Finite Element Simulation of Wear Behavior of Groove-textured Rocket Sled Slider
CHINA SURFACE ENGINEERING(2023)
摘要
A rocket sled system is a piece of dynamic test equipment driven by a rocket engine on a dedicated track at high forward speeds, for the purposes of collecting test data. Wear is a direct consequence of using the rocket sled system that is serviced under certain working conditions. It has been confirmed that the wear of the slider of the rocket sled system under high-speed and heavy-load conditions seriously threatens the reliable operation and service safety of the rocket sled during operation. The wear damage of rocket sled slider wear is inevitable, and has been considered as a technical bottleneck that restricts the development and application of the rocket sled system. The aforementioned issue has not been addressed owing to the extreme service condition and high test cost, with current research often limited to simulations of only two-dimensional models, or local impact deformation analysis. Existing studies have revealed that surface texture can weaken the wear damage of materials to a certain extent. The finite element simulation analysis method has become an effective way to analyze the friction and wear behavior of materials, so that the wear of the slider can be reasonably predicted and evaluated. In the present work, a finite element three-dimensional wear model consisting of a 0Cr18Ni9Ti stainless steel slider and a U71Mn steel rail for railway track was established. First of all, in order to accurately and effectively simulate the wear process of a rocket sled slider, the widely recognized and mature Archard theory and finite element discretization were used as the wear calculation principle and numerical calculation method, respectively. Additionally, to avoid forming mesh distortions caused by repositioning the surface mesh nodes during the wear process of the rocket sled slider, a nonlinear adaptive geometric update strategy was adopted to redivide the mesh when mesh distortion occurred. Furthermore, the elastoplastic deformation of the rocket sled slider was also taken into account; a bilinear isotropic hardening constitutive model of the slider material was provided. Meanwhile, one kind grooved surface texture was designed, with the grooves parallel to the sliding direction. In the simulation, the width and depth of the grooved surface texture was 50 equal parts and 100 equal parts of the symmetrical model width (13.5 mm) - namely 270 mu m and 135 mu m, respectively - while the texture density was varied between values of 22%, 28%, and 34%. The wear simulation of the smooth surface and the groove-textured surface of the rocket sled slider were carried out. Finally, any changes to contact characteristics during the wear process of the slider such as contact surface wear, von Mises stress, and contact pressure were revealed. The results showed that the smooth surface which presented a significant front-end effect, might lead to the occurrence of eccentric wear. On the other hand, the grooved surface texture have resulted in a uniform stress distribution and stable gradient pressure, and would significantly reduce the wear of slider. The increase in texture density was found to promote uniform wear at the friction interface. In addition, positive variations in uniform stress distribution and stable gradient change were also demonstrated as the texture density increased on groove-textured rocket sled slider, which alleviated the stress concentration and has avoided severe wear of the slider during long time service. Meanwhile, the contact pressure also increased with the increase of texture density, which brought the contact surface in closer contact with the target surface, with the gap between the two appearing smaller. This is able to effectively avoid three-body wear that is induced by formed abrasive particles or debris from wear. Therefore, only the factor of texture density is deserved to be considered, with the 34% texture density the most appropriate value. The finite element simulation suggested that the grooved surface texture was able to reduce wear, which can provide technical reference and theoretical support for the realization of a rocket sled slider with anti-friction properties, anti-wear properties, and structural designability.
更多查看译文
关键词
rocket sled slider,finite element simulation,wear,grooved surface texture
AI 理解论文
溯源树
样例
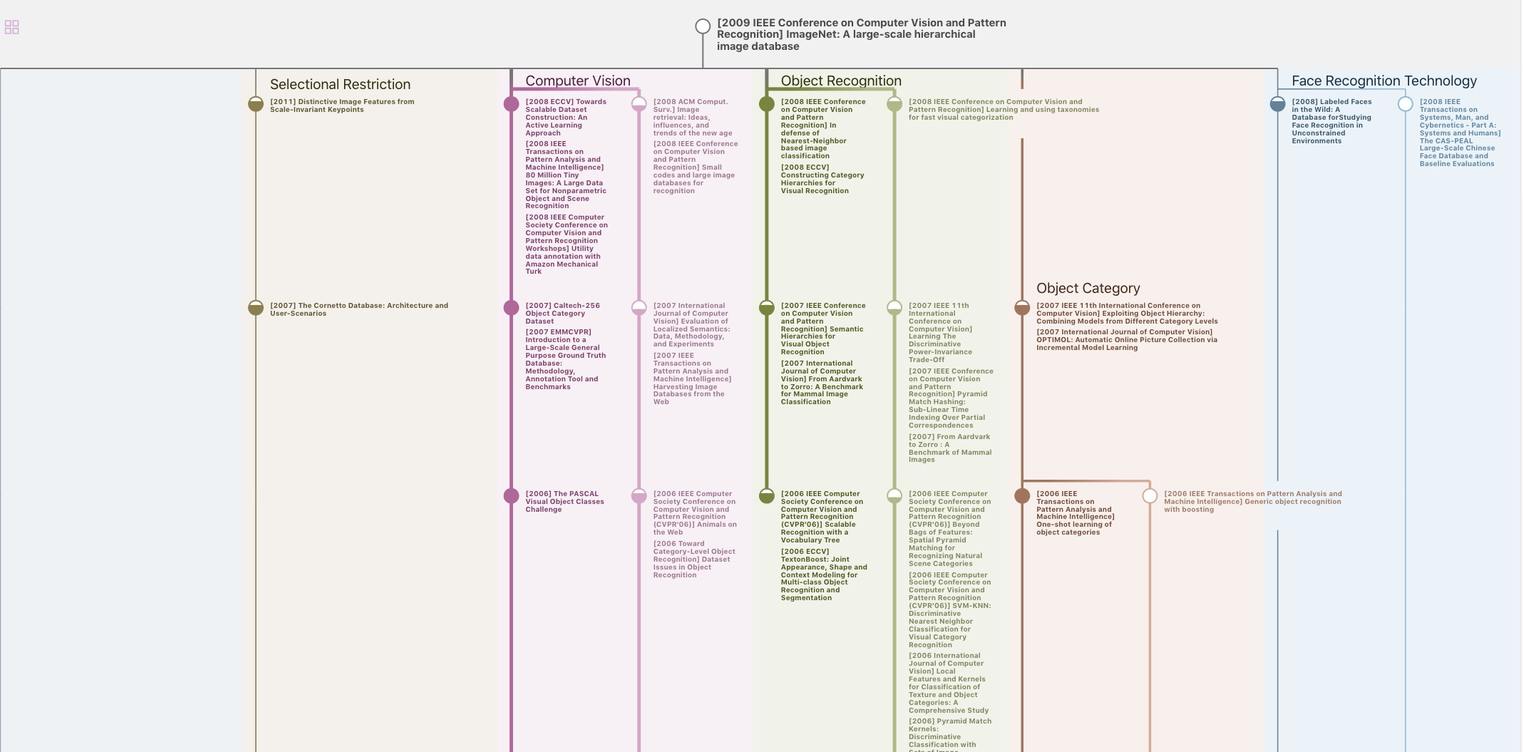
生成溯源树,研究论文发展脉络
Chat Paper
正在生成论文摘要