Detc 2015-47468 a compliant mechanism design for refreshable braille display using shape memory alloy
semanticscholar(2015)
摘要
Refreshable Braille Display (RBD) is a device that enables people with visual imparity to read digital text through tactile interface. Braille literacy is essential for empowerment of visually impaired people and offers several advantages over auditory aids. Commercially available RBDs have not been able to penetrate the market due to their high cost. Shape memory alloy (SMA) based Braille display is a low cost alternative but faces the challenge of high power consumption, heat accumulation and low refresh rate. This paper discusses the design, analysis and experimental validation of a cantilever based compliant mechanism for SMA based RBD to solve these issues. INTRODUCTION Computers and other digital media have empowered people with blindness by providing them access to digital text through auditory outputs. Audiotapes and computers that ‘speak’ a text through a voice synthesizer program provide access to digital content, but they fail to facilitate reading. Graphs and diagrams are difficult to describe orally; they can be clearly explained using a tactile interface [1]. Braille literacy is not only important to read textbooks and documents, but it is also useful in a variety of other ways like labelling everyday items of usage, e.g. cans of food, medicine bottles, etc. and playing board games such as scrabble [1]. A study reveals that those who learnt Braille had ∗Address all correspondence to this author. higher employment rates, were better educated and financially self-sufficient than the people who relied on auditory aids [2]. However, commercially available Braille displays that use piezoelectric technology are typically priced in the range of 2500 4000 USD (65 100 USD per Braille character cell) and are thus inaccessible to users in both developed and developing countries [3, 4]. Thus, affordable Braille displays based on an alternate technology need to be developed to allow deeper penetration of RBDs among the blind population. This paper presents the design and development of RBDs employing SMA based actuation which builds on the previous paper [5] and addresses the issues of high power consumption, heat accumulation, short lifecycle and Braille cell height in [5]. This paper primarily discusses: • design and assembly of a mechanism where SMA wires are kinematically coupled with a metal cantilever, producing the desired controlled actuation of the Braille dots, • theoretical estimation, optimization and experimental validation of power consumption and actuation time of the RBD, • design of a digital control for the electromechanical assembly that employs time division multiplexing (TDM) to reduce the peak current supply to the Braille cell, • Computational fluid dynamics (CFD) analysis and design of active and passive cooling systems for maintaining the operational temperature, • statistical modelling and tolerance analysis of the design to identify critical parameters for further controlling the cell manufacturing process, 1 Copyright © 2015 by ASME • fatigue life estimation of various configurations of the actuator design, and • physical realization of the proposed design in modules of eight cells. RELATED WORKS Researchers have explored a number of ways to design micro actuators to make a functional RBD. References [6, 7] provide comprehensive overview of these technologies and also review the same. Current attempts focus at developing affordable refreshable Braille displays while satisfying the requirements and specifications of Braille display systems given in [8]. There have been multiple attempts at identifying potential technologies that offer high performance at a lower cost. Reference [9] has detailed comparison of the technologies used to build actuators. Reference [10] explores the potential of electroactive polymers (EAP) in the development of RBDs and also highlights the current challenges being faced. RBDs based on Micro-electromechanical systems (MEMs) are currently facing the problem of damage due to mechanical load touch, reliability issues, insufficient linear motion and force to stimulate touch sensation [6]. RBDs employing pneumatic systems have portability issues and can be noisy. Till date, no affordable RBD has been made commercially available that satisfies the functional device requirements. SMA based actuators offer several advantages such as high power to weight ratios (allowing development of miniature actuators), noiseless operation, high reliability, large recoverable strains, high electrical resistivity (thus avoiding need of separate heating elements) and design flexibility [11]. Given the dimensional constraints and affordability issues of the product, SMA suits as a viable alternative to piezoelectric technology in making RBDs. Prior attempts at developing SMA based tactile displays have been reviewed in [5, 7]. Some actuator designs use a vertical configuration of SMA wire which necessitates the Braille pin to remain in ‘up’ position in the un-actuated state. On an average, 3 out of 8 Braille pins remain up in digital Braille format which means 5 actuator elements need to pull the Braille pin down. This increases the power consumption of the device. Reference [12] uses a pivot to amplify the displacement of SMA wire and [13] uses a locking mechanism to latch the Braille pin. Both these designs involve tiny moving components which lead to manufacturing complexity and higher cost. Some designs use SMA springs to actuate the Braille dot. Although the use of springs lowers the overall height of the device, it has a slower cooling rate and higher power consumption in comparison to SMA wires. The proposed design uses SMA wire as an actuator and addresses these issues and explores the cooling system designs to solve the heat accumulation problem. SHAPE MEMORY ALLOY ACTUATION SMAs exhibit thermo-mechanical properties which are a result of their reversible diffusion-less transformation between high temperature austenite and low temperature martensite phase. SMAs are able to memorise and recover from an original shape, after they have been deformed by heating over their transformation temperature. This unique effect of returning to an original geometry after a large inelastic deformation (near 10%) is known as the ‘shape memory effect’. This property is exploited in development of various industrial actuators. Reference [14] explains the shape memory effect and discusses some of its applications. Out of the several alloys that exhibit shape memory effect, NiTi (45 51% of Ti) has been a standard choice for use in space and many other applications. Other merits of using shape memory actuators and their applications have been