3D Printed Carbon PEEK - Influence of Printing Strategy on Tensile Performances
Dynamic Response and Failure of Composite Materials(2023)
摘要
Additive Manufacturing, also called 3D printing, plays an increasingly important role in various sectors, including aerospace. Among the most used additive technologies there is Fusion Deposition Modeling (FDM), which offers various opportunities in the printing of thermoplastic polymers by layer-by-layer deposition of the material. Currently, the technology is mainly exploited as rapid prototyping, but the goal in the near future is to use it for the production of mechanical components, especially with high-performance technopolymers, such as Ultem, PEEK and Carbon PEEK [1, 2]. To achieve this goal, process control and repeatability of parts must be increased. Furthermore, the process parameters have to be optimized in order to reduce defects and porosities and to increase the bonding between adjacent filaments within the same layer and between layers. The performances of parts produced in FDM are influenced by many process parameters, such as the material deposition speed, the printing strategy, the layer thickness, the nozzle and working chamber temperature. In the present work the printing strategies of the specimens in Carbon PEEK were studied and their influence on the mechanical tensile performance were evaluated [3]. The specimens were produced by a Roboze Argo 500 3D printer with four different filament deposition strategies (printing orientation: 0°, 90°, ±45°, 0/90°), nozzle temperature of 450 ℃, chamber temperature of 180 ℃, layer thickness of 0.225 mm, nozzle diameter of 4 mm and 100% infill.
更多查看译文
关键词
Thermoplastic materials, Tensile tests, Carbon PEEK, 3D printing
AI 理解论文
溯源树
样例
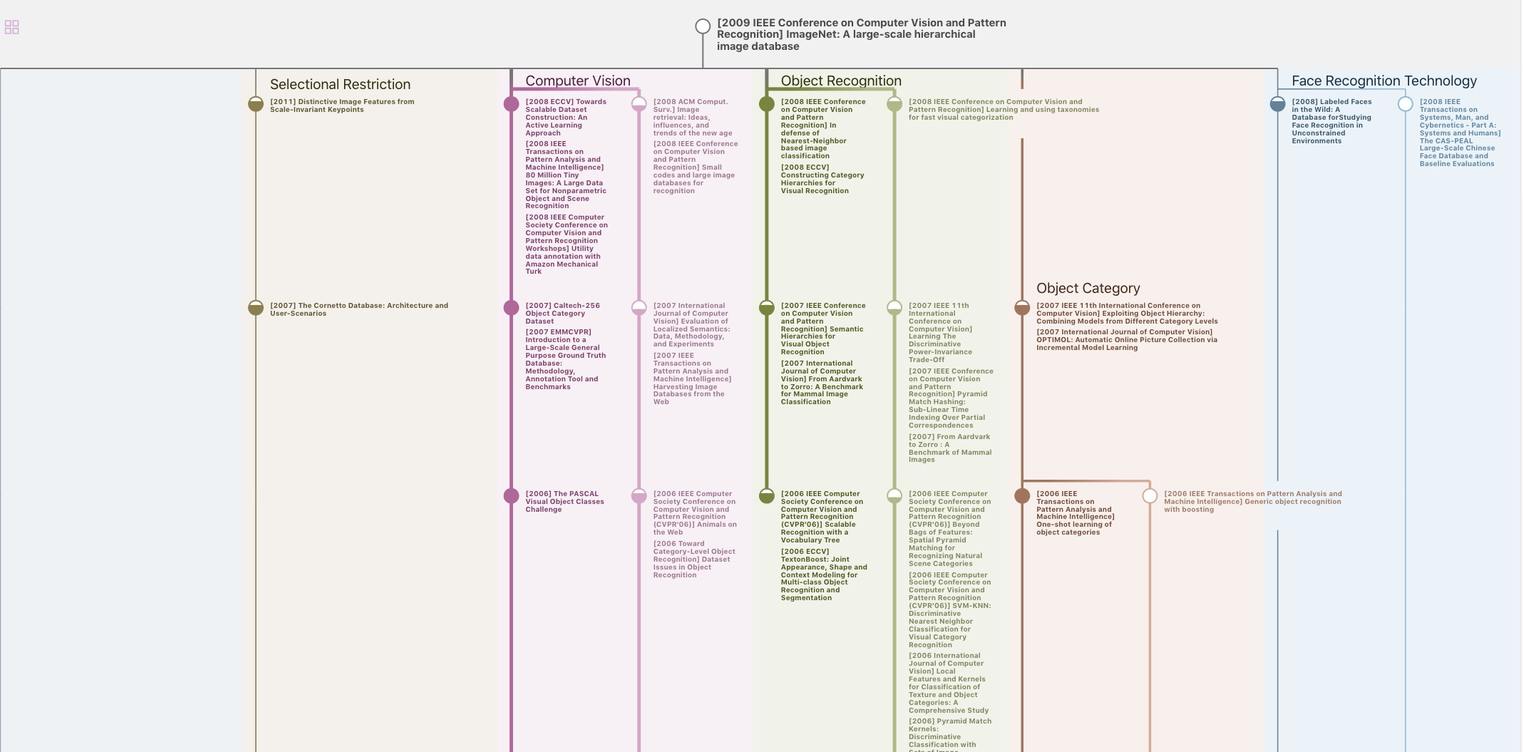
生成溯源树,研究论文发展脉络
Chat Paper
正在生成论文摘要