Boundary-conforming finite element methods for twin-screw extruders using spline-based parameterization techniques
Computer Methods in Applied Mechanics and Engineering(2020)
摘要
This paper presents a novel spline-based meshing technique that allows for usage of boundary-conforming meshes for unsteady flow and temperature simulations in co-rotating twin-screw extruders. Spline-based descriptions of arbitrary screw geometries are generated using Elliptic Grid Generation. They are evaluated in a number of discrete points to yield a coarse classical mesh. The use of a special control mapping allows to fine-tune properties of the coarse mesh like orthogonality at the boundaries. The coarse mesh is used as a ‘scaffolding’ to generate a boundary-conforming mesh out of a fine background mesh at run-time. Storing only a coarse mesh makes the method cheap in terms of memory storage. Additionally, the adaptation at run-time is extremely cheap compared to computing the flow solution. Furthermore, this method circumvents the need for expensive re-meshing and projections of solutions making it efficient and accurate. It is incorporated into a space–time finite element framework. We present time-dependent test cases of non-Newtonian fluids in 2D and 3D for complex screw designs. They demonstrate the potential of the method also for arbitrarily complex industrial applications.
更多查看译文
关键词
Co-rotating twin-screw extruder,Elliptic grid generation,Isogeometric analysis,Space–time finite elements,Boundary-conforming finite elements,Non-isothermal flow
AI 理解论文
溯源树
样例
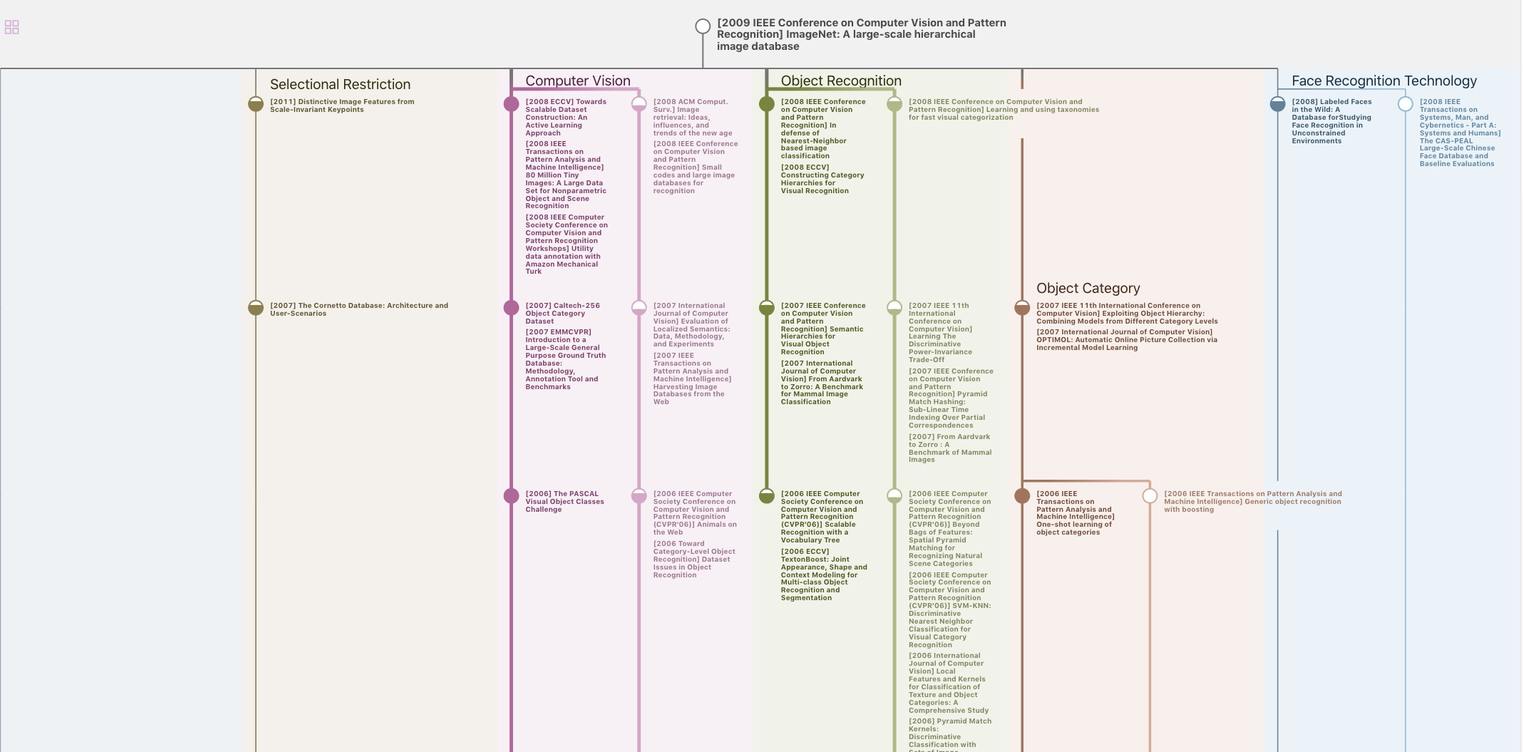
生成溯源树,研究论文发展脉络
Chat Paper
正在生成论文摘要