Scalable, flexible and resilient parallelization of fused filament fabrication: Breaking endemic tradeoffs in material extrusion additive manufacturing
Additive Manufacturing(2022)
摘要
Low build time in Material Extrusion Additive Manufacturing (MatEx) is key to economic printing of large parts and bigger batch sizes on an industrial scale. A prevalent solution is to print large roads at the cost of reduced geometric resolution and greater post-processing waste. The alternative of parallelization, i.e., using multiple printheads to concurrently print distinct sections of a part, suffers from limited geometric complexity, high cost, and complex machine design. We create a new paradigm for parallelized MatEx of thermoplastics called Multiplexed Fused Filament Fabrication (MF3). MF3 prints concurrently with multiple FFF extruders without controlling each extruder motion’s individually by using a new toolpath strategy that is rooted in our discovery of continuous filament retraction and advancement. MF3 can print non-periodic 3D structures, larger contiguous parts or multiple smaller distinct parts or a mixture of both, on the same machine, at an unprecedented throughput-resolution combination, without the limitations of state-of-the-art parallelization methods. MF3 also enables a form of hardware-fault-tolerance that is lacking in conventional single-nozzle printing by allowing printing to continue despite extruder failure. We reveal key parametric effects in continuous retraction/advancement and uncover new insight into the corresponding extrudate behavior. We also develop a unique thermal model which shows the impact of the extruder array’s configuration and the inter-section interface type on part-scale temperature evolution. Finally, we discuss how MF3 will realize new economies of scale and productivity in MatEx.
更多查看译文
关键词
Fused Filament Fabrication,Big Area Additive Manufacturing,Throughput-resolution tradeoff,Flexibility,Resilience
AI 理解论文
溯源树
样例
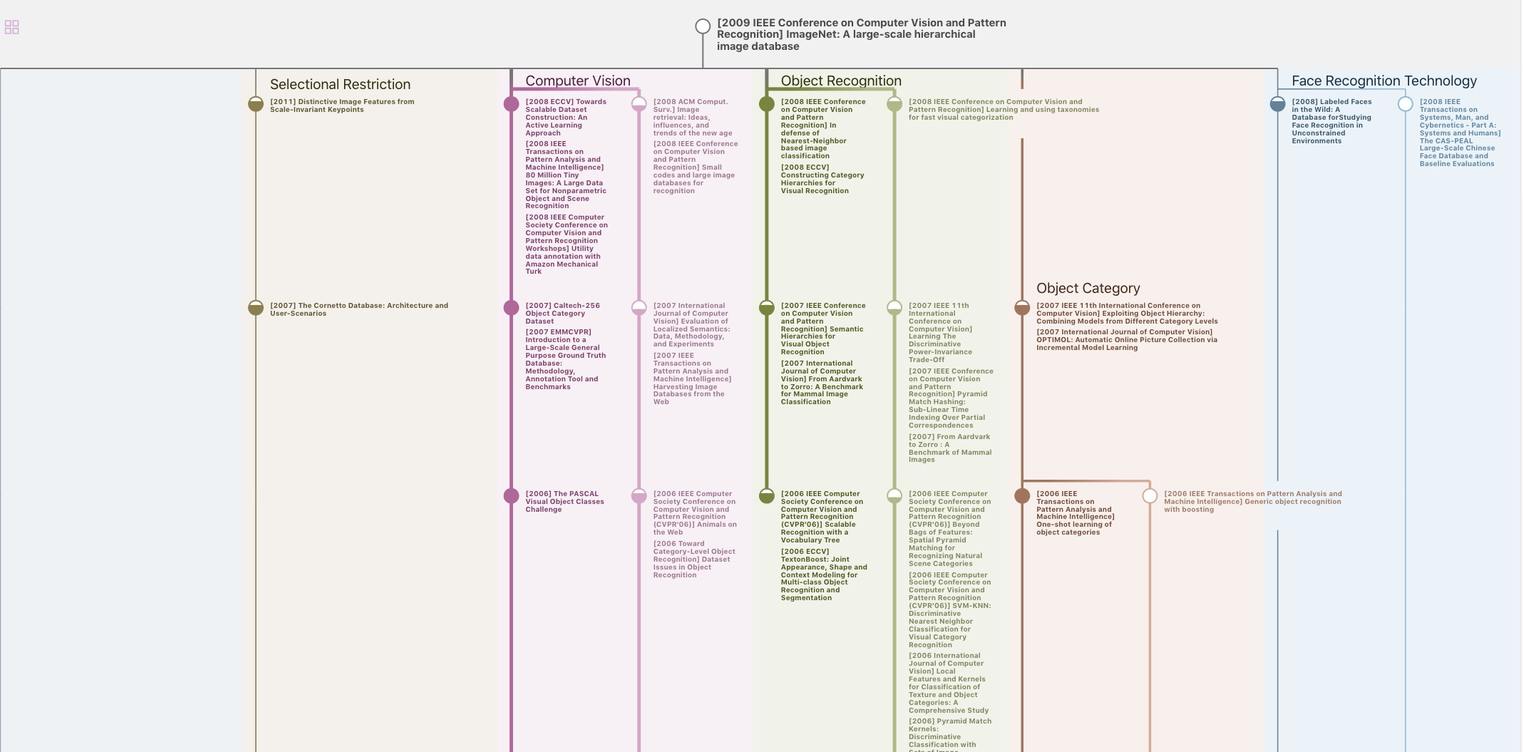
生成溯源树,研究论文发展脉络
Chat Paper
正在生成论文摘要