Tapping stream tracking model using computer vision and deep learning to minimize slag carry-over in basic oxygen furnace
ELECTRONIC RESEARCH ARCHIVE(2022)
摘要
This paper describes a system that can automatically determine the result of the slag dart input to the converter during tapping of basic oxygen furnace (BOF), by directly observing and tracking the behavior of the pouring molten steel at the tapping hole after the dart is injected. First, we propose an algorithm that detects and tracks objects, then automatically calculates the width of the tapping stream from slag-detection system (SDS) images collected in real time. Second, we develop a time-series model that can determine whether the slag dart was properly seated on the tap hole; this model uses the sequential width and brightness data of the tapping stream. To test the model accuracy, an experiment was performed using SDS data collected in a real BOF. When the number of sequential images was 11 and oversampling was 2:1, the classification accuracy in the test data set was 99.61%. Cases of success and failure of dart injection were quantified in connection with operation data such as ladle weight and tilt angle. A pilot system was constructed; it increases the reliability of prevention of slag carry-over during tapping, and can reduce the operator's workload by as much as 30%. This system can reduce the secondary refining cost by reducing the dart-misclassification rate, and thereby increase the productivity of the steel mill. Finally, the system can contribute to real-time process control and management by automatically linking the task of determining the input of darts to the work of minimizing slag carry-over in a BOF.
更多查看译文
关键词
object detection, object tracking, recurrent neural network, steelmaking, tapping operation, slag detection system
AI 理解论文
溯源树
样例
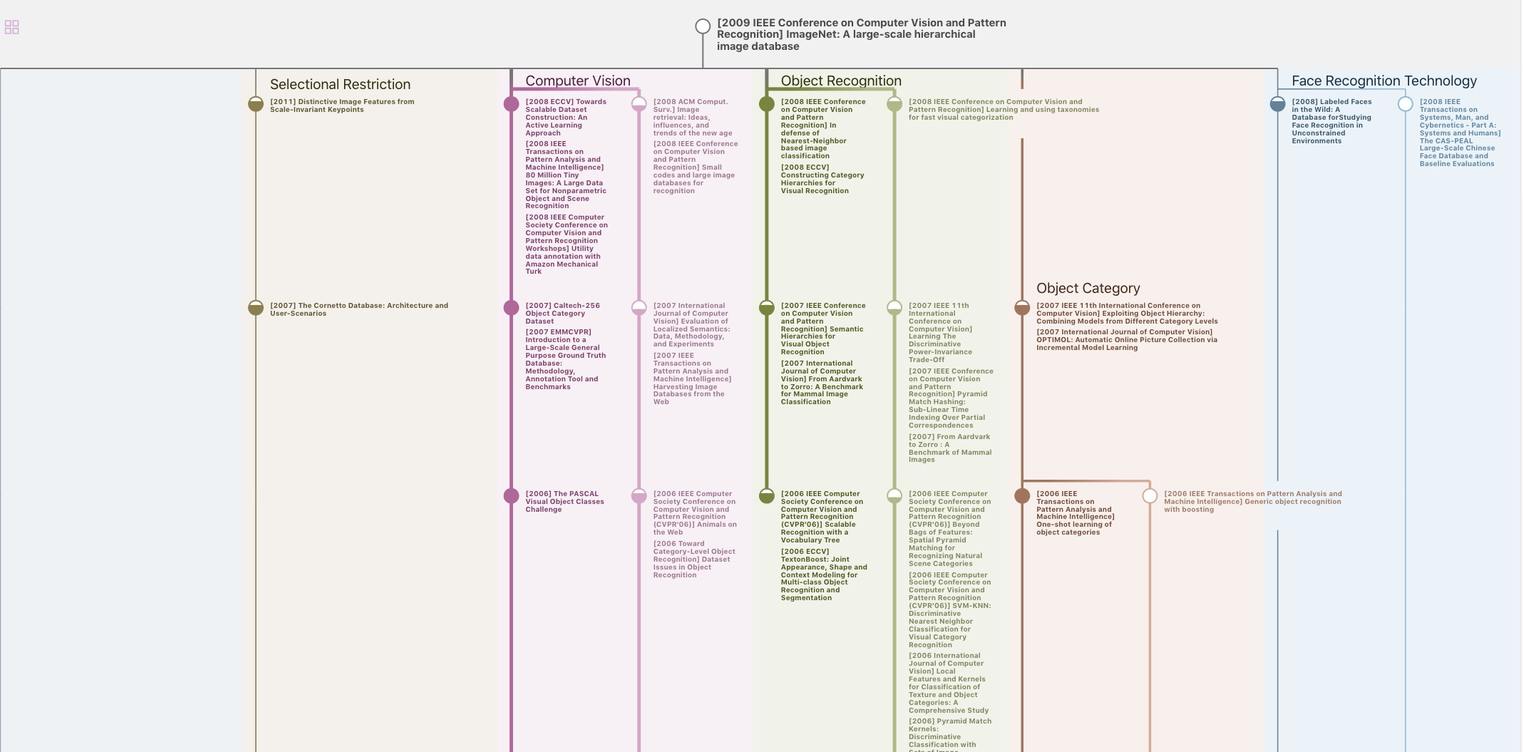
生成溯源树,研究论文发展脉络
Chat Paper
正在生成论文摘要