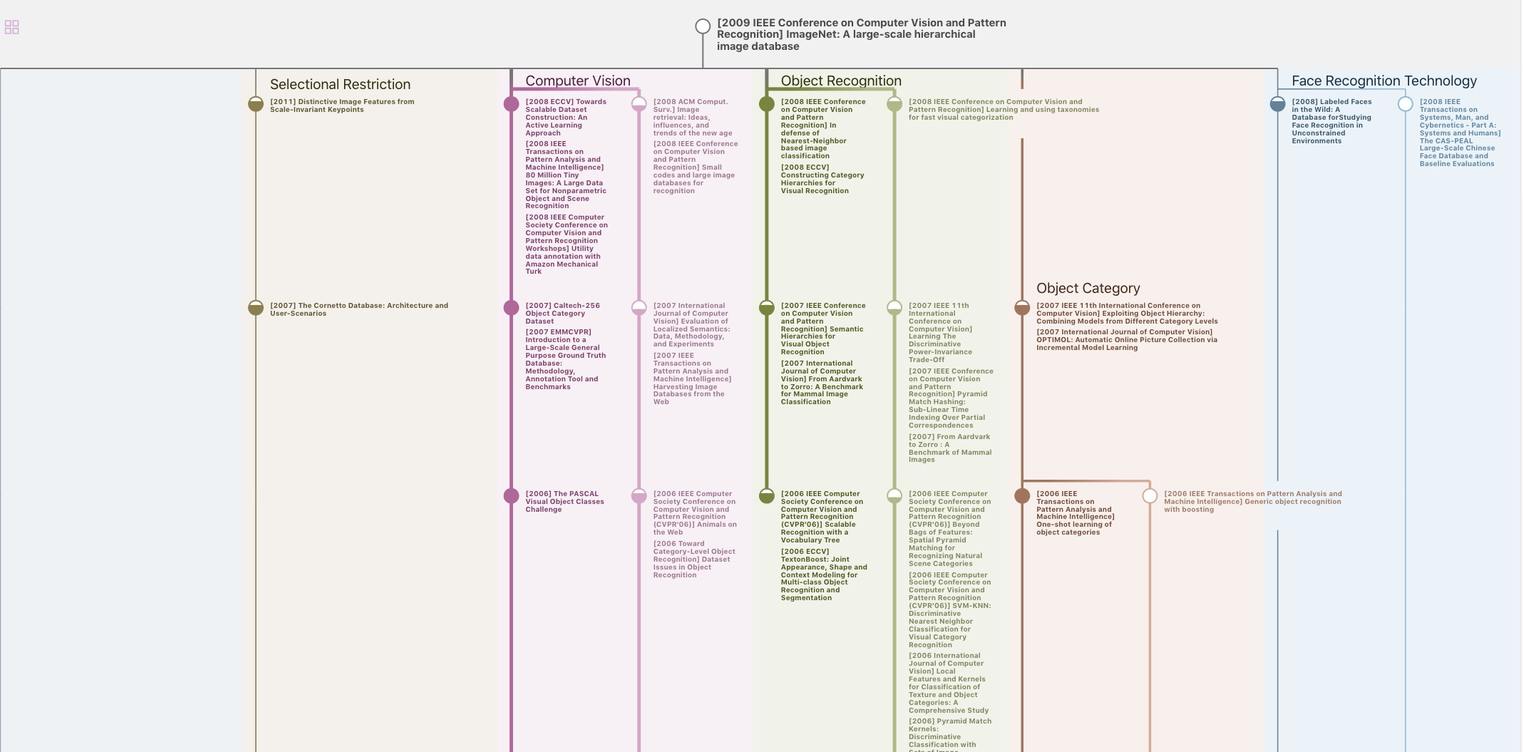
生成溯源树,研究论文发展脉络
Chat Paper
正在生成论文摘要