Analysis of process parameters on energy utilization and environmental impact of hydrogen metallurgy
Journal of Cleaner Production(2022)
摘要
Based on the heat energy and mass balance, the gas demand and carbon emission of per ton of direct reduced iron were calculated using a hydrogen-metallurgy process with an H-2 and CO mixture as the reducing gas in the reduction temperature range of 800-1300 degrees C. The effects of the reduction temperature and H-2 volume fraction on the gas demand and carbon were analyzed. The direct reduction process was evaluated based on the recovery rate of the reducing gas, gas energy efficiency, and heat recovery rate. The of the study results indicated that when the temperature does not exceed 900 degrees C, the minimum gas demand and lowest recovery rate of the reducing gas increase with an increase in the H-2 volume fraction. When the temperature increases, the minimum gas demand and the lowest recovery rate of the reducing gas first decreased and then increased. When the reduction temperature was 1000.C and the H-2 volume fraction was 22%, the energy consumption reached its lowest value of 3.00 GJ/t. Increasing the H-2 volume fraction or increasing the temperature of the hydrogen metallurgy process can effectively reduce the carbon emissions. In the all-hydrogen state, the higher the temperature, the lower the energy efficiency of the reducing gas. The thermal energy recovery rate decreased with an increasing H-2 volume fraction and reduction temperature. The selection and design of the physical parameters of hydrogen metallurgy to achieve different goals would be more convenient if these calculations are used during the actual operation.
更多查看译文
关键词
Reducing gas demand,Direct reduced iron energy consumption,Direct reduced iron carbon emissions,Recovery rate of reducing gas,Reducing gas energy efficiency,Heat recovery rate
AI 理解论文
溯源树
样例
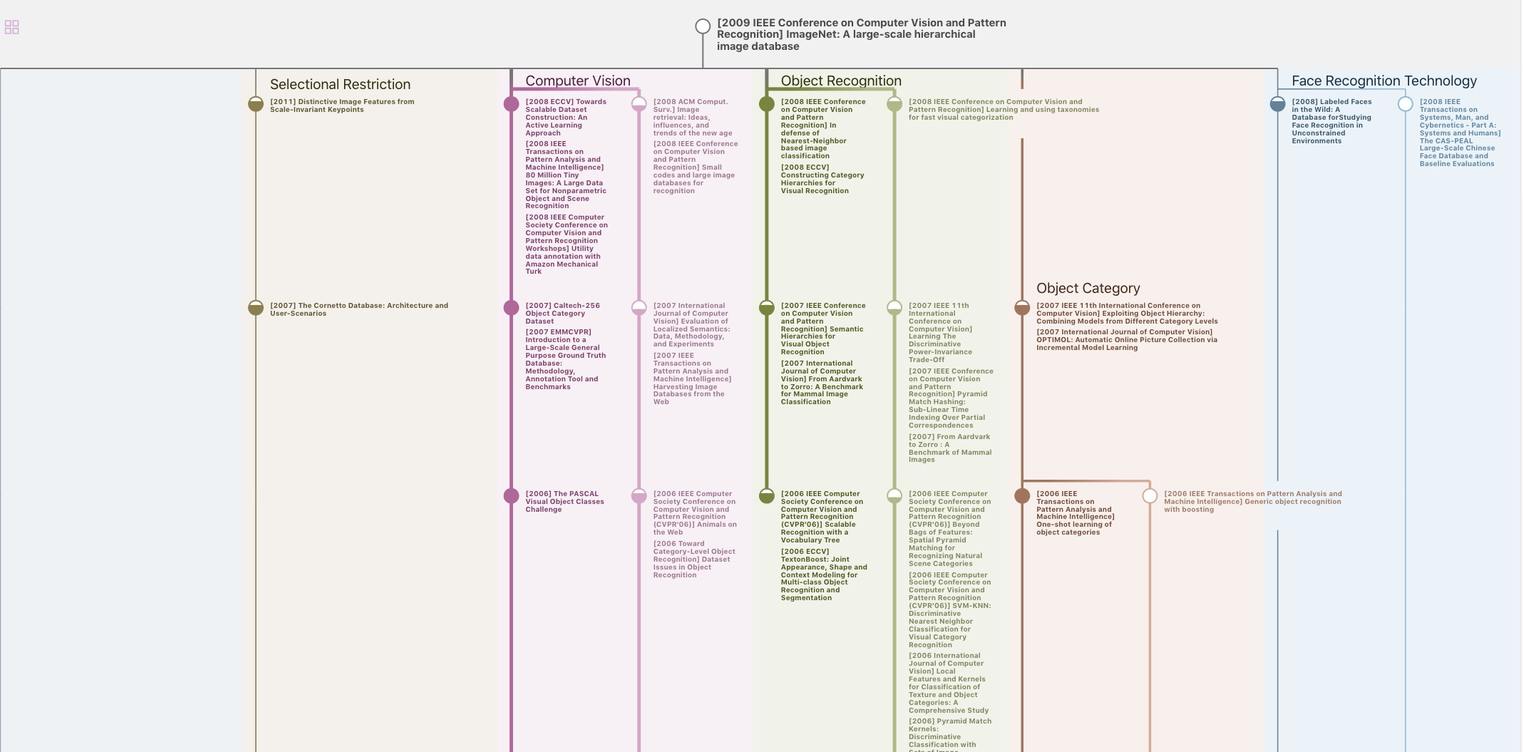
生成溯源树,研究论文发展脉络
Chat Paper
正在生成论文摘要