Toward a Physical Basis for a Predictive Finite Element Thermal Model of the LENS™ Process Leveraging Dual-Wavelength Pyrometer Datasets
Integrating Materials and Manufacturing Innovation(2022)
摘要
Predicting the thermal history of a component produced via metal-based additive manufacturing is an important step of the part qualification process because the thermal history can be used to predict thermally induced residual stresses, distortion, and porosity. Thermal simulation calibration and validation are difficult due to the lack of insight into the melt pool during the build from traditional data used for calibration, such as thermocouple measurements and infrared camera images. This work presents a three-dimensional, finite element method, predictive thermal model of a Ti–6Al–4V thin wall manufactured via LENS™ that accounts for heat transfer due to conduction, convection, and radiation. Thermal melt pool data taken with a dual-wave pyrometer are used to calibrate and validate the model. Results from the calibration and validation studies indicate that process parameters (i.e., layer height and width) along with physical properties of the heat source and material can be used to inform the heat source modeling of powder-blown directed energy deposition finite element thermal models to generate datasets for modeling across multiple length scales in an integrated computational materials engineering framework.
更多查看译文
关键词
Additive manufacturing,Directed energy deposition,Laser engineered net shaping,Finite element analysis,Ti–6Al–4V
AI 理解论文
溯源树
样例
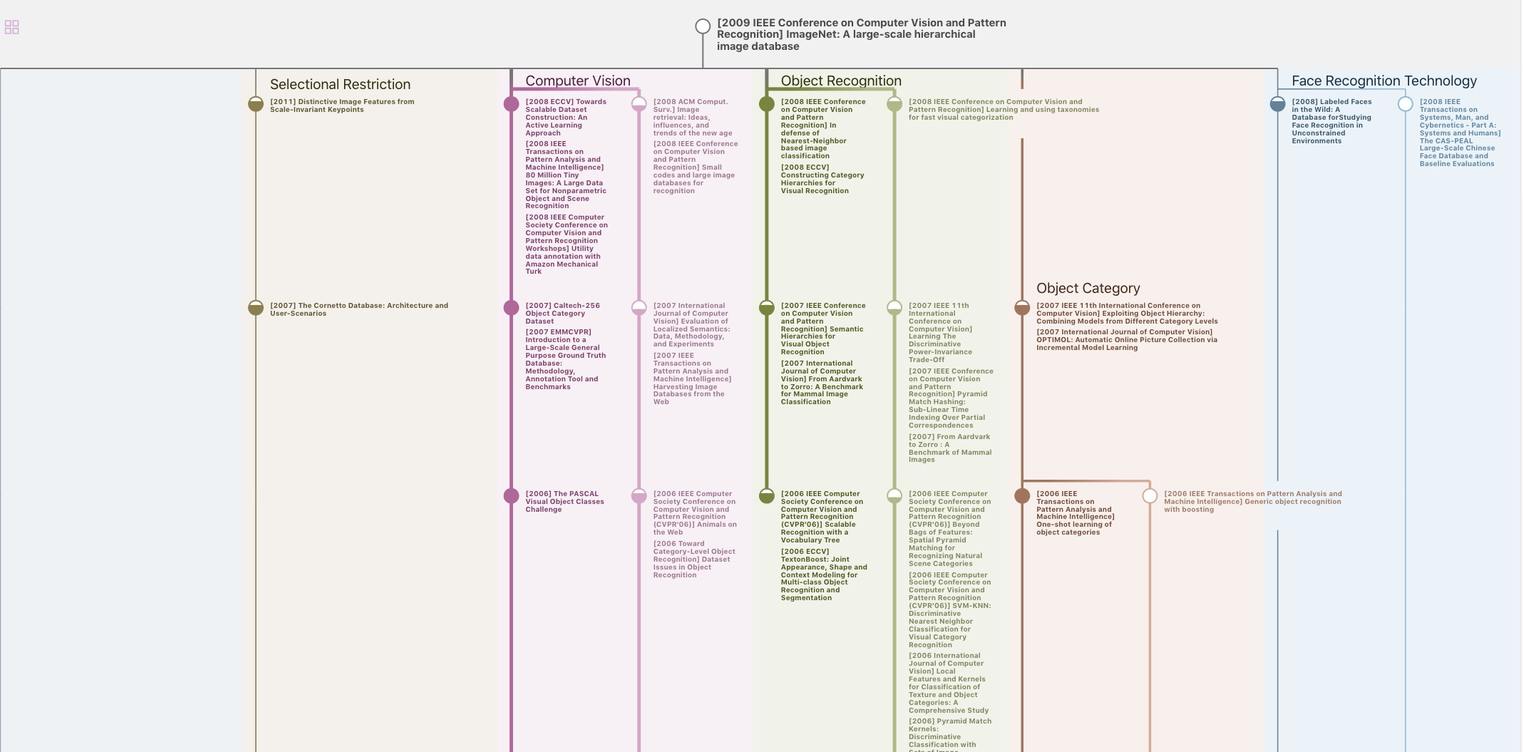
生成溯源树,研究论文发展脉络
Chat Paper
正在生成论文摘要