Treatment of sugar factory effluent biological trickling filters
msra(2009)
Abstract
In a high rate filter rapid production of biological film takes The biological degradation of sugar factory effluent by place and if the void spaces in the packing are insufficiently trickling filters was investigated in a pilot plant. The process large blockage of the filter will occur. In conventional filters was found to be suitable provided additional nitrogen and 75-150 mm stones or other media are used for this reason. For secondary filters smaller packing material is adequate as phosphorus were added. The cost of trickling filters and other the lower loading of these filters results in less bio-mass biological oxidation processes were compared. accumulation. For small scale filters the depth should be identical to the Introduction full scale depth which for gravel filters is normally2 metresg. For Factory effluents contain mainly organic waste, small plastic media towers having a depth up to 8 m can be used. amounts of salts and no toxic substances. This type of effluent However, greater depth is usually specified to save floor space can be treated by anaerobic or aerobic biological treatment, and filters of different depth normally show similar efficiencies or a combination of both. at similar loads of BOD per unit volumelo. Although anaerobic degradation greatly reduces oxygen demand the effluent of this treatment will not meet the required standard in South Africa (COD < 75 mg/R) and the process will invariably lead to odour problems, which would only be tolerable at some distance from a factory or housing scheme. Various aerobic processes are applied for organic waste degradation: activated sludge, biological filtration and aeration in fermentation tanks. The aerobic activated sludge process for sugar factory effluent has been described in Australia1. The importance of the addition of nitrogen and phosphorus in this process has been stated by various auth0rs~~~94. Aeration of waste water in a pilot plant fermenter was described by Revuz5. The mixed liquid suspended solids content was kept very high in this fermenter (40 000 mg/R) and no solids were discharged. The BOD dropped from 4 600 mg/R to 300 mg/R after 4 hours retention. A modification of the activated sludge process in the form of a ditch, and applied to sugar factory effluent, was described by Ashe 6 9 7 . This type of activated sludge plant is used by many small municipalities in Europe for the treatment of domestic e f f l~en t .~ Biological trickling filters for purification of sugar factory effluent have been used by Rennie. An experimental biological trickling filter at Darnall operated successfully at a load of 1 kg COD/m3 per day. The main advantages of a trickling filter over an activated sludge process are the insensitivity to overloading and easier operation. In order to obtain more data on the operation of trickling filters for the treatment of sugar factory effluent a pilot plant was constructed at the SMRI. Construction of the pilot plant Factory effluent has a COD between 1 500 and 15 000 mg/R and the industrial average is 3 000 mg/R. The COD : BOD ratio for untreated factory effluent is approximately 2 : 1. Effluent having a higher COD content than 500 mg/R cannot be treated in a single stage filtration plant and two stages are usually employed. The first unit is operated as a high rate filter, removing 50-60% of the oxygen demand and the second unit is operated as a low rate filter, which has to provide an effluent conforming to the standards laid down for sugar factory effluent. As alternatives to conventional filter media various prefabricated plastic media are available. These materials are designed to provide a high specific surface and large void spaces to reduce blockages. Table 1 shows the properties of these media. TABLE I Packing media for biological filters I I 1 Specific Surface Medium VoidoSpace / f a m2/m3 To avoid too much influence on the process from wall effects the ratio of the diameter of the packing medium to the diameter of the filter should be at least l : 811. Thus for example in a low rate filter, 25 mm diameter medium