Visualization and Measurement of Boiling Flow Behaviors in Parallel Mini-channel Heat Exchanger by Neutron Radiography
Materials research proceedings(2020)
摘要
Boiling two-phase flows in cross-flow type mini-channel evaporator were visualized by neutron radiography. Refrigerant vertically upward flow of HFC134a [CH2FCF3] in 21 parallel channels with the hydraulic diameter of 1.47 mm was heated by the heating medium of fluorocarbon FC3283. Void fraction distributions of evaporating two-phase flows were measured by neutron radiography. The effect of the inlet orifices for each refrigerant channel to prevent flow instability was evaluated. The refrigerant was supplied to the test section as subcooled liquid with the mass flux of 50 to 100 kg/(ms). The heating medium was supplied with the mass flux of 460 and 920 kg/(ms) and at the inlet temperature of 47.1 to 67.2 °C. As the result, it is shown that void fraction close to the inlet of heating medium was relatively higher. Flow instability of boiling flows and the effect of the inlet orifices were not observed. Introduction Compactness and decrease in temperature difference between two fluids are still important issues in developing heat exchangers. Especially, decrease in the temperature difference is required for the improvement in performance of energy systems, such as waste heat recovery, refrigerating and air-conditioning systems. One approach is the increase in heat transfer area density. On the other hand, for refrigeration and air-conditioning machines, reduction of the refrigerant charging amount is strongly required to satisfy the Kigali agreement of Montreal Protocol, because popular refrigerants have high global warming potential (GWP). The reduction in the channel diameter is effective way for the both requirements. Microchannel compact heat exchanger manufactured by diffusion bonding process is developed. Smaller refrigerant channel diameter leads to larger pressure loss of refrigerant flows. Larger pressure loss requires larger pumping power. For an evaporator and condenser, the larger pressure loss causes temperature decrease, because the refrigerant is under the saturation condition. Therefore, microchannel heat exchanger has many parallel channels, and refrigerant flow is distributed into the parallel channels to decrease the mass flow rate through each channel. For a liquid or gas single-phase flow application, uniform flow distribution among channels is Neutron Radiography WCNR-11 Materials Research Forum LLC Materials Research Proceedings 15 (2020) 274-280 https://doi.org/10.21741/9781644900574-43 275 easily obtained by appropriate design of the header for flow distribution. However, in the case where the refrigerant flows with evaporation or condensation, maldistribution often occurs, regardless of the inlet flow condition. The maldistribution causes deterioration in the heat