Fatigue Performance Of Polyamide 12 Additively Manufactured Structures Designed With Topology Optimization
JOURNAL OF TESTING AND EVALUATION(2021)
摘要
Additive manufacturing technologies can produce structures with complex geometry, generally as time goes on at higher levels of quality and repeatability. Complex geometry is attractive because it allows for mass redistribution to structural regions where stress is highest, which is comparatively advantageous to solid section designs. Additively manufactured structures, however, are sensitive to stress concentrations either from geometry or defects reducing the overall strength and fatigue performance. It is, therefore, important to address stress concentrations from a design perspective, formulating a process that ensures fatigue performance. A topology optimization process is presented for designing a beam subjected to three-point loading with objectives to reduce structural volume/mass while representing the expected fatigue life as a function of the stress. The design process produced structures with between 28 and 67 % of the original volume of material for a given volumetric constraint with material redistributed to reduce stress concentrations. Two designs were fabricated of polyamide 12 using selective laser sintering and tested mechanically to failure under quasistatic and cyclic fatigue loading. Experimentally, digital image correlation was used to observe the onset of failure and strain response in the structure, which showed that vertical members typically failed by buckling and material yielding. Load, displacement, cycles to failure, and heat generation were measured during fatigue loading, capturing significant viscoelastic self-heating and plasticity behavior in the vertical structural members.
更多查看译文
关键词
topology optimization, fatigue, digital image correlation, TOSCA, additive manufacturing, polyamide 12
AI 理解论文
溯源树
样例
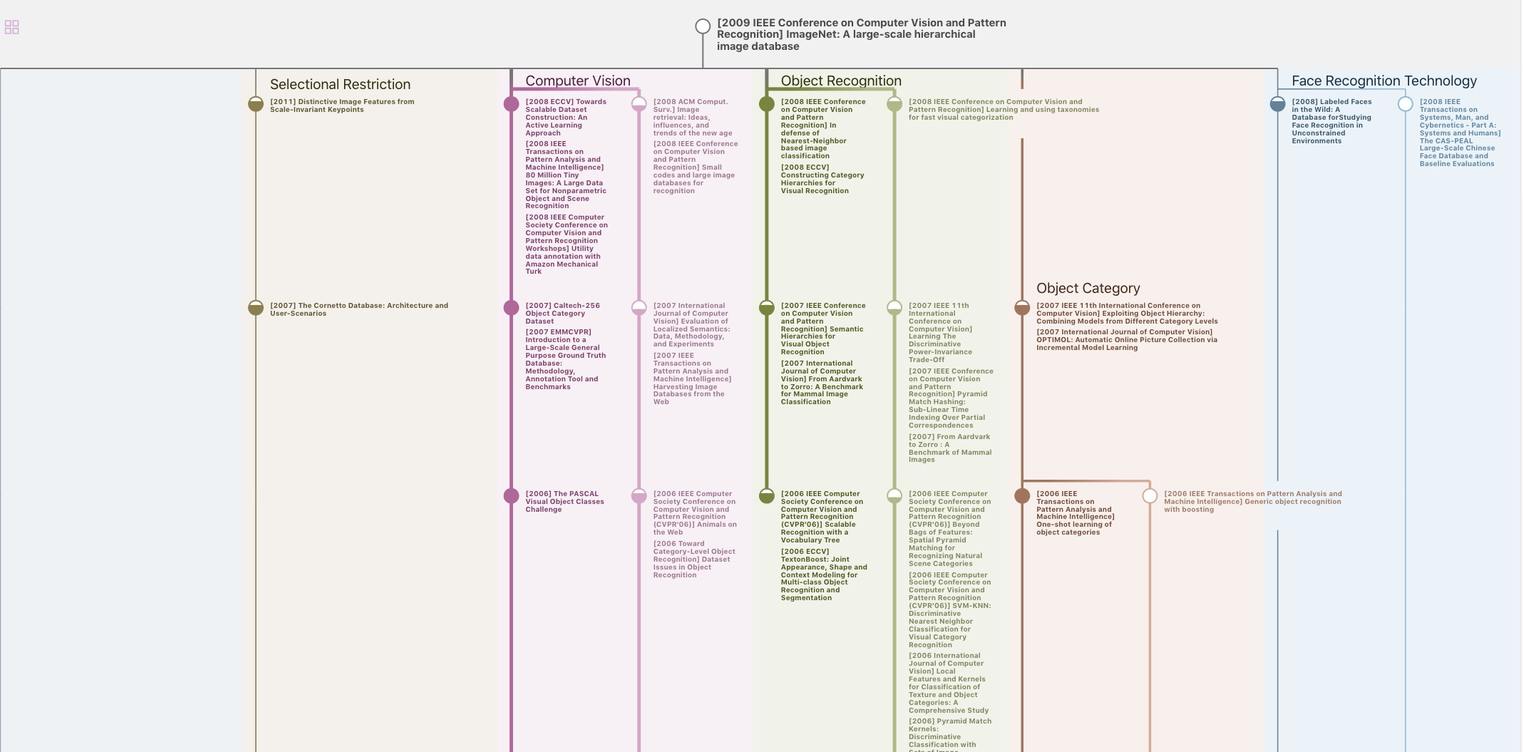
生成溯源树,研究论文发展脉络
Chat Paper
正在生成论文摘要