Thermo-Mechanical Loading Of Full-Scale Welded Piping Components In High Temperature Water Environment
PROCEEDINGS OF THE ASME PRESSURE VESSELS AND PIPING CONFERENCE, 2017, VOL 4(2017)
摘要
The effect of high-temperature water environment on the fatigue life of steels used for pressure retaining components has been discussed controversially for the last 20 to 30 years. Fatigue testing of laboratory specimens for typical steels showed significant drops in fatigue life when tested in high temperature water environment compared to air environment. Based on these findings the applicability of fatigue design curves such as those enclosed to ASME code Section III NB are questionable concerning their degree of conservatism. Nevertheless, experience from components experiencing power plant operation does not match up with laboratory fatigue testing of small uniaxial specimens. Fatigue life estimations based on models representing laboratory tests do highly overestimate the fatigue life reduction resulting from high temperature water environments compared to the analyses of components having reached their postulated fatigue life. To overcome this disagreement component testing under defined laboratory conditions is highly desired to achieve "gap closure".At MPA University of Stuttgart a test facility was set up where environmental fatigue testing on component level can be realized within a hot water test loop. Within the framework of a research project sponsored by the German Federal Ministry of Education and Research (BMBF) piping modules containing a dissimilar metal weld are exposed to water environments with alternating temperature conditions. At specific locations water at about room temperature is injected to a hot pipe segment which results in thermal induced loading situations. Consequently thermal stratification and shocks cause localized stresses and strains in the tested modules. Within this paper an overview of the testing procedure, the tested materials and results from both experimental measurements and fractographic analyses are presented and discussed. In addition to experimental investigations the results drawn from a coupled computational fluid dynamics (CFD) and structural mechanics finite-element-analysis (FEA) including a fatigue life assessment are shown. Finally, this work states on the applicability of common fatigue assessment procedures including the fatigue life reducing factors based on the results from realistic fatigue testing on component level.Within low cycle fatigue tests a nickel-base weld material was characterized regarding its fatigue life in air and high temperature water environment in comparison. It was found that the effect of environmentally assisted fatigue is in good agreement with what is known from literature for smooth specimens made from austenitic steels. Results from tests using notched specimens showed a significant change in the environmental effect compared to tests using smooth specimens. During component testing within a hot water loop modules which contain a dissimilar metal weld were exposed to alternating water temperature conditions between 20 degrees C and 65 degrees C. At the end of the component test cracks were found in the regions where the highest temperature changes were measured and calculated. The numerical analysis of the fluid structure -interaction pointed out that the transition region between the austenitic steel and the nickel base weld material is the highest loaded section within the module. Finally the fatigue assessment of the pipe sections containing cracks showed that based on common fatigue hypothesis the loading state is regarded to be subcritical.
更多查看译文
关键词
fatigue assessment of components, Thermal Fatigue, Environmentally Assisted Fatigue (EAF), microstructural influence of weldments, multiaxiality, component testing, fluid-structure-interaction
AI 理解论文
溯源树
样例
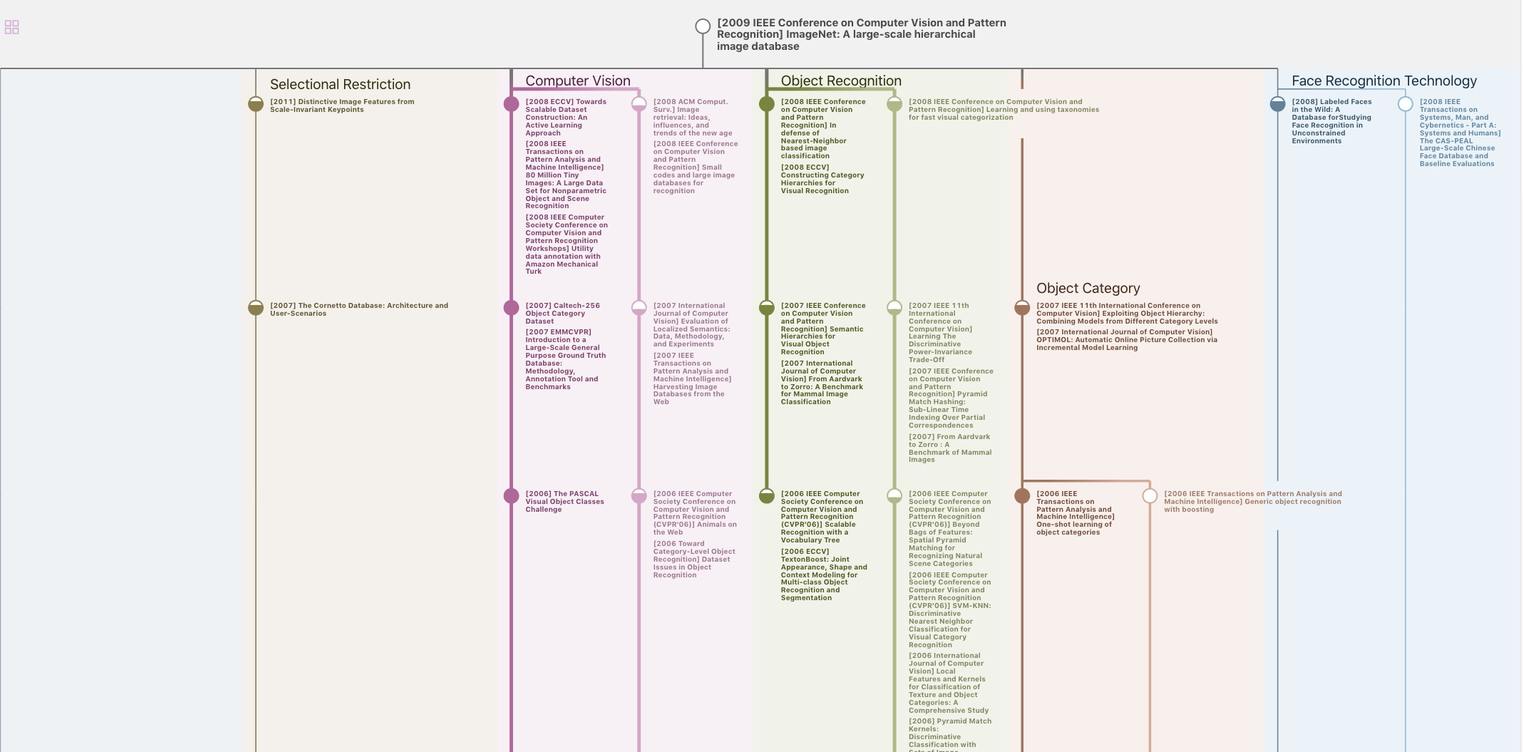
生成溯源树,研究论文发展脉络
Chat Paper
正在生成论文摘要