Finish dry turning of DC53 tool steel via modified carbide inserts: a study of machining dynamics
The International Journal of Advanced Manufacturing Technology(2024)
摘要
DC53 steel possesses a unique balance of toughness and hardness and has extensive applications in punches and ejector pins where the turning process is the primary shaping technique. Data concerning the conventional machining of DC53 steel is limited. Some researchers have tried the wire electric discharge machining (EDM) process to thoroughly explore its machinability aspects. According to a detailed literature review, Xcel carbide tool geometry outperformed both conventional and wiper tooling in dry turning of tool steels. Therefore, the Xcel tool configuration is evaluated in the present work for dry turning of DC53 steel at higher feed rates. The effect of operating parameters, including cutting speed (50, 100 m/min), feed rate (0.225, 0.337, and 0.562 mm/rev), and depth of cut (0.5, 1 mm), are evaluated. The tribology of tool wear is supplemented with optical, scanning electron microscope (SEM) images, and energy dispersive X-ray (EDX) analysis. Machining dynamics data involving tool life, total material removed, surface roughness, machining zone temperature, power consumption, and workpiece surface hardening is presented. In general, experiments conducted at 100 m/min cutting speed produced better results in terms of all evaluated responses. A maximum tool life of 39 min was observed at 100 m/min cutting speed, 0.225 mm/rev feed rate, and 1 mm depth of cut with the minimum surface roughness value of 0.20 µm-Ra, while maximum material (1410 cm3) was removed at 100 m/min, 0.562 mm/rev, and 1 mm in just 25 min with acceptable surface roughness (Ra < 1 µm). However, the latter conditions consumed 58
更多查看译文
关键词
DC53 steel,Finish dry turning,Xcel carbide inserts,Tool life,Machining dynamics
AI 理解论文
溯源树
样例
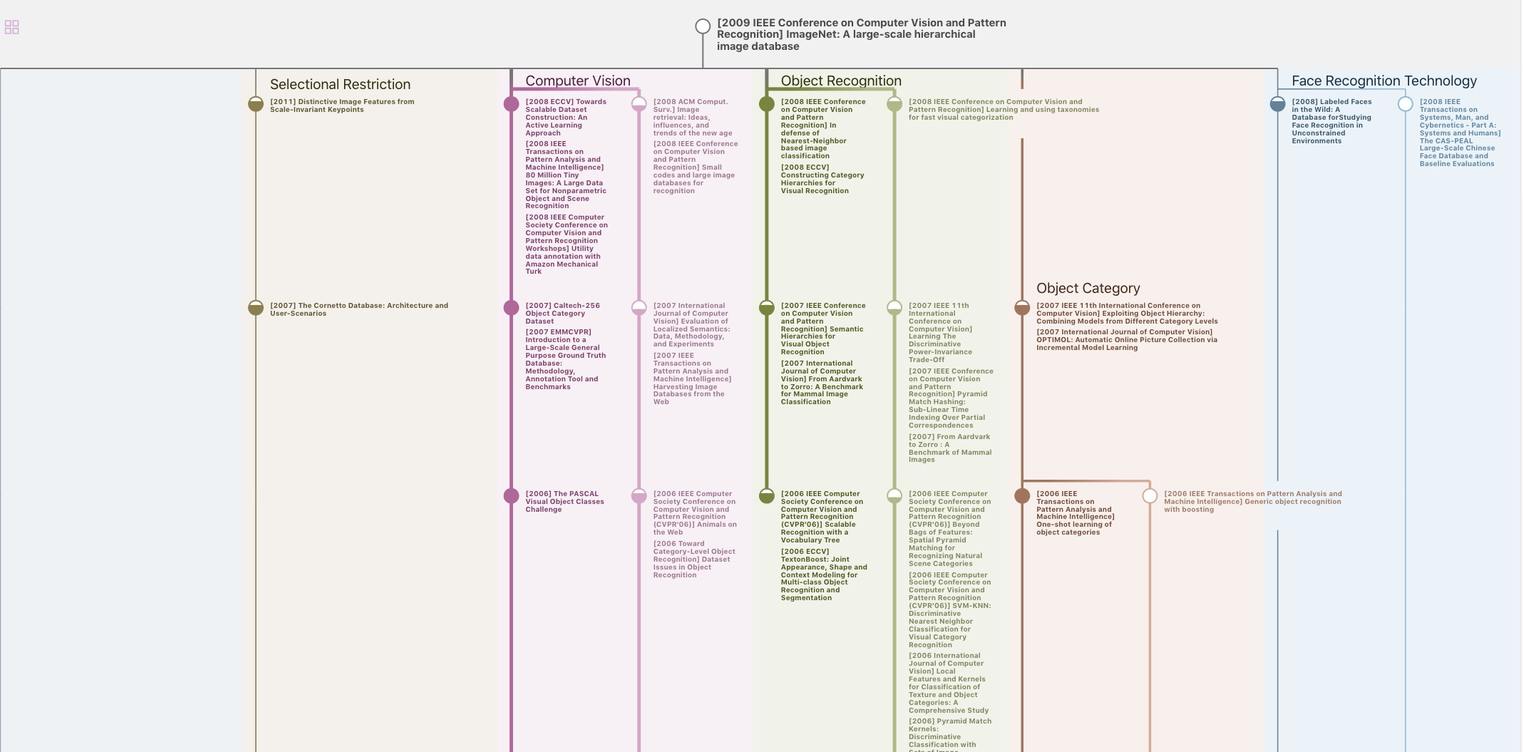
生成溯源树,研究论文发展脉络
Chat Paper
正在生成论文摘要