Research on the mechanism and control methods of mechanical drift in linear ultrasonic motors
SMART MATERIALS AND STRUCTURES(2024)
Abstract
Linear ultrasonic motors (LUMs) have advantages such as de-energized self-locking and micro-nano displacement resolution. However, their positioning and control accuracy are negatively affected by mechanical drift, which limits their application in ultra-precision fields. To date, the quantitative mechanism of LUM mechanical drift under power-off conditions remains unreported. To solve the problem, we employ the creep theory to identify the clamp stiffness parameters and consider the internal friction and stick-slip effects of the slider, thereby establishing a non-autonomous dynamic model of the LUM mechanical drift in the power-off state. Subsequently, we utilize this model to investigate how the LUM's structural parameters influence mechanical drift and explore methods to mitigate this undesirable phenomenon. Finally, we validate the model's validity through experimental research. Our findings reveal that structural creep is the primary cause of mechanical drift in LUMs. Increasing the tangential stiffness of the clamp component and slider internal friction proves to be an effective approach to reducing mechanical drift. This study holds substantial theoretical and practical significance as it deepens understanding of the mechanisms of mechanical drift in LUMs and offers a pathway to achieve effective mechanical drift control.
MoreTranslated text
Key words
linear ultrasonic motor,creep theory,mechanical drift,self-locking
AI Read Science
Must-Reading Tree
Example
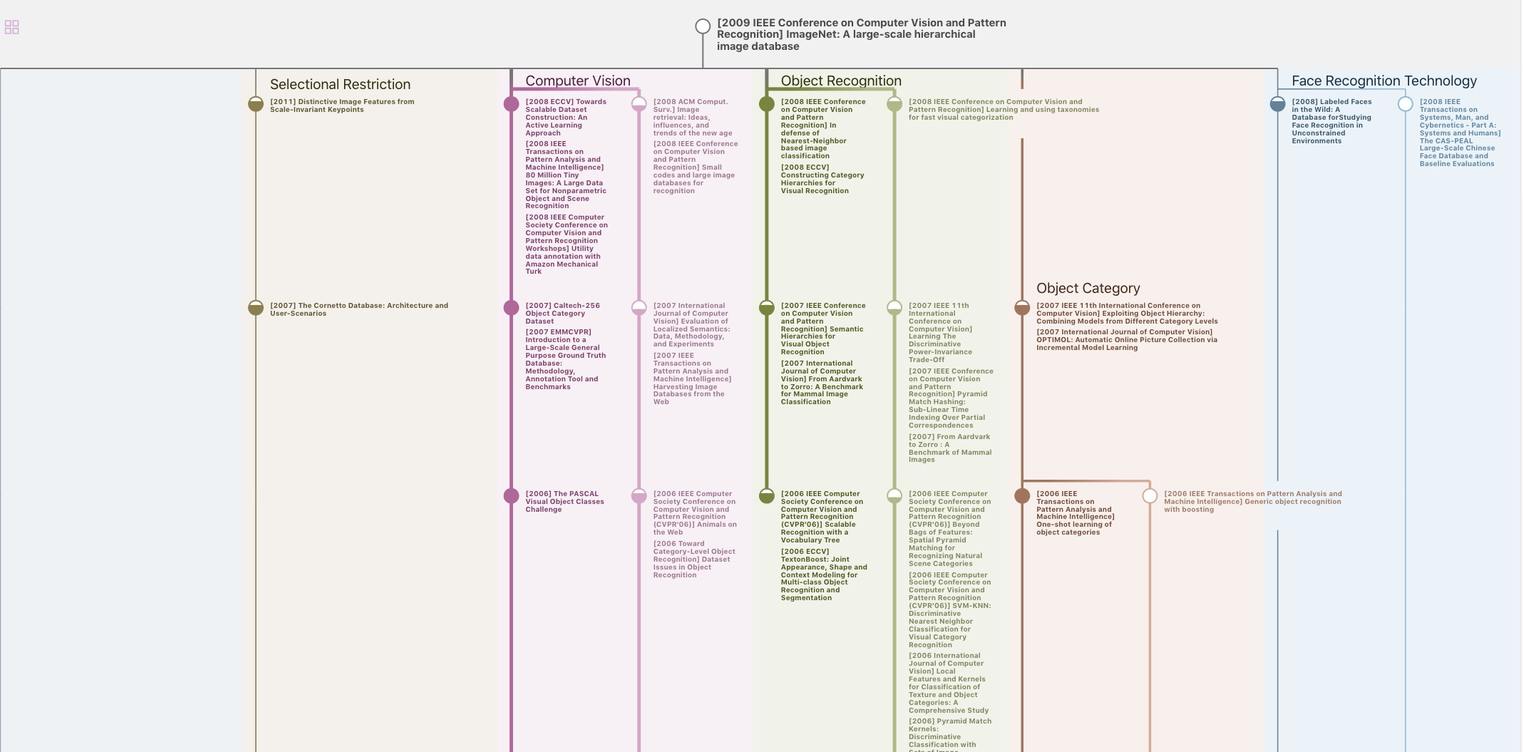
Generate MRT to find the research sequence of this paper
Chat Paper
Summary is being generated by the instructions you defined