A Redundant Parallel Robotic Machining Tool: Design, Control And Real-Time Experiments
NEW DEVELOPMENTS AND ADVANCES IN ROBOT CONTROL(2019)
摘要
In this chapter, we present a machining device, named ARROW robot, designed with the architecture of a redundant parallel manipulator capable of executing five degrees-of-freedom in a large workspace. Machine-tools based on parallel robot development are considered a key technology of machining industries due to their favourable features such as high rigidity, good precision, high payload-to-weight ratio and high swiftness. The mechanism of ARROW robot isolates its workspace from any type of inside singularities allowing it to be more flexible and dynamic. An improved PID with computed feedforward controller is implemented on ARROWrobot to perform real-time experiments of a machining task. The control system deals with antagonistic internal forces caused by redundancy through a regularization method, and achieves a stability conservation in case of actuators saturation. The results are evaluated using the root mean square error criteria over all the tracking trajectory confirming the high accuracy and good performance of ARROW robot in machining operations.
更多查看译文
关键词
Machine tool, Redundant parallel robot, Kinematics, Dynamics, Singularity analysis, Motion planning, Control, PID, Feedforward, Anti-windup
AI 理解论文
溯源树
样例
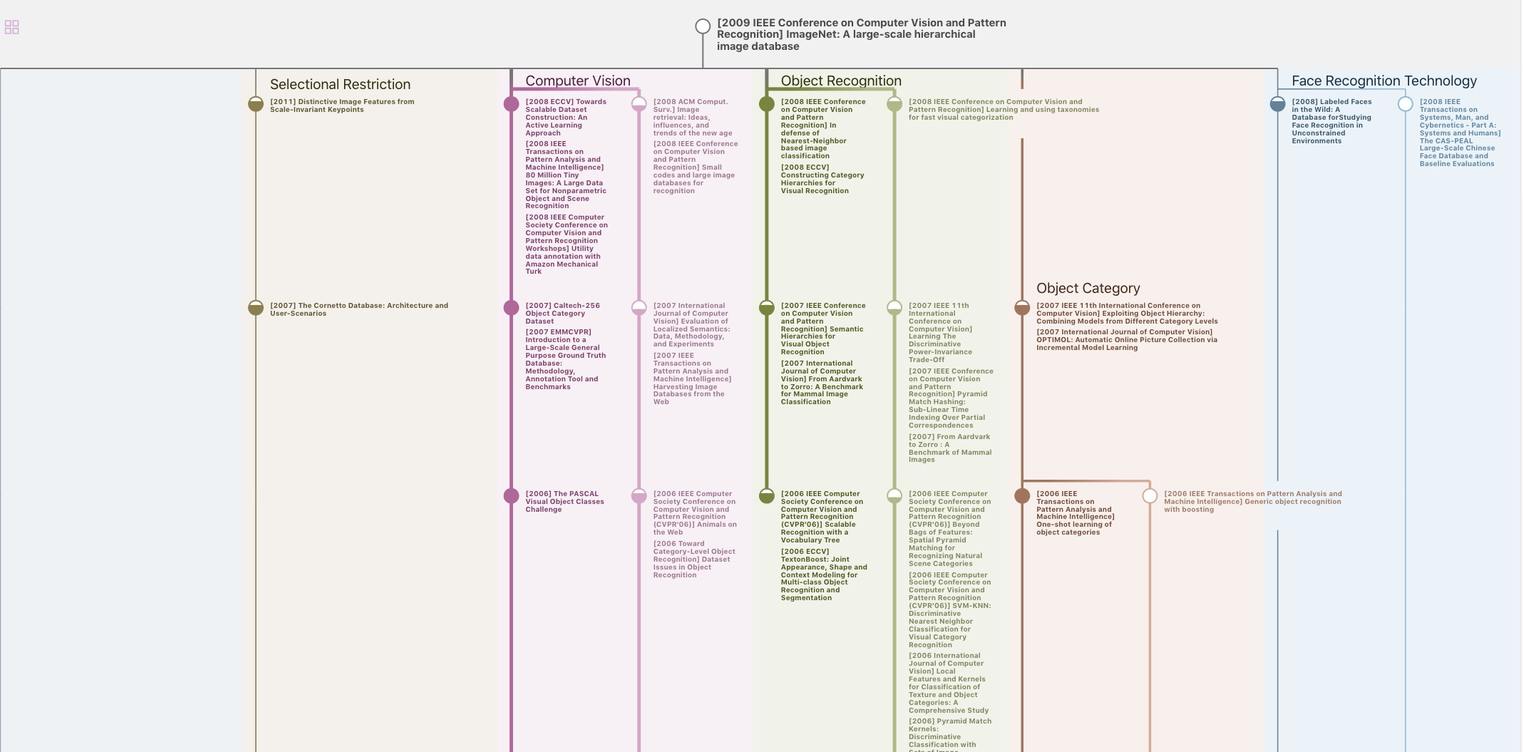
生成溯源树,研究论文发展脉络
Chat Paper
正在生成论文摘要