discussed in [15]. Disadvantages of SMA based actuators include higher current and power consumption and lower actuation frequency (limited by slow SMA cooling rate). REFRESHABLE BRAILLE CELL DESIGN Constraints The proposed design of the cell considers, both − spatial constraints and operational constraints. Spatial constraints are derived from various standards practiced internationally. Prescribed sizes and spacing of Braille character according to different standards are given in [16]. The Braille dot can be raised above the surface anywhere between 0.6 − 0.9 mm for easy tactual sensing. Operational constraints define the user desired functionalities of an RBD and are derived through user interaction. These constraints are as following. • An RBD is expected to last 2-3 years with seamless use which is equivalent to ∼ 107 actuation cycles for a single line RBD. • A refresh rate (the rate at which a Braille dot extends and retracts) of 5 Hz is recommended, but 1 Hz may be tolerable for some applications with limited interaction [8]. • A minimum resistive force (the force that a Braille dot can bear without going below surface) of 0.15 N is required [8]. Actuator Design Pro-longed life cycle of the actuator was the primary concern towards the design of the Braille cell. To achieve this, stress and strain in the SMA wire needed to be reduced. The proposed actuator design amplifies the contraction of the SMA wire using a cantilever type of compliant mechanism which leads to strain reduction in the SMA wire in the actuated state. This further reduces the power required to actuate and sustain the temperature of the SMA wire as well as improves its life. Figure (1) shows 2 Copyright © 2015 by ASME the schematic diagram of the compliant actuation mechanism. When current is passed through the SMA wire, it heats up (due to Joule heating effect) and contracts which leads to elastic deformation of the cantilever. Due to this deformation, the Braille dot is raised above the top surface of the display. The dots can then be felt using fingers. Once the passage of current to the SMA wire is stopped, it cools down, elastic strain in the cantilever is released and the Braille dot falls to its default position due to gravity. The dimensions of the ‘triangle’ (points A, B and C in Fig. (1)) formed by the metal strip, SMA wire and the plastic body have been determined using exhaustive search method of optimization. An iterative program was made in Microsoft Excel that calculated the stress and strain in the wire for every possible combination of the input parameters. The objective function minimizes the stress and strain in the SMA wire conforming to the following constraints: • stress in metal strip (cantilever) should be less than its elastic limit to avoid plastic deformation, • height of the Braille cell should not exceed 30 mm, and • amplification ratio of the cantilever should not be too large; larger ratio would lead to unwanted actuation even with small fluctuations in the ambient temperature and input current. The values have been so chosen to take care of the spatial and operational constraints. The following equations were derived (using the results of [17]) to calculate the actuation of the Braille dot: δ = Fsinβ∗a2(3L−a) 6EI −6Fcosβ∗a2 (1) β = sin−1( lwsinθ−δn
更多查看译文
AI 理解论文
溯源树
样例
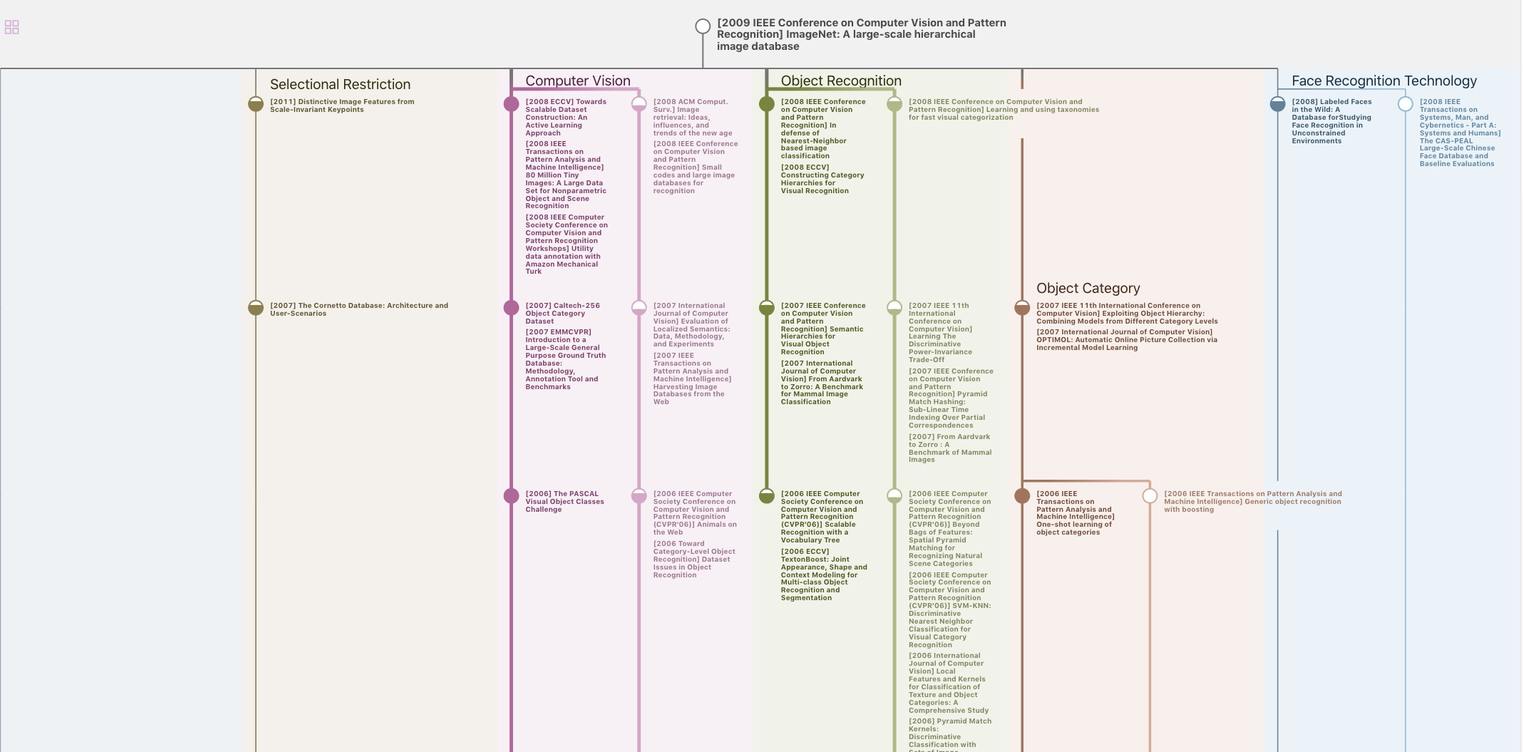
生成溯源树,研究论文发展脉络
Chat Paper
正在生成论文摘要