Experimental investigation of electrochemical cut-off grinding for Inconel-718 and comparative study with Ti-6Al-4V alloy
ADVANCES IN MATERIALS AND PROCESSING TECHNOLOGIES(2023)
摘要
In the present study, a hybrid machining process known as an electrochemical cut-off grinding (ECCG) is used for grinding of Inconel-718 material. The specimen (superalloy) contains nickel as major component. It cannot be machined conventionally due to its outstanding properties. During the electrochemical grinding of Inconel 718, the author examines the effects of input voltage (v), tool feed rate (mm/min), electrolytic concentrations (g/ltr), electrolytic flow rate (ltr/min), and grinding speed (rpm) on responses such as material removal rate (MRR) and surface roughness (Ra). The tests contains the bronze-bonded diamond abrasive grinding wheel. The MRR and surface roughness of Inconel 718 and titanium super alloy during the ECCG process are also compared in this research project. Based on the findings of the studies, it appears that the tool feed rate, the flow rate of the electrolyte, and the rotation of the grinding wheel are the maximum influential parameters for enhancing MRR and surface finish during electrochemical cut-off grinding of Inconel 718. Tool feed rates of 0.09 mm/min to 0.18 mm/min, electrolyte flow rates of 5 ltr/min to 8 ltr/min, and grinding wheel speeds of 800 rpm to 2000 rpm are the ideal influencing factors. The comparative analysis demonstrates that Ti-6Al-4 V alloy cannot match Inconel 718's machinability. Compared to Ti-6Al-4 V alloy, Inconel-718 has an average material removal rate that is up to 1.73 times higher and an average surface quality that is up to 3.16 times better.
更多查看译文
关键词
Electrochemical cut off grinding method, Inconel 718, Ti-6Al-4V alloy, material removal rate, surface roughness, electrochemical machinability
AI 理解论文
溯源树
样例
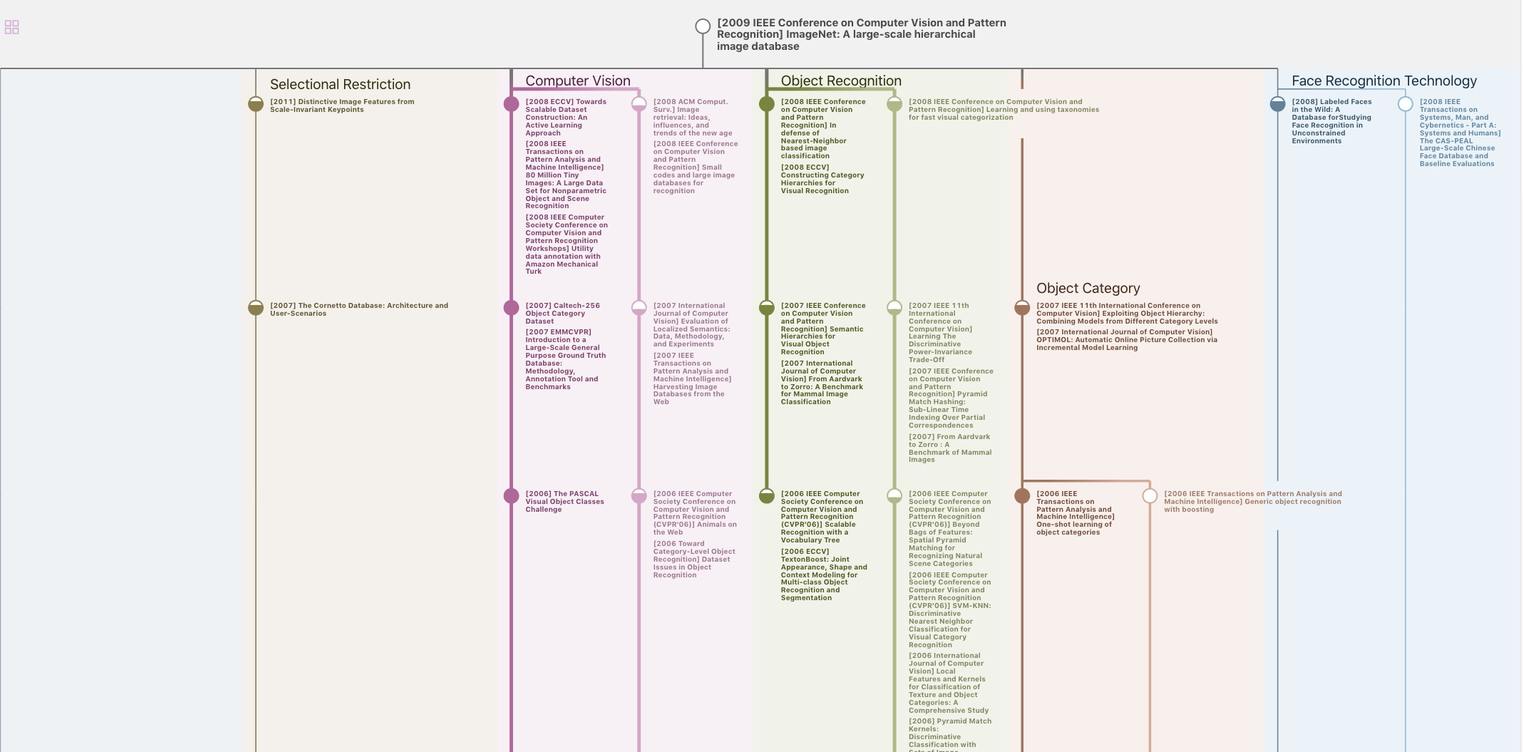
生成溯源树,研究论文发展脉络
Chat Paper
正在生成论文摘要