transfer performance. Such parallel microchannel systems are investigated for the application of the cooling device of electro equipment. Huang and Thome [1] conducted boiling flow experiments in 67 parallel microchannel cooling equipment using three types of refrigerant. The channel hydraulic diameter was 0.1 mm. As a result; it was shown that boiling flows could be stabilized by an inlet orifice for each channel, and pressure loss through the straight section except of the inlet orifice decreased. Dário, et al. [2] experimentally evaluated the pressure drop of HFC-134a boiling flows through 9 parallel microchannels with the hydraulic diameter of 0.77 mm. Frictional and acceleration contributions to the pressure drop were analyzed. In these studies, parallel channels were symmetrically heated with constant heat flux. Kuroki, et al. [3] conducted HFC-32 boiling flow experiments in 2 parallel channels with the diameter of 1.0 mm. The effect of nonuniformly heating on heat transfer coefficient was evaluated. It was reported that under the nonuniformly heating condition, the heat transfer coefficient of the flow with higher heating load became lower, and overall heat transfer coefficient of the parallel channels decreased by nonuniform heating. The deterioration in heat transfer coefficient might be caused by refrigerant maldistribution. In this study, boiling two-phase flows in cross-flow type mini-channel evaporator manufactured by diffusion bonding were visualized by neutron radiography. Liquid refrigerant was heated by a heating medium. The effects of mass flow rate of the refrigerant, mass flow rate and inlet temperature of the heating medium on heat transfer rate and void fraction distribution were evaluated. Experimental setup and method A schematic diagram of experimental apparatus is shown in Fig. 1. HFC-134a, whose chemical formula is CH2FCF3, was used as the refrigerant, and fluorocarbon FC-3283 was used as the heating medium. The attenuation of neutron is quite low for FC3283 because FC3283 does not include hydrogen. Subcooled liquid refrigerant was supplied to the test section through a preheater by a gear pump. The refrigerant inlet temperature was measured by a K-type sheathed thermocouple inserted in the channel at the downstream of a mixing section. A tank was connected to the upstream of the pump to absorb volume change due to boiling. Refrigerant pressures were measured at the inlet and outlet of the test section. On the other hand, the heating medium was supplied from a temperature controlled bath. Inlet and outlet temperatures were measured by inserted thermocouples. Mass flow rates of both fluids were measured by mass flow meter. A schematic of tested heat exchanger is shown in Fig. 2. Refrigerant and heating medium channels were formed on a thin stainless steel sheet by chemical etching process, individually. Then, the