Direct Particle-Fluid Simulation Of Flushing Flow In Electrical Discharge Machining
ENGINEERING APPLICATIONS OF COMPUTATIONAL FLUID MECHANICS(2021)
摘要
The efficient removal of material debris by flushing is critical for the performance and the surface quality of the electrical discharge machining (EDM) manufacturing process. The particle concentration alters the thermal, mechanical, and electrical properties of the particle-dielectricum suspension and affects the manufacturing process and the surface quality by inducing high thermal loads. For the first time, we perform a direct particle-fluid simulation of the flushing cycle in a generic EDM cavity using a hierarchical Cartesian sharp-interface cut-cell method. The flow around each debris particle is completely resolved and the heat transfer between the particles and the fluid is taken into account. The rate of material removal and the cooling performance of the flushing mechanism are studied for three-volume loadings. The results show that the flow around the particles has a pronounced impact on the heat transfer between the dielectricum and the workpiece. A particle loading of 14% increases the mean heat transfer by approximately 16%. The particle loading also has a pronounced impact on the rate at which particles are flushed out of the cavity. Increasing the initial volume loading from 6% to 14% decreases the amount of particles that get flushed out of the cavity by 14%.
更多查看译文
关键词
Direct particle–, fluid simulation, cut-cell method, electrical discharge machining, mono-hole inlet flushing, multiphase flow
AI 理解论文
溯源树
样例
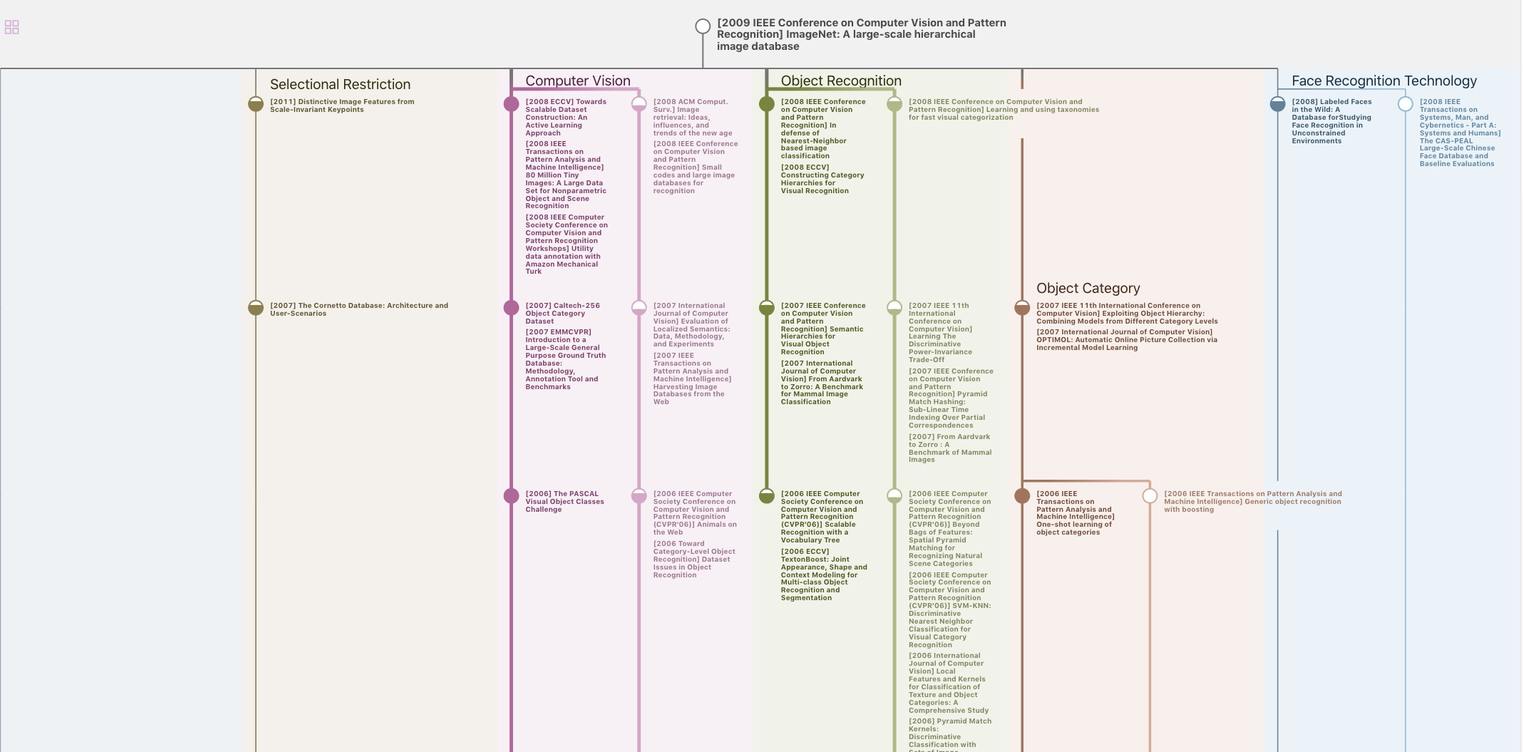
生成溯源树,研究论文发展脉络
Chat Paper
正在生成论文摘要