Multi-Physics Modeling Of Side Roughness Generation Mechanisms In Powder Bed Fusion
ADDITIVE MANUFACTURING(2021)
摘要
Surface roughness is a serious concern in powder bed fusion (PBF) additive manufacturing, especially for aerospace and biomedical applications. An adequate surface quality of as-built components is desired due to difficulty in post-processing of interior sides and intricate geometries of printings. The side surface draws more attention than the top surface and a comprehensive understanding of side roughness mechanisms is required to interpret effectively. However, observation of side roughness formation in experiments is yet difficult. In this paper, the formation process of the side surfaces in electron beam PBF is analyzed by a 3-D mesoscale multi physics simulation, so as to provide an insight view into side roughness mechanisms from the viewpoint of heat and mass transfer. The melting process and the resulting side surface morphologies of thin-walled parts are exclusively analyzed. It turns out that the melted traces in cases with a relatively low heat input generally have greater fluctuations than in cases with a high heat input, which leads to a higher side roughness. The proposed investigation reveals that the melt pool flow driven by surface tension is the main cause of track shape fluctuation. This fluctuation is driven by the random distribution of powder particles and the Plateau-Rayleigh instability, which describes the disintegration into a chain of drops. An analytical estimation of minimum limit of side roughness in as-built parts and the mechanisms for the generation of the side roughness are depicted systematically, based on which some improvement measures are proposed finally. This will help improve surface quality in metal additive manufacturing.
更多查看译文
关键词
Surface roughness, Powder bed fusion, Numerical simulation, Additive manufacturing
AI 理解论文
溯源树
样例
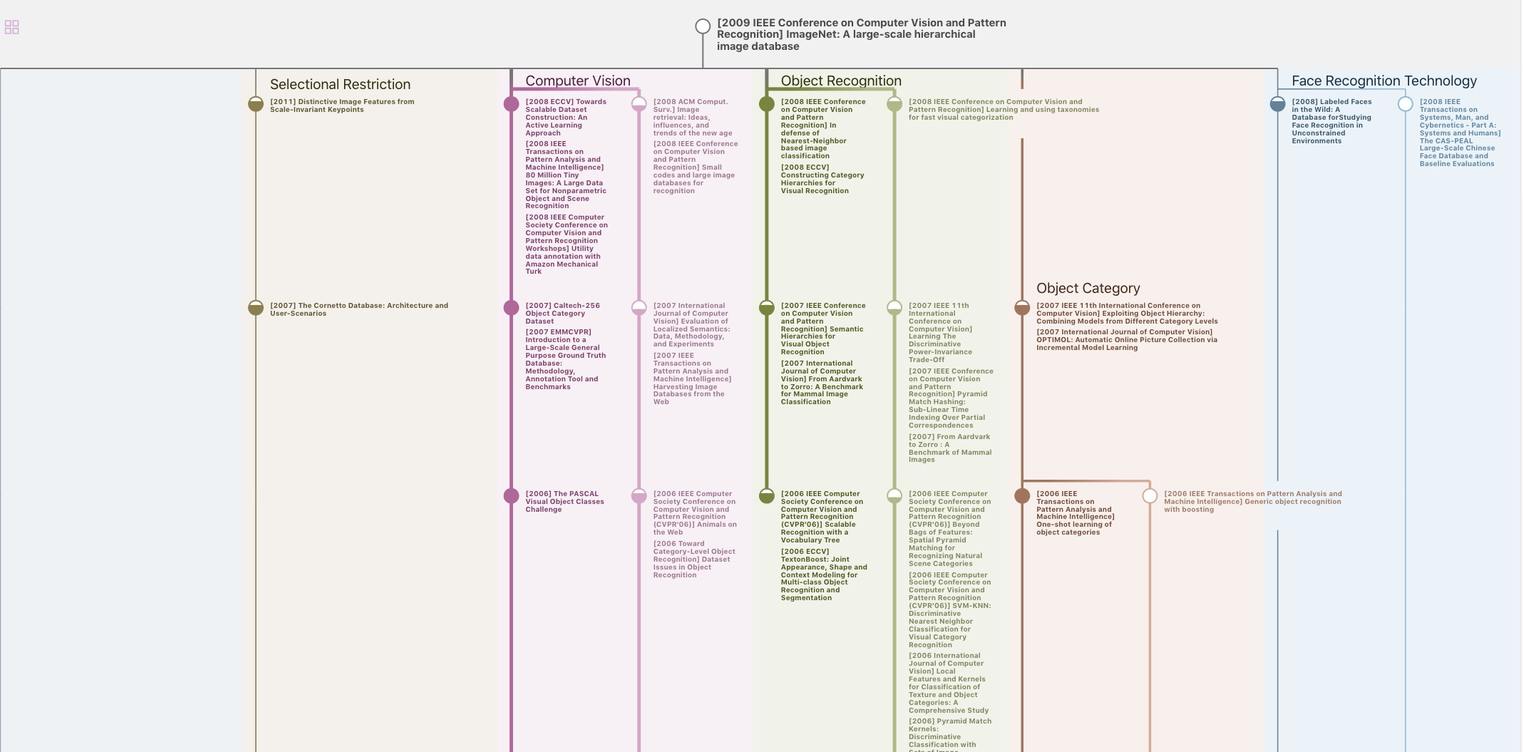
生成溯源树,研究论文发展脉络
Chat Paper
正在生成论文摘要