Three-dimensional finite element method for the filling simulation of injection molding
Engineering with Computers(2006)
Abstract
With the development of molding techniques, molded parts have more complex and larger geometry with nonuniform thickness. In this case, the velocity and the variation of parameters in the gapwise direction are considerable and cannot be neglected. A three-dimensional (3D) simulation model can predict the filling process more accurately than a 2.5D model based on the Hele–Shaw approximation. This paper gives a mathematical model and numeric method based on 3D model to perform more accurate simulations of a fully flow. The model employs an equal-order velocity–pressure interpolation method. The relation between velocity and pressure is obtained from the discretized momentum equations in order to derive the pressure equation. A 3D control volume scheme is used to track the flow front. During calculating the temperature field, the influence of convection items in three directions is considered. The software based on this 3D model can calculate the pressure field, velocity field and temperature field in filling process. The validity of the model has been tested through the analysis of the flow in cavities.
MoreTranslated text
Key words
3D,Equal-order interpolation,Injection molding,Simulation
AI Read Science
Must-Reading Tree
Example
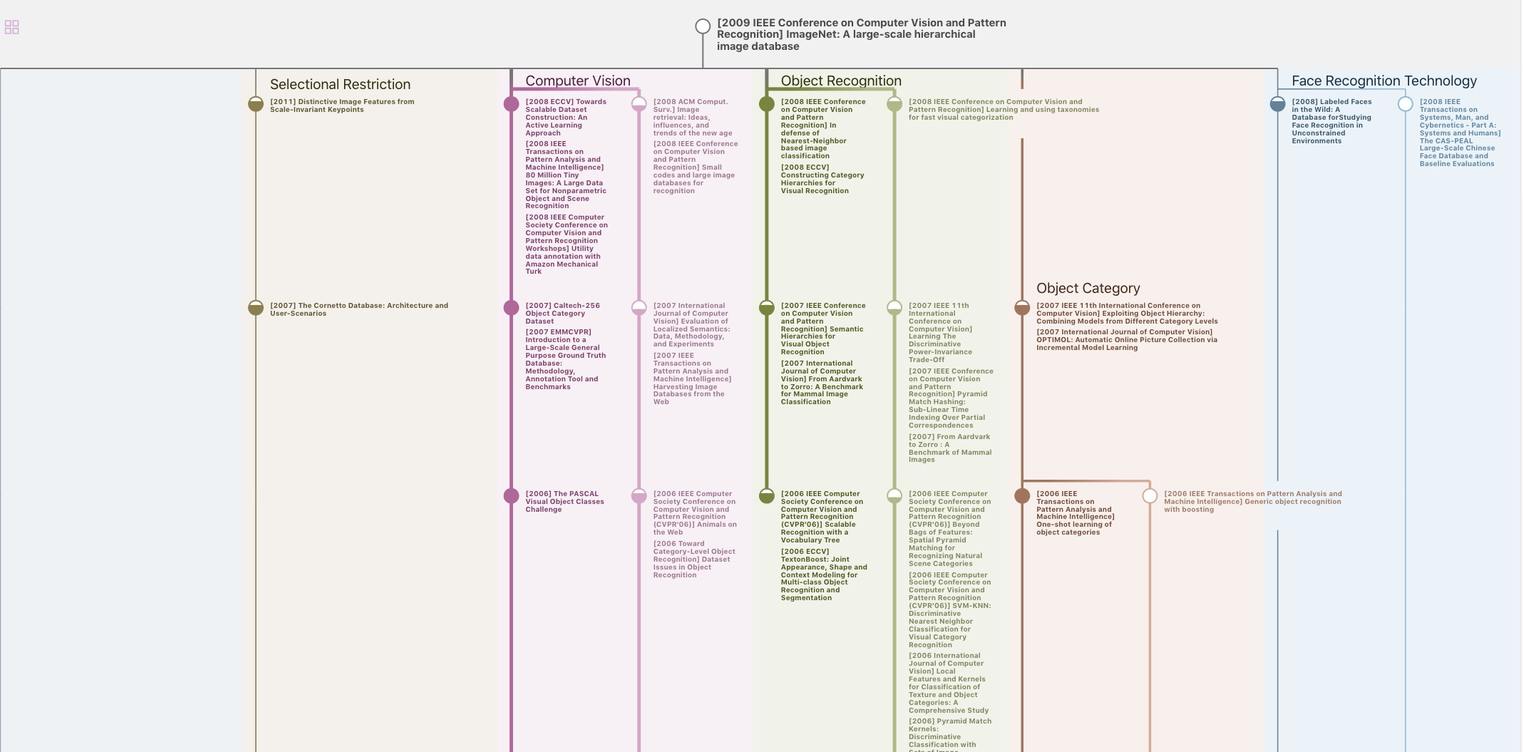
Generate MRT to find the research sequence of this paper
Chat Paper
Summary is being generated by the instructions you defined