Spray Trajectory Planning for Complex Structural Components in Robotized Cold Spray Additive Manufacturing
JOURNAL OF THERMAL SPRAY TECHNOLOGY(2024)
关键词
additive manufacturing,cold spray,multiple features,slicing,trajectory
AI 理解论文
溯源树
样例
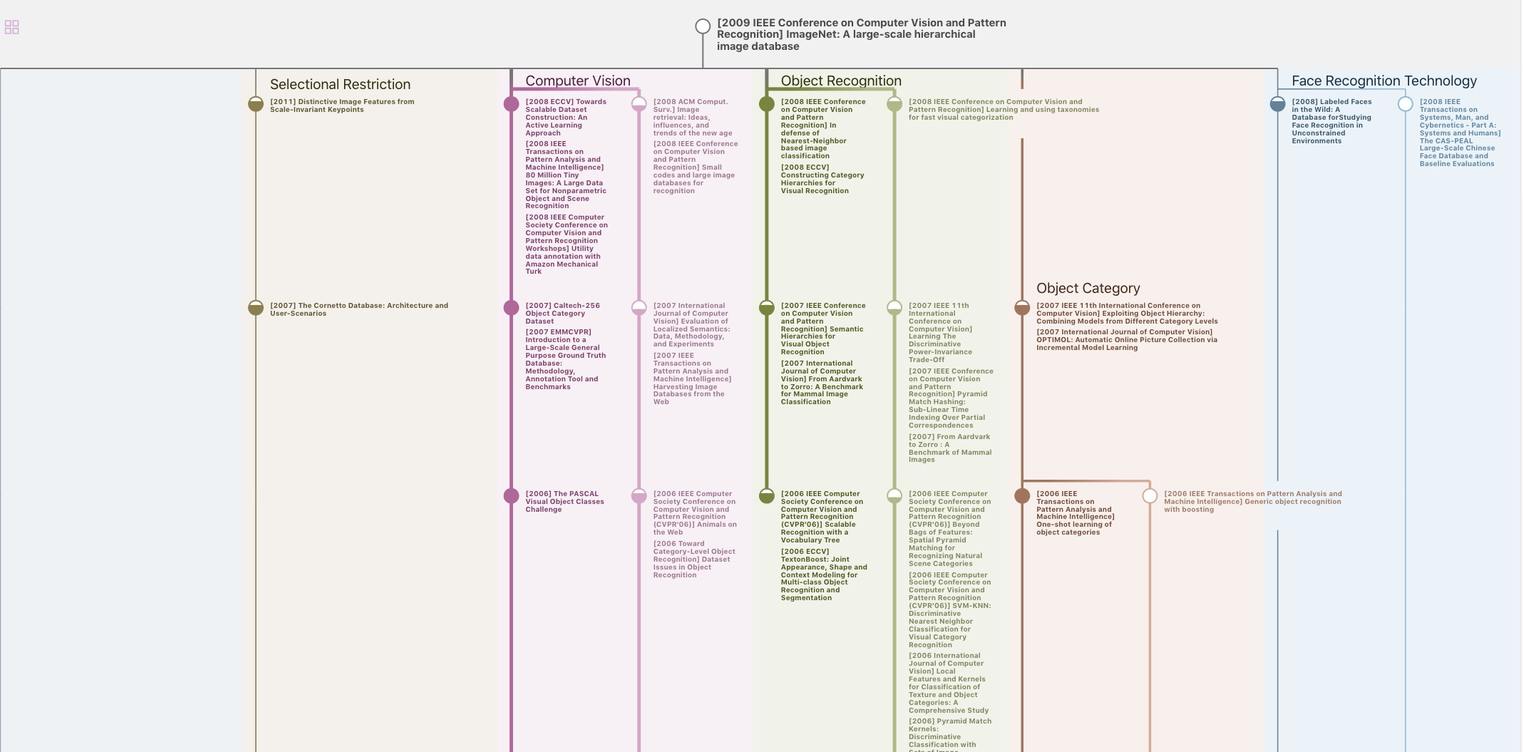
生成溯源树,研究论文发展脉络
Chat Paper
正在生成论文摘要