Development of ultra-light hybrid glass fiber and polymeric fiber reinforced polypropylene composites
semanticscholar(2019)
摘要
It is a trend in the automotive industry to pursue materials with improved strength-to-weight ratio. Light weight reinforced thermoplastic (LWRT) composites represent one type of these desired materials. This study reports development of a new LWRT material with a significantly improved strength-to-weight ratio over standard LWRT materials. A novel ultra-light reinforced thermoplastic composite, which features the mixed usage of glass fibers and bi-component polymeric fibers, is reported. Polymeric fibers provide a low density reinforcement, while glass fiber has better strength and stiffness. Through hybridization, it is possible to design the material to suit various applications more closely. The hybrid effects of glass and polymeric fibers on the flexural and physical properties have been investigated. It has been found that the partial substitution of glass fiber with bi-component polymeric fiber helps further reduce weight without sacrificing the mechanical strength of the material. Introduction and Background In the recent decade, there has been a fast growth in the use of thermoplastic composite materials [1,2]. For example, fiber reinforced composites have been widely employed by the automotive industry for seat backs, door panels, trunk trim, interior parts and headliners [3]. Car manufacturers are constantly pushing to use materials which provide lighter weight, lower cost, and more design freedom. To meet the market demand, it is critical to develop new materials responding to the need for weight reduction and improved formability. Glass fiber reinforced polypropylene (PP) sheets/mats manufactured by wet-laid process, are excellent candidates as headliner materials for their light weight, good formability, and low coefficient of thermal expansion [4]. Normally, an aqueous suspension of well-dispersed thermoplastic resin and chopped glass fiber is transferred onto a web-forming section. A thermoplastic composite sheet can be manufactured by removing the water from the web, heating the web to a temperature above the melting point of the thermoplastic resin, and subsequently consolidating the web. A part can be produced by thermo-forming the thermoplastic composite sheet. During the thermo-forming process, when the resin melts, the residual stress among fibers is released. The thickness of the composite sheet becomes greater than that before being heated. This is a phenomenon called “loft”. In the whole porous structure, resin serves the function of adhesive to hold the chopped fiber together. Further improvement of the formability as well as the strength-to-weight ratio of the wet-laid LWRT composites can be achieved by addition of expanding agents during web forming, which further increase the loft and the porosity of thermoformed parts. In this paper, we will report a novel glass/bi-component polymeric fiber hybrid polyolefin composite prepared by the wet-laid process. The adding of bi-component polymeric fiber with lower density retains more expanding agents, which allows higher degree of expansion at lower basis weight. Therefore, further weight reduction has been achieved without sacrificing
更多查看译文
AI 理解论文
溯源树
样例
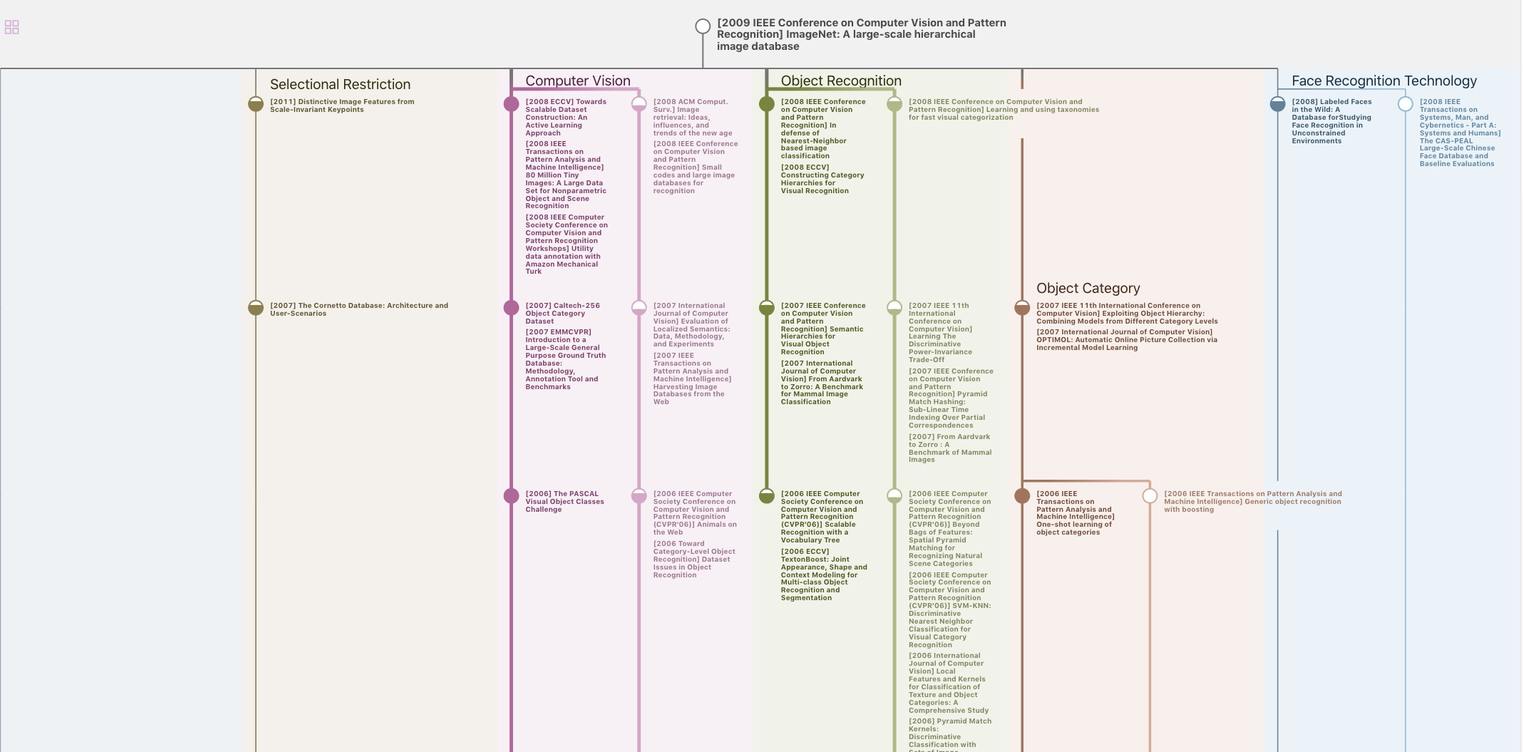
生成溯源树,研究论文发展脉络
Chat Paper
正在生成论文摘要