Optimization of perforated support structures for electron beam additive manufacturing
The International Journal of Advanced Manufacturing Technology(2022)
摘要
The current study aims to design optimal support structures for the fabrication of titanium alloy overhangs by electron beam melting such that they are easy to remove and consume less material without affecting the part quality. To achieve this objective, the effect of design and process parameters of the perforated block support structures was evaluated and optimized using response surface methodology and multi-objective genetic algorithm. The results showed that it is possible to reduce the support volume by 19% and support removal time by 45% without any warping deformation using the optimum combinations (tooth height of 2.885 mm, tooth base interval of 1.677 mm, perforation beam of 4.611 mm, beam current of 5.327 mA, and beam scan speed 1347.197 mm/s). In addition the multi-objective optimization results found the optimal perforated supports characterized by 4-mm tooth height, 2-mm tooth base interval, 2-mm perforated beam, 6-mA beam current, and 1600 mm/s beam scan speed. The study also showed that the use of optimum support structures results in substantial reduction of the support volume and post-processing.
更多查看译文
关键词
Additive manufacturing,Electron-beam melting,Support structures,Overhang structures,Optimization
AI 理解论文
溯源树
样例
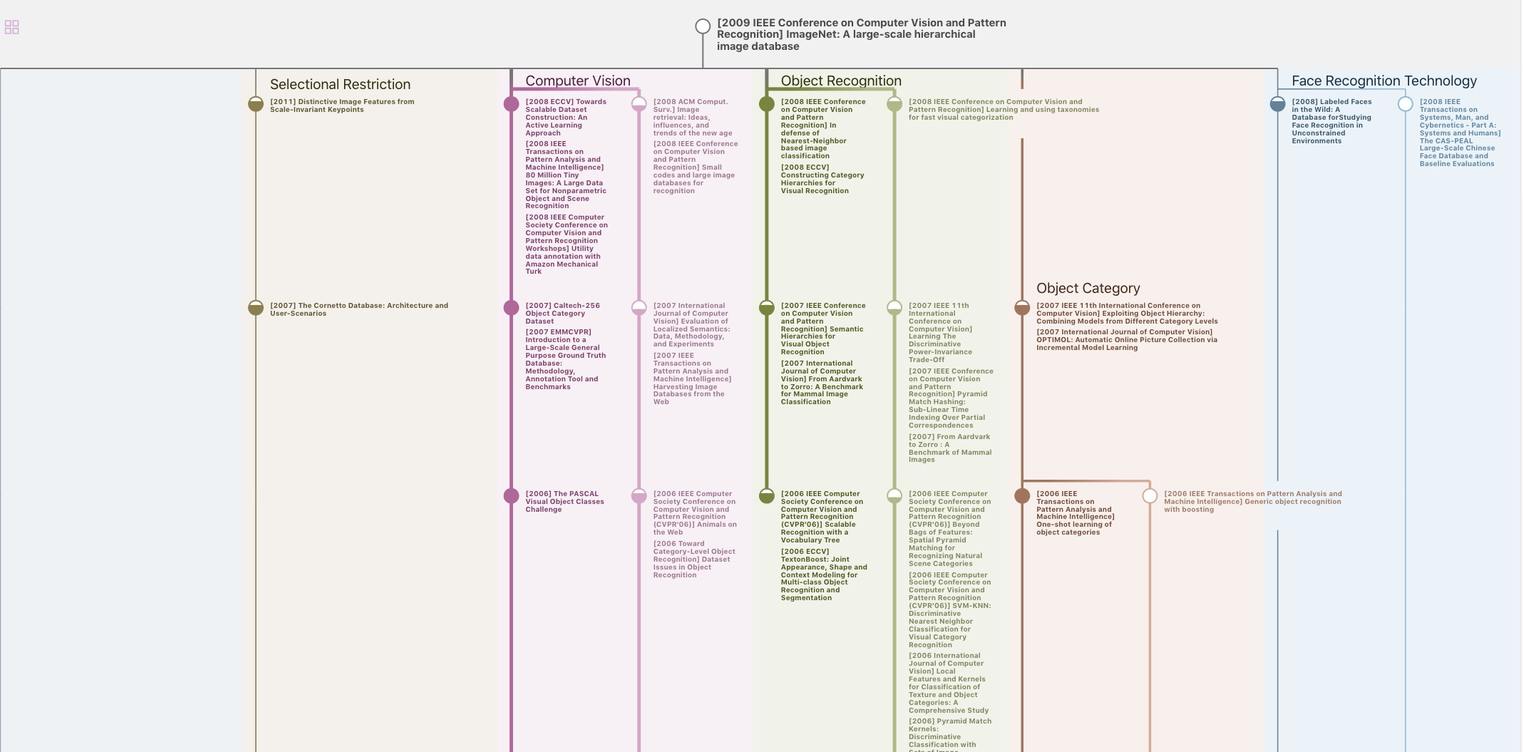
生成溯源树,研究论文发展脉络
Chat Paper
正在生成论文摘要