Crack-free laser powder bed fusion by substrate design
Additive Manufacturing(2022)
摘要
Additively manufactured components by laser powder bed fusion (LPBF) often suffer from stress-induced cracks (e.g. delamination), especially at the build-substrate interfaces where stiff mechanical constraints and large thermal gradients coexist. To reduce the probability of cracking, this work proposes an innovative strategy to optimize the geometry of the substrate by reducing its mechanical stiffness and, consequently, the stress accumulation during LPBF. To assess the feasibility of the strategy, a coupled thermo-mechanical finite element model, calibrated with the experimental evidence obtained from the LPBF metal deposition of a bridge-type structure, is used to predict the thermo-mechanical behavior of two T-shape AM parts built on (i) a typical solid substrate and (ii) a groove patterned substrate, respectively. The results show that several visible cracks appear at the interface between the build and the typical solid substrate due to stress concentration (up to 1600 MPa), while a crack-free component can be manufactured by adding grooves through the thickness of the substrate, without compromising the resulting microstructure and microhardness of the metallic materials with high crack sensitivity. The difference between the groove patterned substrate design with respect to the use of support structures used for printing cantilever structures is clarified to further justify the novelty of the proposed approach.
更多查看译文
关键词
Laser powder bed fusion,Cracking,Structural optimization,Thermomechanical simulation
AI 理解论文
溯源树
样例
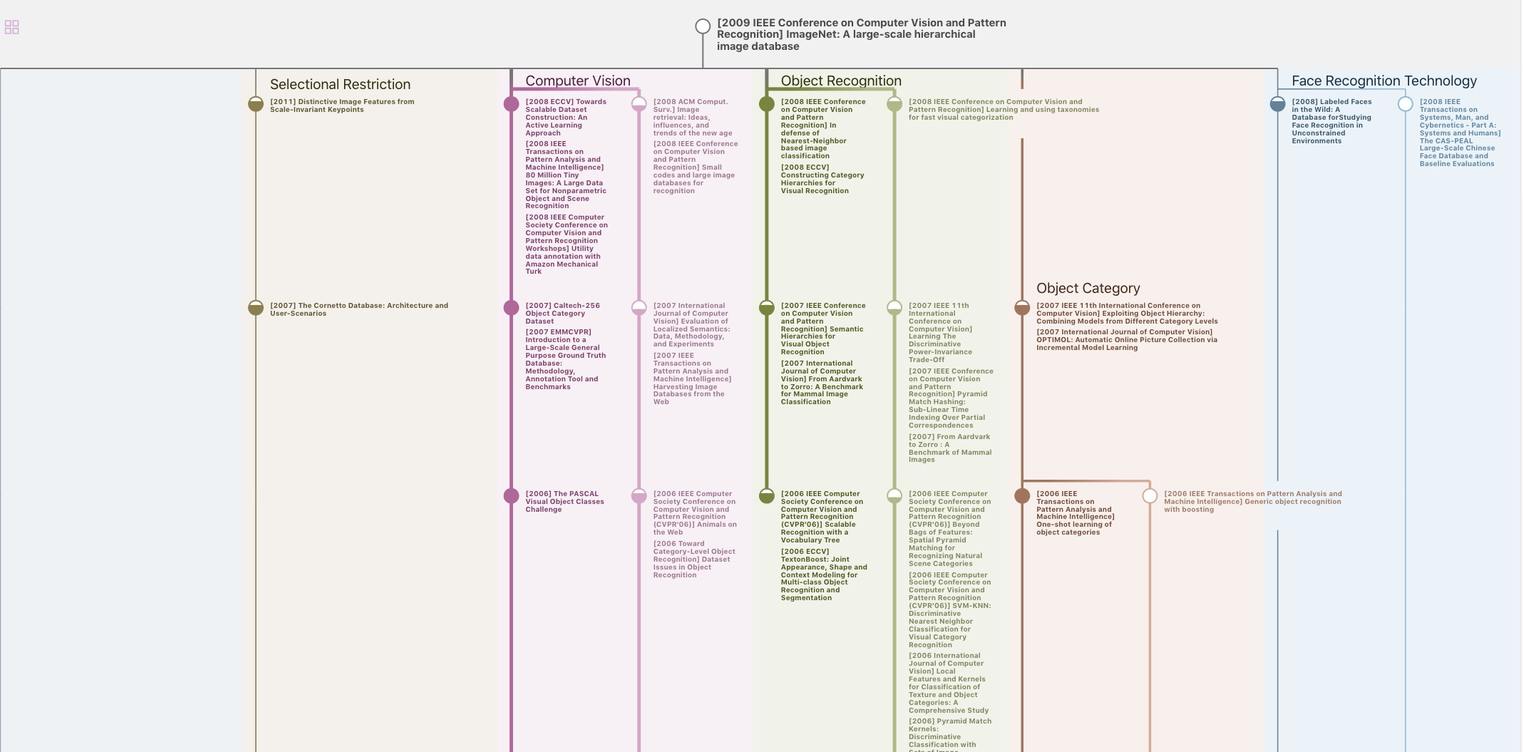
生成溯源树,研究论文发展脉络
Chat Paper
正在生成论文摘要