FEA and experimental ultimate burst pressure analysis of type IV composite pressure vessels manufactured by robot-assisted radial braiding technique
INTERNATIONAL JOURNAL OF HYDROGEN ENERGY(2024)
摘要
Composite pressure vessels (CPVs) are lightweight and high-strength containers that can be used for the storage of compressed gases, including hydrogen. While hydrogen is a promising alternative energy source, storage of hydrogen comes with its significant challenges which requires a need for the efficient production of CPVs. Most commonly, CPVs are manufactured using filament winding technology. Due to the rise in the need for pressure vessels, there is a need for alternative high-throughput manufacturing techniques. Braided, in comparison to filament winding, has a high throughput and is less research manufacturing technology for CPVs. In this study, the applicability of braiding for the manufacturing of CPV is researched. Two types of 2D braids, namely the conventional and unidirectional, braiding were studied for their application in such structures, 24K and UD tanks, respectively. Dry carbon fiber (T700S -24K) and HDPE liner were used to manufacture two different types of composite pressure vessels (CPVs), by robot-assisted radial braiding technique. After the preform of the braiding process was finished, CPVs were cured with a vacuum infusion process (VIP) by using a mold system. Produced braided CPVs were subjected to a hydrostatic burst test in order to determine their ultimate burst pressure point. Finite element analysis (FEA) was used to optimize and correlate experimental burst pressure test results. Ansys ACP was utilized to design composite structures by dividing both tanks' domes into sub-sections. Results suggest that the experimental burst pressure test of 24K and UD tanks were identified as 200 bar and 150 bar, respectively. UD vessel ruptured close to the dome, whereas the 24K fracture point was located in the center of the dome. UD braided CPV was shown to have a smaller apparent burst deformation (rupture) scale than 24K CPV. In comparison to 24K, the UD braided CPV is 5.7% lighter and requires 20.9% less carbon fiber in production. FEA results were consistent with experimental results in terms of the burst pressure point. For both 24K and UD, the fiber failure starts at the point where the cylinder section and boss system are connected under pressure, and fiber failures continue to progress steadily as the pressure increases.(c) 2023 Hydrogen Energy Publications LLC. Published by Elsevier Ltd. All rights reserved.
更多查看译文
关键词
Carbon fiber,Braiding,Composite pressure vessel,Burst test,FEA
AI 理解论文
溯源树
样例
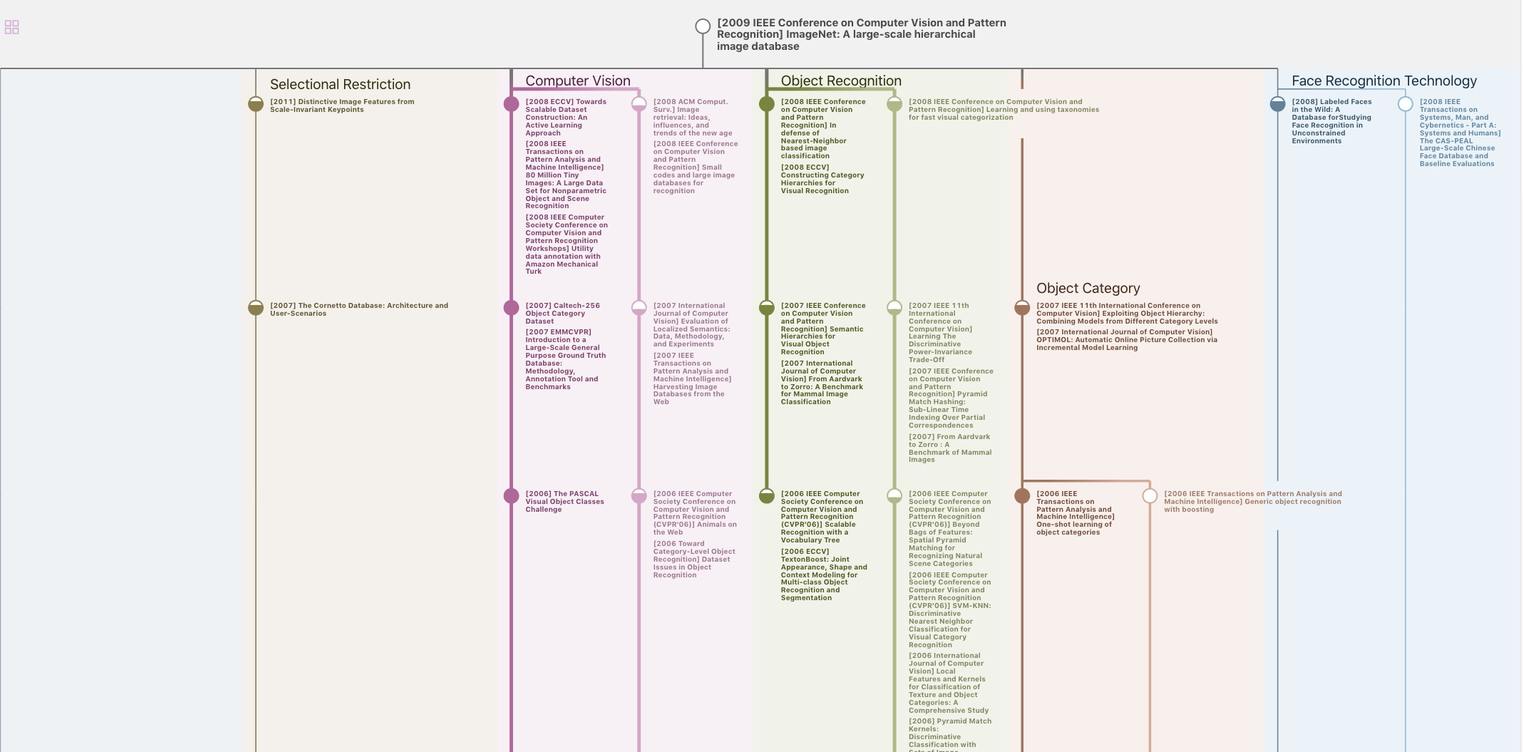
生成溯源树,研究论文发展脉络
Chat Paper
正在生成论文摘要