Virtual special issue: Fatigue 2021: The properties, processing, and performance of structural materials
FATIGUE & FRACTURE OF ENGINEERING MATERIALS & STRUCTURES(2023)
摘要
The Engineering Integrity Society (EIS) has been a valuable forum for practicing engineers and scientists from the international fatigue and durability community since its foundation in 1985. Fatigue 2021 was the eighth in a series of major conferences organized by the EIS, and the Society's first online, on-demand event. The principal theme of the Fatigue 2021 conference was to explore and discuss the challenges of using high-performance materials for reliable and cost-effective products. Over 120 participants presented work examining the complex interplay between materials and their processing, advanced manufacturing methods, and the subsequent durability and reliability of the machines and devices. Twelve high-quality papers were selected for the Fatigue and Fracture of Engineering Materials and Structures (FFEMS) special issue to highlight some of the important advances and key developments in fatigue and durability research presented at the conference. Since their inception, conferences hosted by the EIS have attracted contributions from leading academic researchers seeking to advance the fundamental science behind fatigue damage accumulation, crack initiation, crack growth, and ultimate failure mechanisms. In turn, the EIS has encouraged the development of fatigue models for the prediction of behavior in established and novel materials, engineering components, and full-scale structures. Indeed, the development of fatigue lifing algorithms as a basis for industrial application was a particular interest of our founding President, Dr. Peter Watson.1 Therefore, it is fitting that papers in this special issue continue to reflect the crossover between academia and industry. Incremental fatigue damage leading to crack growth and failure in a NiTi shape memory alloy is the basis for a sophisticated finite element analysis framework proposed by Simoes et al.2 When describing constitutive behavior in this class of material, it is necessary to address the added complication of temperature-sensitive phase transformations. Validation relies on a comprehensive raft of previously published empirical studies. The simulations address an increasing level of complexity: (i) the strain-life response of plain laboratory specimens, (ii) the growth of fatigue cracks in single edge notched specimens, (iii) the prediction of fatigue crack growth rates to quantify Paris law parameters, and finally (iv) the fatigue failure of a 3D diamond lattice structure. It is interesting to note that computational efficiencies and associated cost are considered as important by the authors. Three complementary papers by Vasco-Olmo et al and Camacho-Reyes et al,3-5 focusing upon crack propagation mechanisms, employed more established titanium, stainless steel, and aluminum alloys as the vehicle for detailed empirical research. Evaluation of surface crack growth, crack wake, and crack tip plasticity in compact tension specimens relied on optical microscopy and digital image correlation (DIC) to establish local strain fields and crack tip opening displacement. A novel application of DIC even allowed for the measurement of the 3D out-of-plane strains within the crack tip plastic zone. This combined research portfolio allows for an improved understanding of the effects of the crack tip plasticity on the mechanism of crack advance and corrections to the associated crack driving forces. These three papers exemplify the popularity of DIC techniques for fatigue characterization that has developed during the past two decades. Improved access to X-ray beam line facilities over a similar period offers an alternative to DIC for the characterization of crack paths and associated damage, with the additional advantage of providing full 3D inspection of the interior. Carrera et al6 provide improved definition of the plastic zone geometry associated with a through crack growing in a bainitic steel specimen. It is encouraging to note their empirical measurements fell within the plane stress/plane strain bounds predicted by traditional Westergaard elastic strain theory. Once again, this research will support greater accuracy to the definition of appropriate stress intensity factors. In contrast, Xue et al7 focus their attention on earliest stages of fatigue crack initiation, in particular the phenomenon of multiple subsurface cracking that can be a common feature of fatigue failures in titanium alloys. Planar slip damage leading to cracking in alpha phase grains was invariably detected as the source of cracking; however, differences in crack tip opening morphologies were noted for surface and subsurface cracks. Given recent well-publicized in-service aero-engine failure events,8 it would be interesting to see similar tomography applied to Ti-6Al-4V containing microstructurally textured regions (so called “macrozones”) and to incorporate dwell fatigue loading cycles where practical. A common feature of the two papers that concentrated upon corrosion-fatigue was the sophistication of the laboratory-based systems devised for the replication of in-service damage. In the first example, Fatoba and Akid9 simulated aqueous corrosion pitting of a pipeline steel via advanced electrolysis methods and then applied high magnification optical inspection to study the interaction between neighboring pits during crack initiation and the subsequent transition to a “long” fatigue crack. Mathematical models were applied to describe this key stage of the total corrosion-fatigue life. The experimental setup required to simulate a high-temperature environment employed by Bache et al10 for their in situ assessment of a nickel-based super alloy in highly corrosive sulfur dioxide (SO2) gas did not allow for the partition of the total fatigue lives. However, an understanding of the short cracks developing from corrosion pits was again emphasized, in this case forming at the surface of plain test specimens due to grain dropout and intergranular sulfide attack. Complementary crack propagation measurements on corner crack specimens indicated that SO2 itself was benign during stage II long crack growth, that is, crack rates and fatigue crack threshold were insensitive to the presence of SO2 in high-temperature air. In terms of materials processing, additive technologies continue to attract a wealth of research, as witnessed at Fatigue 2021 with four complete sessions dedicated to powder based alloys. From the fatigue perspective, 3D printed structures offer obvious challenges, including the potential for microstructural defects or microtexture acting as internal crack initiation sites plus inherently complex geometries or surface flaws providing local stress raising features. A fundamental knockdown in fatigue performance for laser powder bed fused 316L stainless steel, when compared to traditional wrought product, is characterized by Liang et al.11 Low cycle fatigue performance was invariably dominated by dislocation based damage and bulk plasticity, ignoring the fusion flaws that were distributed throughout the additive volume. In contrast, under high cycle fatigue conditions, failure was notably sensitive to these fusion defects, with improvements to the surface finish helping to recover fatigue strength to a degree although not entirely back to wrought properties. By way of alleviating such fatigue debits, Martin et al12 investigate the potential for an annealing heat treatment to resist crack initiation through strain recovery, grain growth, and general improvements to ductility in a nickel-based superalloy destined for aerospace application. These combined microstructural modifications were also beneficial for the control of long crack growth rates. Finally, two case studies are published, which adopt various aspects of academic research for the description of fatigue failure in engineering components. Iyer Kumar et al13 document a laboratory study of the fatigue performance of composite-to-steel double-strap adhesive joints employed for marine applications. The fatigue assessment generated a stress–life (S-N) database supported by detailed fractography to define the interaction at the composite–adhesive–metal interfaces. Under this scenario, a “life to first crack” lifing approach could be adopted to support future component design. In contrast, Hectors et al14 take a linear elastic fracture mechanics (LEFM) approach to model the fatigue performance of a welded overhead crane runway girder. Material specific properties including Paris–Erdogan stage II crack growth data were experimentally determined to underpin their finite element model. Load spectra based on real operational data and measurements of hot spot stresses fed the fracture mechanics simulations to successfully predict crack morphology and the fatigue properties of two critical joints of the crane structure.
