A Finite Element Model Of The Squeeze Casting Process
INTERNATIONAL JOURNAL OF NUMERICAL METHODS FOR HEAT & FLUID FLOW(2006)
摘要
Purpose - To present a numerical model of squeeze casting process.Design/methodology/approach - The modelling consists of two parts, namely, the mould filling and the subsequent thermal stress analysis during and after solidification. Mould filling is described by the Navier-Stokes equations discretized using the Galerkin finite element method. The free surface is followed using a front tracking procedure. A thermal stress analysis is carried out, assuming that a coupling exists between the thermal problem and the mechanical one. The mechanical problem is described as an elasto-visco-plastic formulation in an updated Lagrangian frame. A microstructural solidification model is also incorporated for the mould filling and thermal stress analysis. The thermal problem is solved using enthalpy method.Findings - During the mould-filling process a quasi-static arbitrary Lagrangian-Eulerian (ALE) approach and a microstructural solidification model were found to be applicable. For the case of the thermal stress analysis the influence of gap closure, effect of initial stresses (geometric nonlinearity), large voids and good performance of a microstructural model have been demonstrated.Research limitations/implications - The model can also be applied to the simulation of indirect castings. The final goal of the model is the ability to simulate the forming of the material after mould filling and during the solidification of the material. This is possible to achieve by applying arbitrary contact surfaces due to the sliding movement of the cast versus the punch and die.Practical implications - The presented model can be used in engineering practice, as it incorporates selected second-order effects which may influence the performance of the cast.Originality/value - During the mould-filling procedure a quasi-static ALE approach has been applied to SQC processes and found to be generally applicable. A microstructural solidification model was applied which has been used for the thermal stress analysis only. During the thermal stress analysis the influence of gap closure and initial stresses (geometric nonlinearity) has been demonstrated.
更多查看译文
关键词
couplers, thermo-mechanical separation, fluid dynamics, solidification, modelling, finite element analysis
AI 理解论文
溯源树
样例
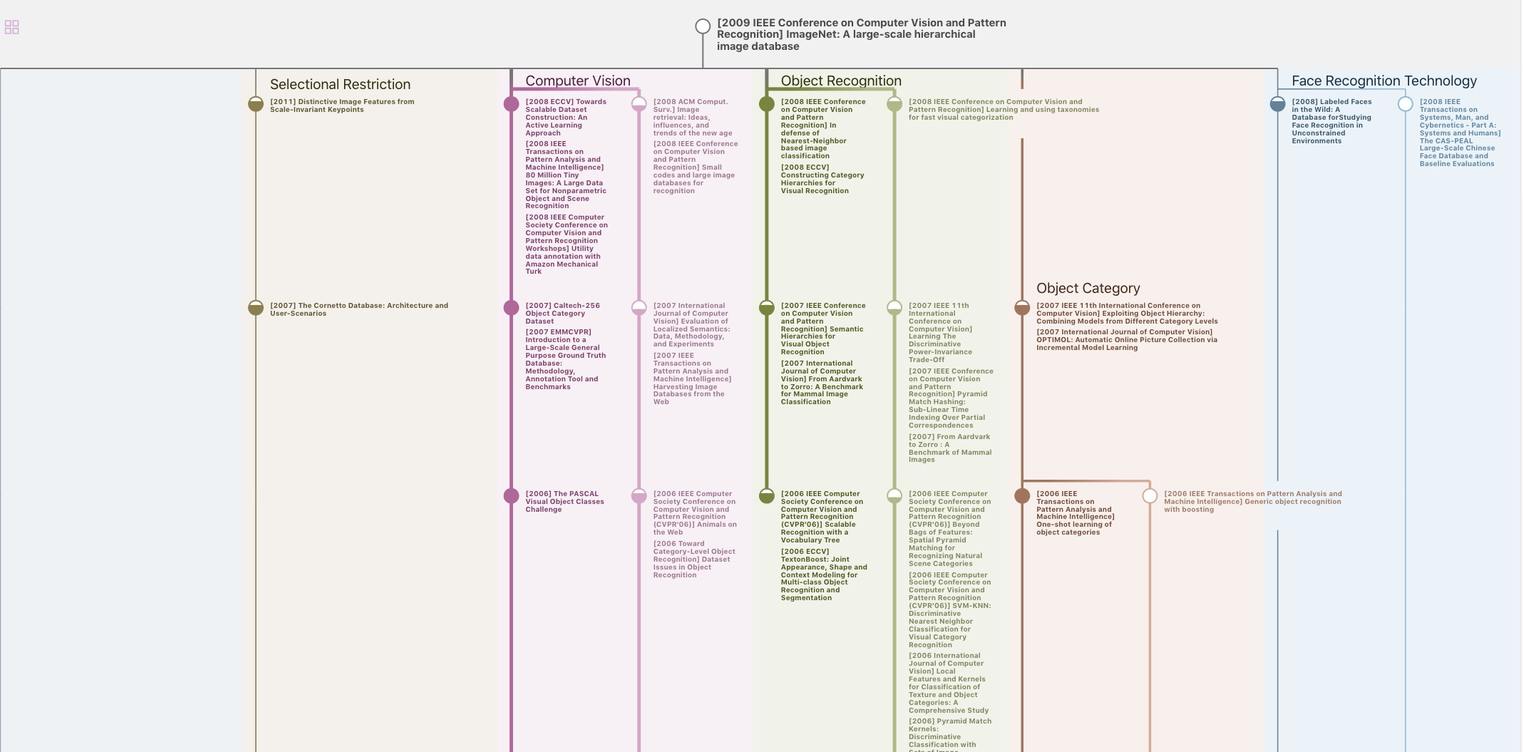
生成溯源树,研究论文发展脉络
Chat Paper
正在生成论文摘要