Absolute Position Detection in 7-Phase Sensorless Electric Stepper Motor.
IEEE/RJS International Conference on Intelligent RObots and Systems (IROS)(2022)
摘要
Absolute position detection in sensorless electric stepper motors potentially allows for higher space efficiency, improved shock resistance, simplified installation, reduced number of parts and lowered cost. A prototype is demonstrated measuring 42 x 42 x 34mm(3) with seven coils arranged in a star configuration. The rotor is (sic)25.8 x 12.5mm(2) and has 51 teeth which are irregularly spaced. At the driver side, the coil currents are measured during motion in order to reconstruct the absolute position of the motor. Calibration and smoothing techniques are used to reduce systematic and stochastic measurement errors, respectively. The motor is able to detect and correct its position after externally-induced stalls at the tested motor speeds from 40 rpm to 108 rpm. The holding torque is 0.23Nm at an armature current of 1 A; on average the torque is 7% lower than that of a reference bipolar stepper motor with the same dimensions. The results show that dynamic position sensing and correction are possible for a range of velocities, but not at standstill. The driver requires seven current sensors and sufficient computational power, and proper calibration of motor intrinsics is required beforehand. The presented technology could make existing 3-D printers and other machines with open-loop stepper motors more robust and increase the range of operating speeds and accelerations, without the adverse side-effects of increased complexity and cost associated with dedicated position sensors.
更多查看译文
关键词
sensorless
AI 理解论文
溯源树
样例
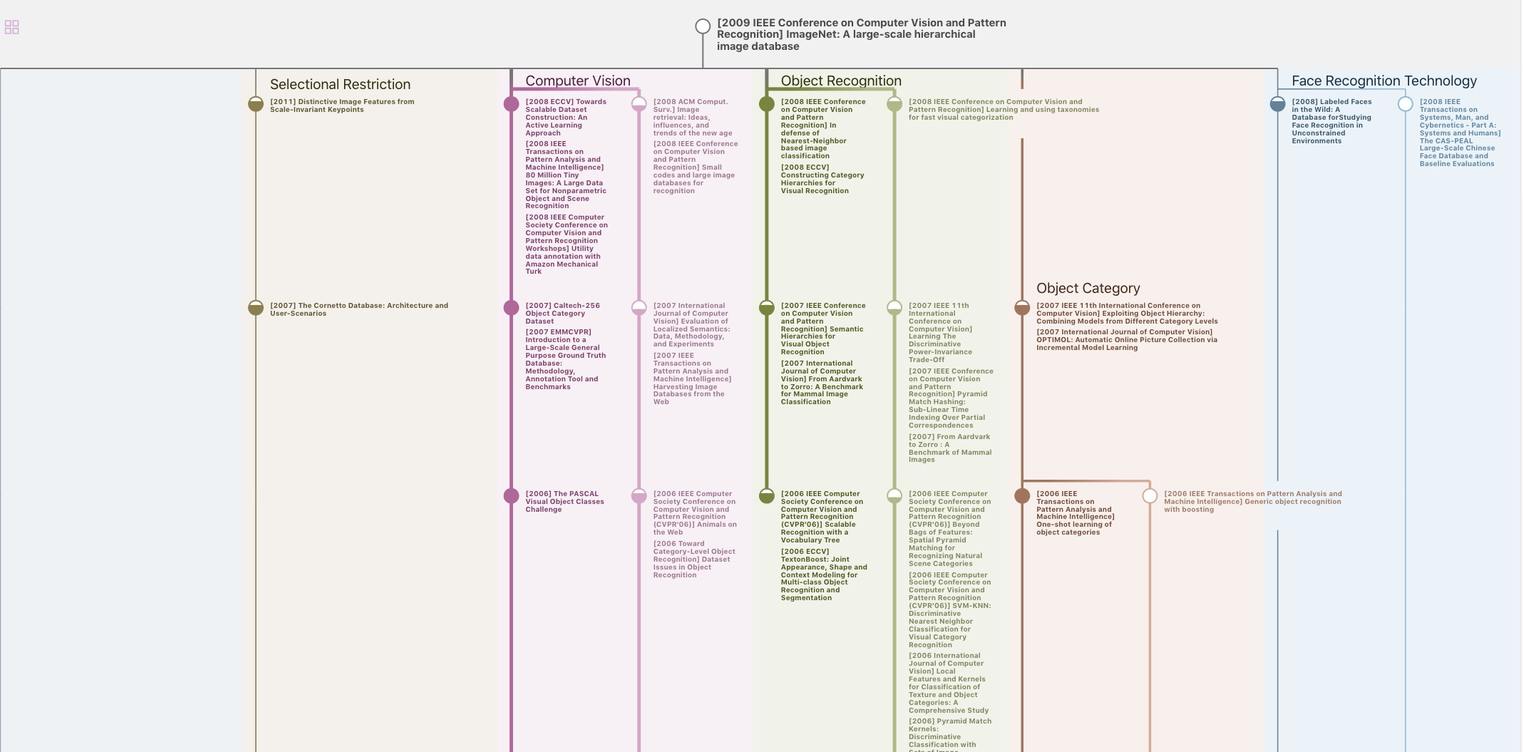
生成溯源树,研究论文发展脉络
Chat Paper
正在生成论文摘要