Distributed optical fibre sensor based monitoring of thermoplastic carbon composite cylinders under biaxial loading: Experimental and numerical investigations
COMPOSITE STRUCTURES(2021)
Abstract
Composite tubes are used in numerous applications including aerospace, mechanical, civil and transport sectors, where they may be susceptible to combined loading especially axial compression and torsion and suffer failure due to their intrinsic weakness under such loads. An experimental cum numerical investigation is performed to understand the behaviour of hollow composite tubes with cut-outs under combined axial compression and torsional loadings. Carbon fibre reinforced thermoplastic CF/PEEK tubes with different diameters and varied lay-up sequences, were robotically manufactured using an Automated Fibre Placement (AFP) machine. These specimens were mechanically tested using a novel biaxial test jig, designed specifically to be compatible with an INSTRON 8852 axial/torsion servo hydraulic test system. A standard acrylate coated optical fibre was affixed on the surface of the cylinder for distributed strain sensing using an optical backscatter reflectometer (OBR) interrogator to obtain spatial strain data. Surface strains measured using distributed optical fibre sensing (DOFS) and strain rosettes were compared against finite element analysis predictions to successfully validate the numerical model created using Ansys ACP Pre-Post simulation package. Directional deformations around the cut-outs of these tubes were also numerically characterised and compared with digital image correlation (DIC) results from the experimental tests.
MoreTranslated text
Key words
Automated Fibre Placement,Thermoplastic,Fibre optic sensor,Structural health monitoring,Biaxial loading,Composites
AI Read Science
Must-Reading Tree
Example
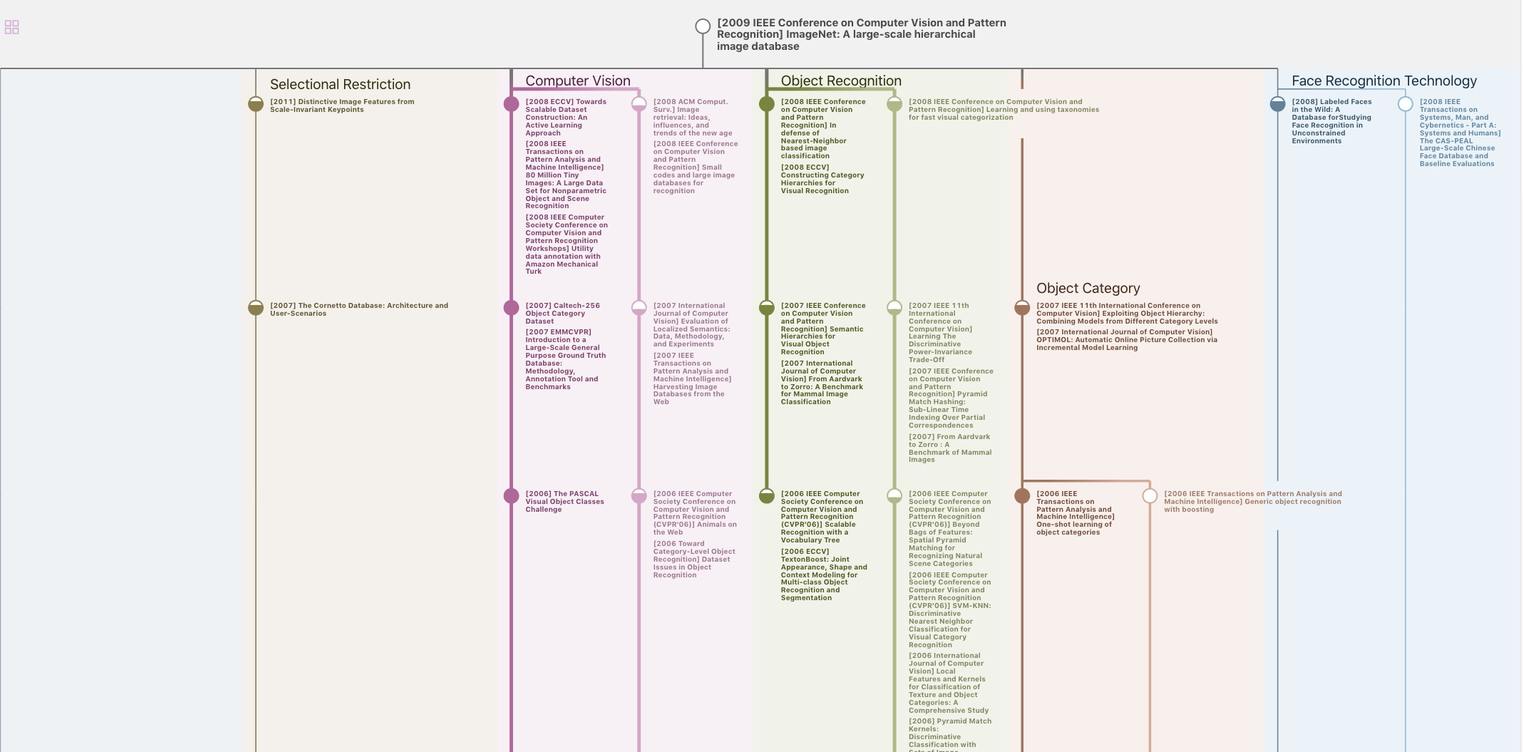
Generate MRT to find the research sequence of this paper
Chat Paper
Summary is being generated by the instructions you defined