can be used in a cylinder of 200-300 mm diameter. Blast furnace slag . . . . . . Flocor . . . . . . . . . Surf pac (crinkle-close) . . . . . Surf pac (standard) . . . . . . Cloisonyle . . . . . . . . Smooth rock . . . . . . . . A conventional medium for a high rate filter would require a cylinder with a diameter of 800-1 200 mm, which would be inconveniently large for laboratory experiments and would require large quantities of effluent. For this reason a plastic medium was used for the high rate filters and of the 3 packing media listed in Table 1 Cloisonyle was considered the most suitable for small scale experiments. 13,4 26 56 25 66 13,4 Cloisonyle has one of the highest specific surfaces of all packing media and the efficiency of a trickling filter is proportionate to the specific surface12. The suppliers of Cloisonyle claim a possible load of 3,4 kg/m3 per day for domestic sewage as compared to a load of 0,3-0,5 kg BOD/m3 per day for conventional media. Cloisonyle medium could therefore be expected to accept about 8 times higher loading than a filter using conventional stone media. It has been shown by Gameson et all3 that considerable differences can occur in the performance of apparently identical filter units. Because of this variation 3 replicate filters were used in parallel to obtain a measure of the variation in operational efficiency and to get meaningful results. Proceedings of The South African Sugar Technologists' Association JunelJuly 1975 23 A flow diagram of the pilot plant is shown in Fig. 1. The effiuent storage tanks were made of galvanised steel, painted plant consisted of 2 identical units having 3 high rate filters inside with epoxy paint. Further construction materials and followed by 3 low rate filters with a settling tank after each piping were plastic and asbestos cement. A picture of the plant filtration step. is shown in Fig. 3. One unit operated on synthetic effluent to which nitrogen and phosphorus had been added, the other unit on synthetic effluent without additional nutrients. Synthetic effluent was used for easier operation and was made up by mixing molasses, sugar and water. The capacity of the feed tanks was such that a new mixture was prepared twice a week. The effluent was evenly distributed over the filters by acrylic plastic pipes with holes rotating at 9 rpm. (See Fig. 2). The surface area of the high rate filters was 0,039 m2, that of the low rate filters was 0,031 m2. The latter were packed with stone of 25 mm diameter. The height of all filters was 2 m. To prevent the possibility of inhibition of bacterial growth, metals were avoided in the construction of the plant. The FIGURE I Flow diagram of pilot plant. I. Synthetic effluent supply tank. 2. Constant head and recirculation tanks. 3. High rate filters. 4. Low rate filters. 5. Sedimentation tanks. FIGURE 3 Pilot plant. FIGURE 2 Distributor. Synthetic effluent was prepared as shown in Table 2. TABLE 2 Composition of synthetic effluent During the experiments the load on the filters was varied in some cases by changing the flow rate to the filter. In a number of cases the molasses and sucrose concentration was changed while the flow was kept identical. This was done to avoid the manufacture of new orifice plates to control the flow every time a change in filter loading was carried out. Molasses . . . . . . . . . . . . . Sucrose . . . . . . . . . Nitrogen (as urea, 46%' ~j . . . . . . . . . . Phosphorus (as super phosphate 8,3 0/6) Water . . . . . . . . . . . . . COD mg/R . . . . . . . . . . . . . . . . . . . BOD mg/R The ratio of molasses to sucrose was always kept at 2 : 1, N and P were added in such a way that COD : N : P was 100 : 2 : 0,4 during the earlier experiments. The last experiments were carried out doubling the concentration of N and P. 6 000 g 3 000 g 128 g 27 g 2300 R 3 500 4 000 2 000 2 300 24 Proceedings of The South African Sugar Technologists' Association JunelJuly 1975
MoreTranslated text
AI Read Science
Must-Reading Tree
Example
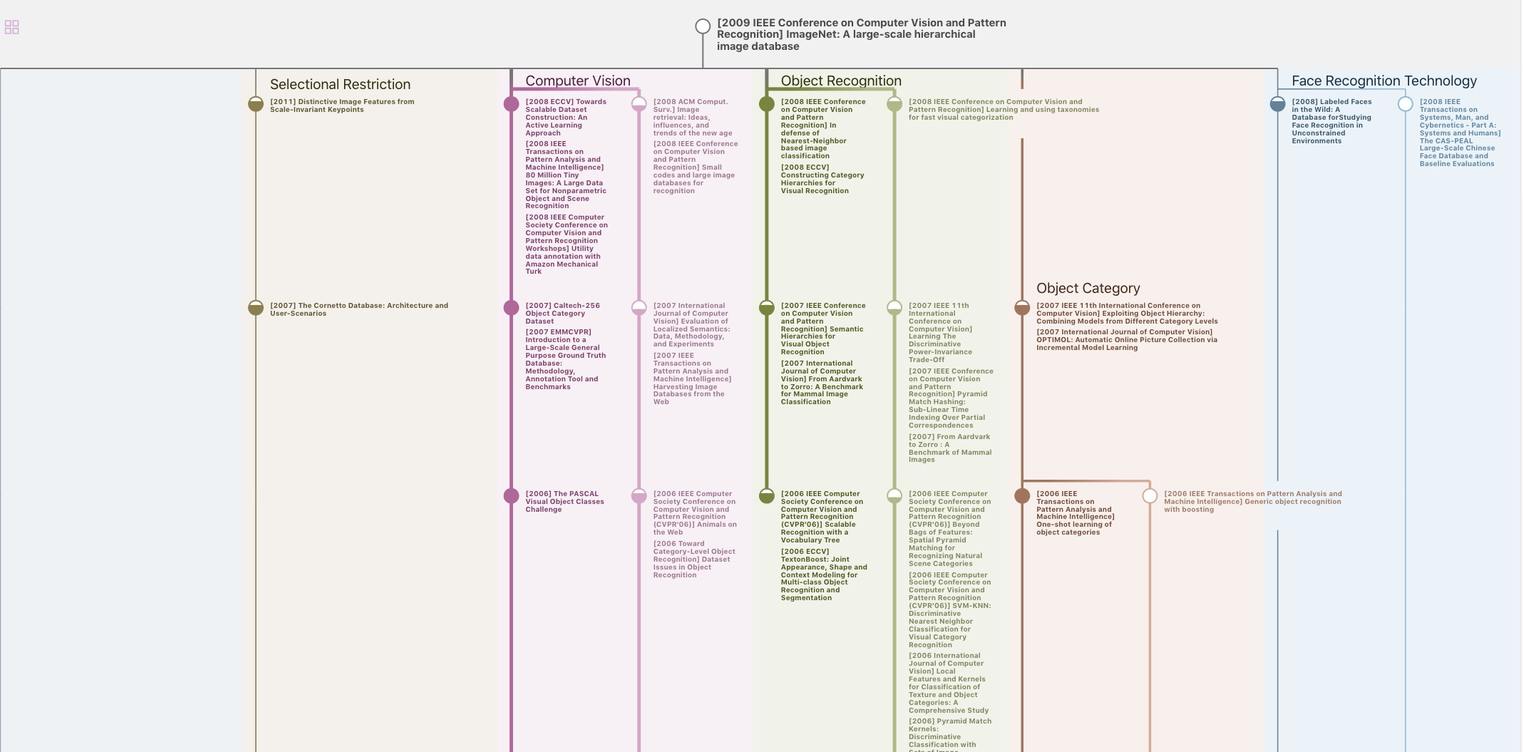
Generate MRT to find the research sequence of this paper
Chat Paper
Summary is being generated by the instructions you defined