sheets was stacked by diffusion bonding process. The cross-sectional shape of channels was semi-circular with the hydraulic diameter of 1.47 mm as shown in Fig. 2 (b). The same channel shape was applied to both fluids. The number of channels was 21 for the refrigerant and 20 for the heating medium. The channels were set in crossflow arrangement as shown in Fig. 2(a). The temperature of the heating medium would be higher at the right channel near the heating medium inlet. The test section was placed vertically to form upward boiling flows. Two types of refrigerant channel were used, namely, Type I with an inlet orifice for each channel and Type II without inlet orifice. Neutron radiography experiments were carried out at B4 port of Kyoto University Research Reactor. The neutron beam was irradiated from the front face. The exposure time was set to 30 Neutron Radiography WCNR-11 Materials Research Forum LLC Materials Research Proceedings 15 (2020) 274-280 https://doi.org/10.21741/9781644900574-43 276 seconds. Since the width of the radiation field was narrower than that of the heat transfer area, radiograph was obtained for 5 sections by moving horizontally. Figure 3 shows an original visualized image of the center section. The pixel size was 87.9 μm/pixel. Void fractions, α, were measured from three radiographs of two-phase flows, the liquid single-phase flow and the vapor single-phase flow. Assuming that the brightness of a visualized image is proportional to the beam intensity on a scintillation converter and neglecting the attenuation term due to a gas phase, the brightness of two-phase flow image STP(x,y), the image of liquid single-phase flow S0(x,y), i.e., α(x,y)=0, and the image of vapor single-phase flow S1(x,y), i.e., α(x,y)=1, are expressed as the following equations [4]. ( ) ( ) ( ) ( ) { } ( ) [ ] ( ) y x O y x t y x y x t y x G y x S TP c mL L w mw w TP , , , 1 , exp , , + − − − = m ρ α m ρ (1) ( ) ( ) ( ) ( ) [ ] ( ) y x O y x t y x t y x G y x S c mL L w mw w , , , exp , , 0 0 + − − = m ρ m ρ (2) ( ) ( ) ( ) [ ] ( ) y x O y x t y x G y x S w mw w , , exp , , 1 1 + − = m ρ (3) where ρ and mm are the density and mass attenuation coefficient, respectively. tw and tc is thickness of wall and channel along a neutron beam, respectively. G(x, y) is the gain and depends on the position due to a non-flatness of the initial beam intensity and of the sensitivity in a imaging system. OTP(x, y), O0(x, y), O1(x, y) are the offset value in brightness. In this study, the dark current O(x, y) was used as the offset values. Using equations (1) to (3), a two-dimensional void fraction distribution can be expressed as ( ) ( ) ( ) ( ) ( ) ( ) ( ) [ ] ( ) ( ) ( ) ( ) ( ) ( ) [ ] y x O y x S y x O y x S y x O y x S y x O y x S y x TP , , , , ln , , , , ln ,
更多查看译文
AI 理解论文
溯源树
样例
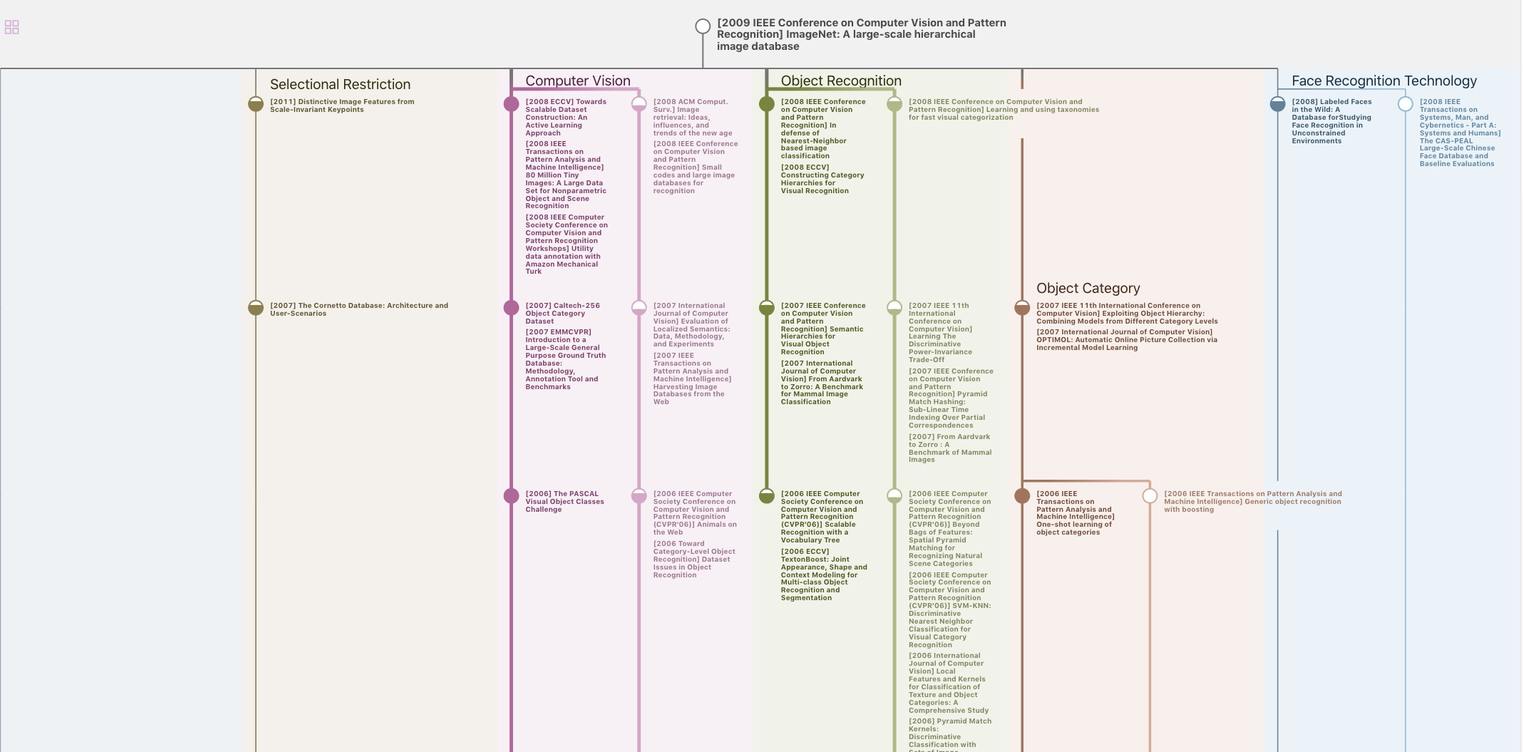
生成溯源树,研究论文发展脉络
Chat Paper
正在生成论文摘要