Gas pressure casting technique for manufacturing of W/OFHC-Cu monoblock
Fusion Engineering and Design(2022)
摘要
The important engineering part of the divertor vertical target is the quality of joint between armor materials and heat sink. To reduce the joint interface stresses, a pure copper (Cu) interlayer was provided between the tungsten(W) armor and the CuCrZr cooling tube. Gas pressure casting method was developed to reduce the porosity and improve the mechanical properties of the Cu interlayer of W/Cu monoblock. In the vacuum casting sample without pressure, porosities were found in Cu. These porosities become defects at the interface between W and Cu and decrease the mechanical properties of the Cu interlayer. In the cooling process of casting, argon gas was pressurized into a porous tube inserted in the Cu and tungsten monoblock applying perpendicular force on the joint surface. This method was effective to remove the porosity in Cu generated during the cooling process and to increase the bonding strength between Cu and tungsten. The quality of bonding interface, depth of the Cu diffusion, and hardness of Cu were compared by SEM, EDS, and Vickers hardness measurement. In the samples made by gas pressure casting method, the porosity was decreased in Cu, no defects on the interface between tungsten and Cu, Cu was diffused into tungsten with a depth of 2∼3 μm and the hardness of Cu was increased about 15%.
更多查看译文
关键词
Gas pressure casting,Plasma facing components (PFCs),W divertor,Hot radial pressing (HRP),High heat flux (HHF) test
AI 理解论文
溯源树
样例
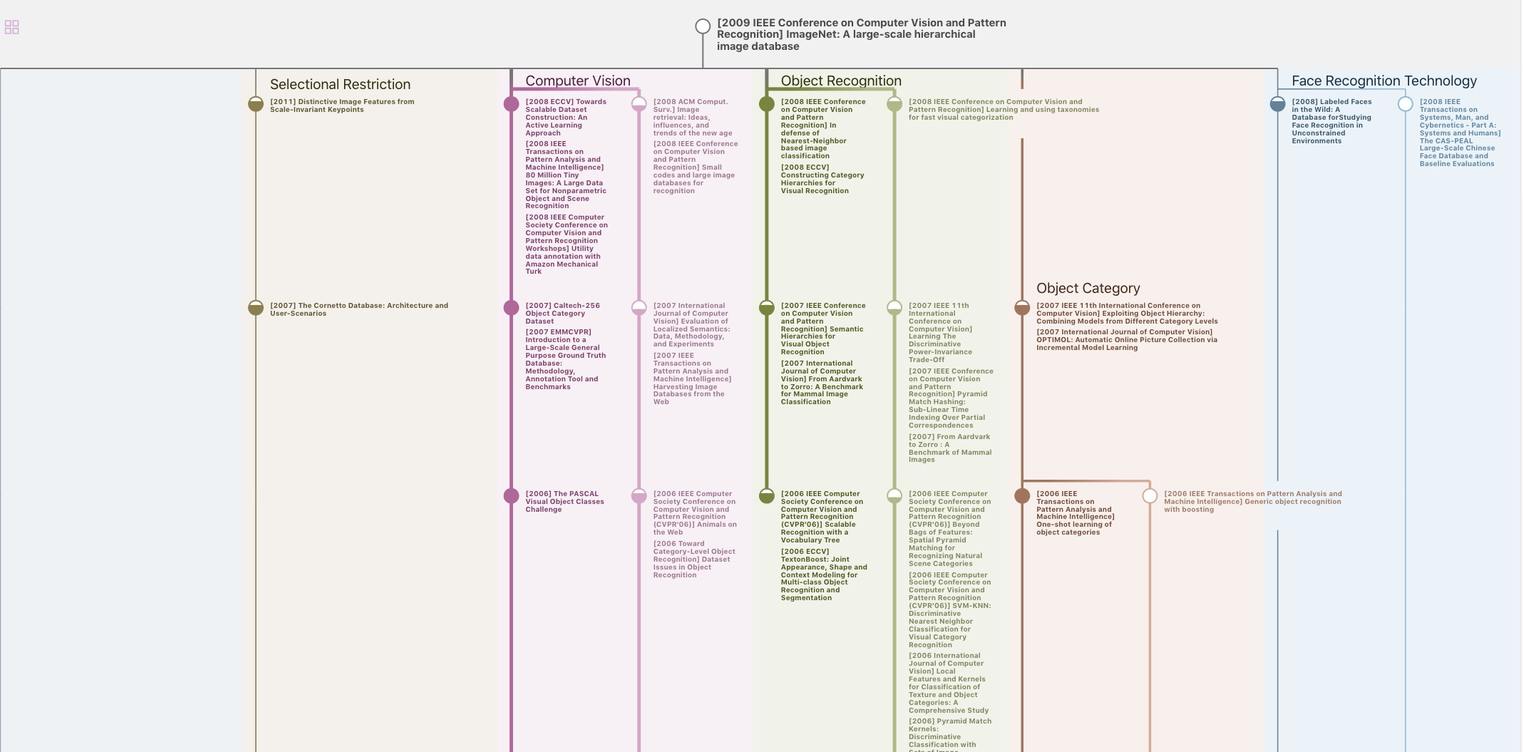
生成溯源树,研究论文发展脉络
Chat Paper
正在生成论文摘要