Model Guided Mixing Of Ceramic Powders With Graded Particle Sizes In Binder Jetting Additive Manufacturing
PROCEEDINGS OF THE ASME 13TH INTERNATIONAL MANUFACTURING SCIENCE AND ENGINEERING CONFERENCE, 2018, VOL 1(2018)
Abstract
Binder jetting additive manufacturing is a promising technology for fabricating ceramic parts with complex or customized geometries. However, this process is limited by the relatively low density of the fabricated parts even after sintering. This paper reports a study on effects of mixing powders with graded particle sizes on the powder bed packing density and consequently the sintered density. For the first time, a linear packing model, which can predict the packing density of mixed powders, has been used to guide the selection of particle sizes and fractions of constituent powders. A selection process was constructed to obtain the maximum mixed packing density. In the part of model validation, three types of alumina powders with average sizes of 2 gm, 10 gm, and 70 gm, respectively, were mixed in optimum volumetric fractions that could lead to the maximum packing density based on model predictions. Powder bed packing density was measured on binary mixtures, ternary mixture, and each constituent powders. Furthermore, disk-shaped samples were made, using binder jetting additive manufacturing, from each constituent and mixed powder. Results show that binary and ternary mixtures have higher powder bed packing densities and sintered densities than the corresponding constituent powders. The disks made from the ternary mixture achieved the highest sintered density of 65.5%.
MoreTranslated text
Key words
binder jetting additive manufacturing,ceramic powders,graded particle sizes
AI Read Science
Must-Reading Tree
Example
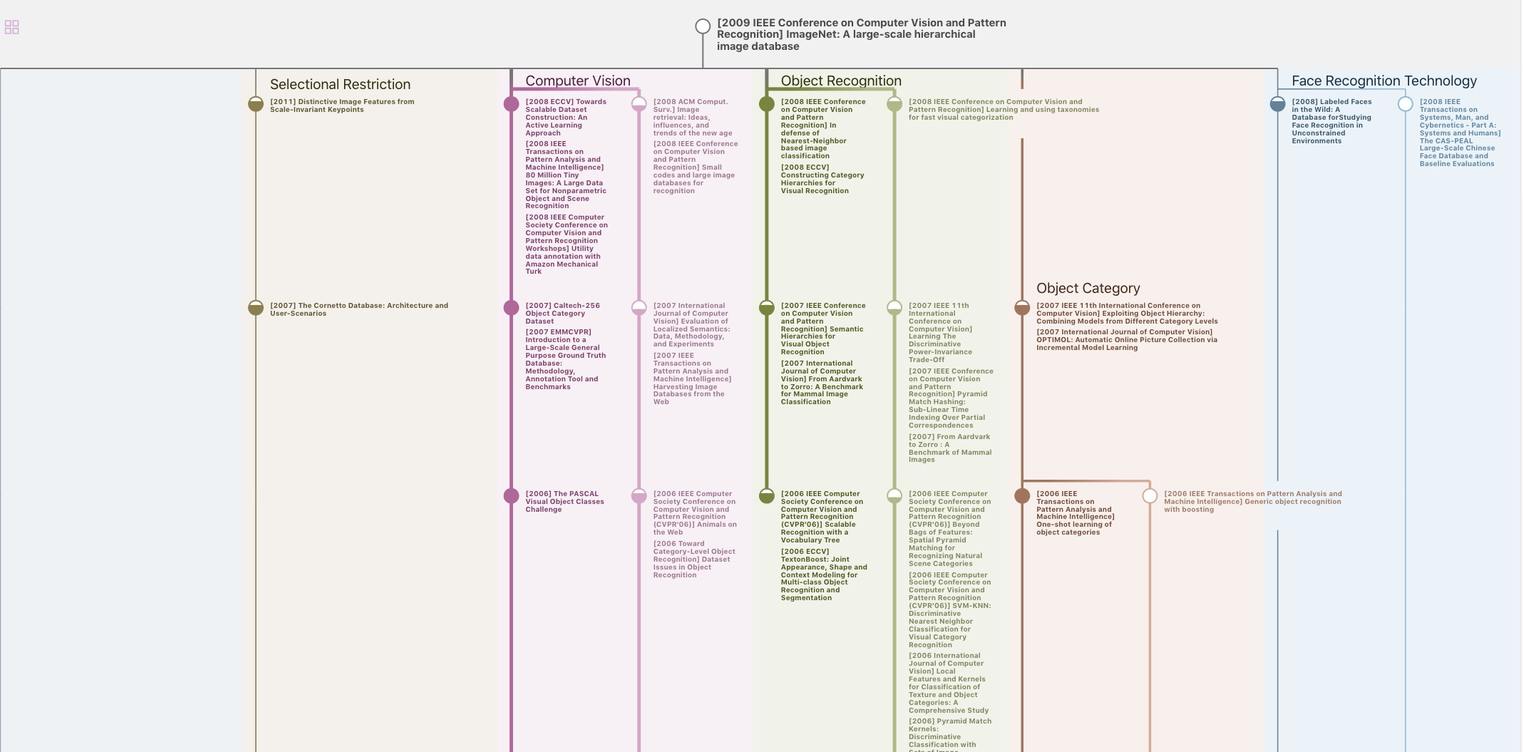
Generate MRT to find the research sequence of this paper
Chat Paper
Summary is being generated by the instructions you defined