Failure Mechanism and Solution Study of IC Wire Bond Heel Crack on Leadframe
EPTC 2008 10TH ELECTRONICS PACKAGING TECHNOLOGY CONFERENCE, VOLS 1-3(2008)
Abstract
Many discussion and activity were focusing on the 1st bond (ball bond) on fine pitch for IC wire bonding in the past few years. However, the industry has been getting more and more challenges on the 2nd bond (stitch bond) to seek the robust interconnect solutions. The weak bond and heel crack are two major issues in terms of the manufacturability and reliability especially on the metal leadframe with tape underneath, i.e., copper leadframe with NiPdAu plating for packaging of MAP QFN, Power QFN, MLP, etc. The contamination from the reflow process of solder die attach material will make the bondability of 2nd bond much worse. For automotive applications, the crescent quality of 2nd bond is very critical to pass the stringent reliability requirements. Some paper [1] discussed the heel crack at stitch bond during molding process. Some paper [2] discussed the heel crack failure during temperature cycling test because of the low adhesion strength between the noble metal finish of the PPF leadframe and epoxy molding compound. This article will show that heel crack can be induced by the improper structure of frame because of the sympathetic vibration of the frame at local area when the ultrasonic power applied during bonding process at TO. It can significantly reduce the sympathetic vibration thus avoiding the over-bond of the crescent (heel crack) by modifying the frame structure at local area. Besides, possible ways to solve the weak bond and heel crack and how to improve the crescent quality at TO were discussed including bonding tool selection, parameter optimization (using security bump and tail scrub to reduce ultrasonic power) by a case study on PQFN package (PPF leadframe using solder paste die attach). By these efforts, the adhesion strength of the stitch bond on the PPF surface with poor bondability has been able to be improved significantly without the risk of heel crack even after the 500 cycles of Temperature Cycling- - test (-65 C to 150 C). The failure mechanism of heel crack caused by sympathetic vibration has been also tried to be explained by FEA modeling in this paper.
MoreTranslated text
Key words
cracks,finite element analysis,integrated circuit packaging,lead bonding,vibrations,FEA modeling,IC wire bonding,MAP,MLP,bonding tool selection,copper leadframe,heel crack,parameter optimization,plating,power QFN package,power qual flat nonlead package,reflow process,solder die attach material,sympathetic vibration,temperature cycling test
AI Read Science
Must-Reading Tree
Example
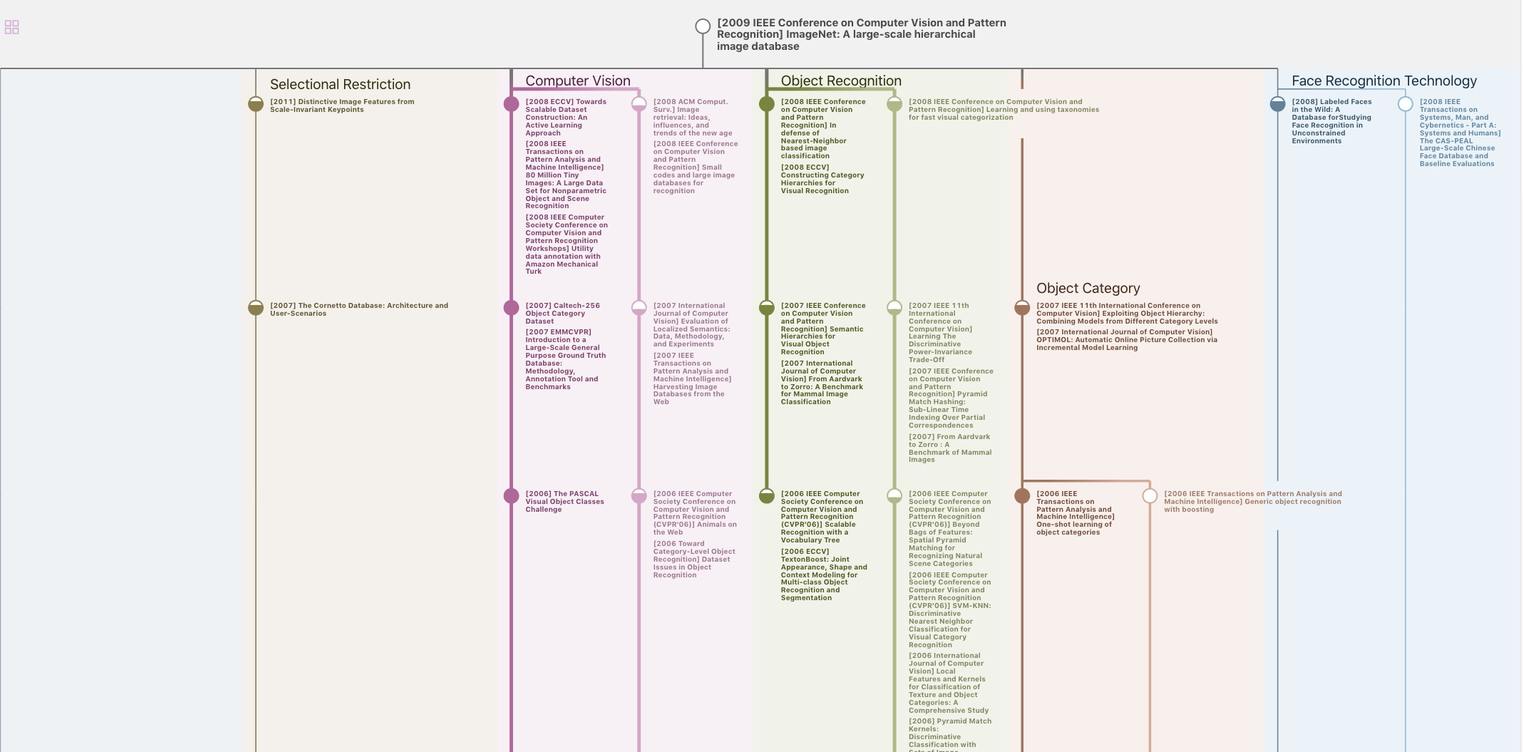
Generate MRT to find the research sequence of this paper
Chat Paper
Summary is being generated by the instructions you defined