更多查看译文
关键词
fatigue,materials
AI 理解论文
溯源树
样例
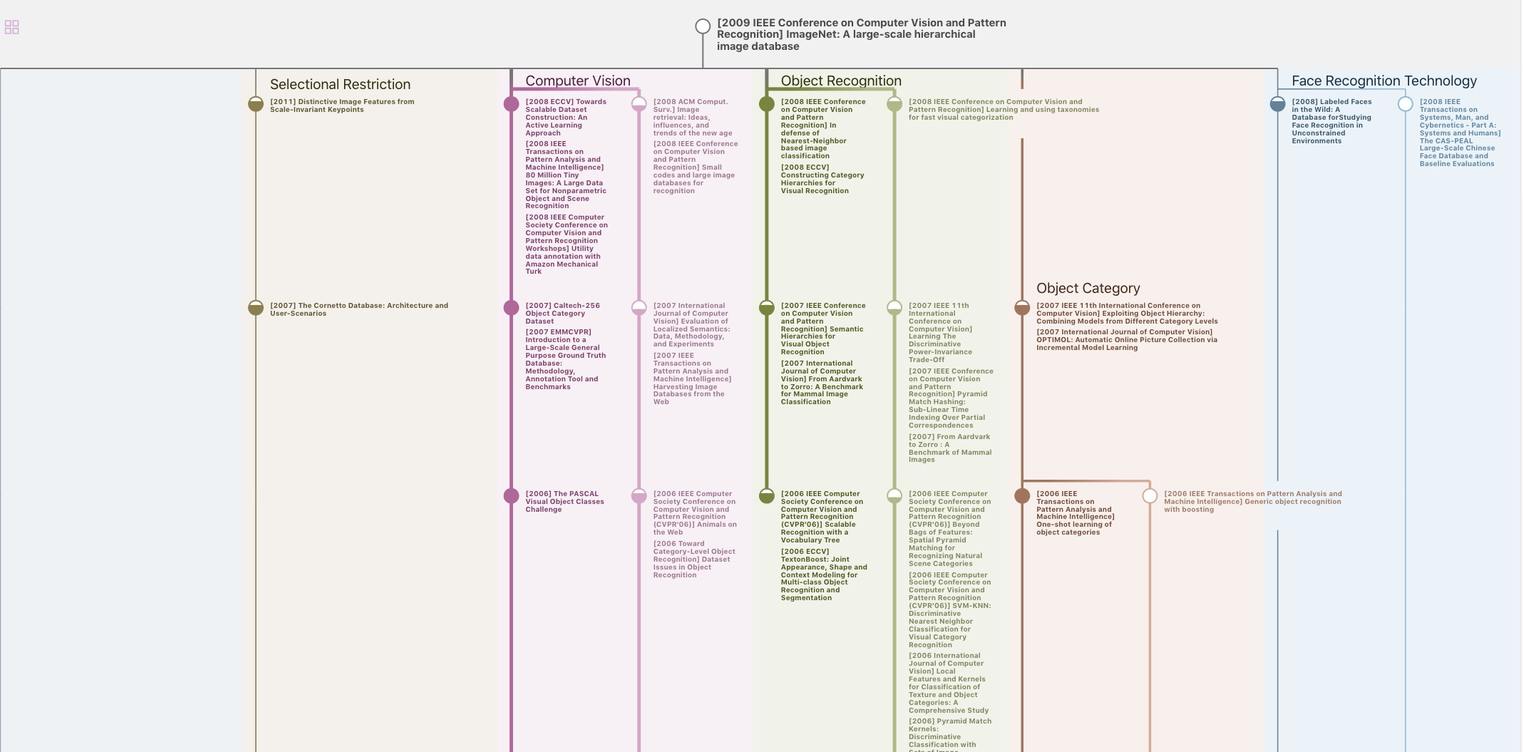
生成溯源树,研究论文发展脉络
Chat Paper
正在生成论文摘要