Influence of fused deposition modelling process parameters on wear strength of carbon fibre PLA
MATERIALS TODAY-PROCEEDINGS(2020)
摘要
Fused deposition modeling (FDM) is an additive manufacturing, rapid prototyping process in which the material melts and gets extruded from the nozzle and build the part layer-by-layer. In this study, investigation on different process parameters such as layer thickness, infill pattern and infill density for the wear strength of carbon fibre PLA (Poly Lactic Acid) specimen processed by FDM is performed and analyzed. Carbon fibre PLA filament contains short fibres of carbon that are infused into PLA base material which helps to increase strength, stiffness and base material properties and prevents shrinkage. The study of wear strength was conducted by the Pin-on-disc apparatus on the specimen fabricated as per ASTM standard. The experimental values of wear rate, specific wear rate and coefficient of friction for different process parameters were measured and analyzed that would help to conclude the most efficient process parameter. Out of these three parameters, the layer thickness is the most influential process parameter that affects the wear rate. It is observed that an increase in infill density helps in increasing wear strength. The wear strength varies with the infill pattern also. This study helps to develop functional relationships between FDM process parameters and wear rate and also guides to select the suitable option of FDM process parameters to provide better wear property. (C) 2019 Elsevier Ltd. All rights reserved. Selection and peer-review under responsibility of the scientific committee of the First International conference on Advanced Lightweight Materials and Structures.
更多查看译文
关键词
Fused Deposition Modeling,Carbon fibre PLA,Layer thickness,Infill pattern,Infill density
AI 理解论文
溯源树
样例
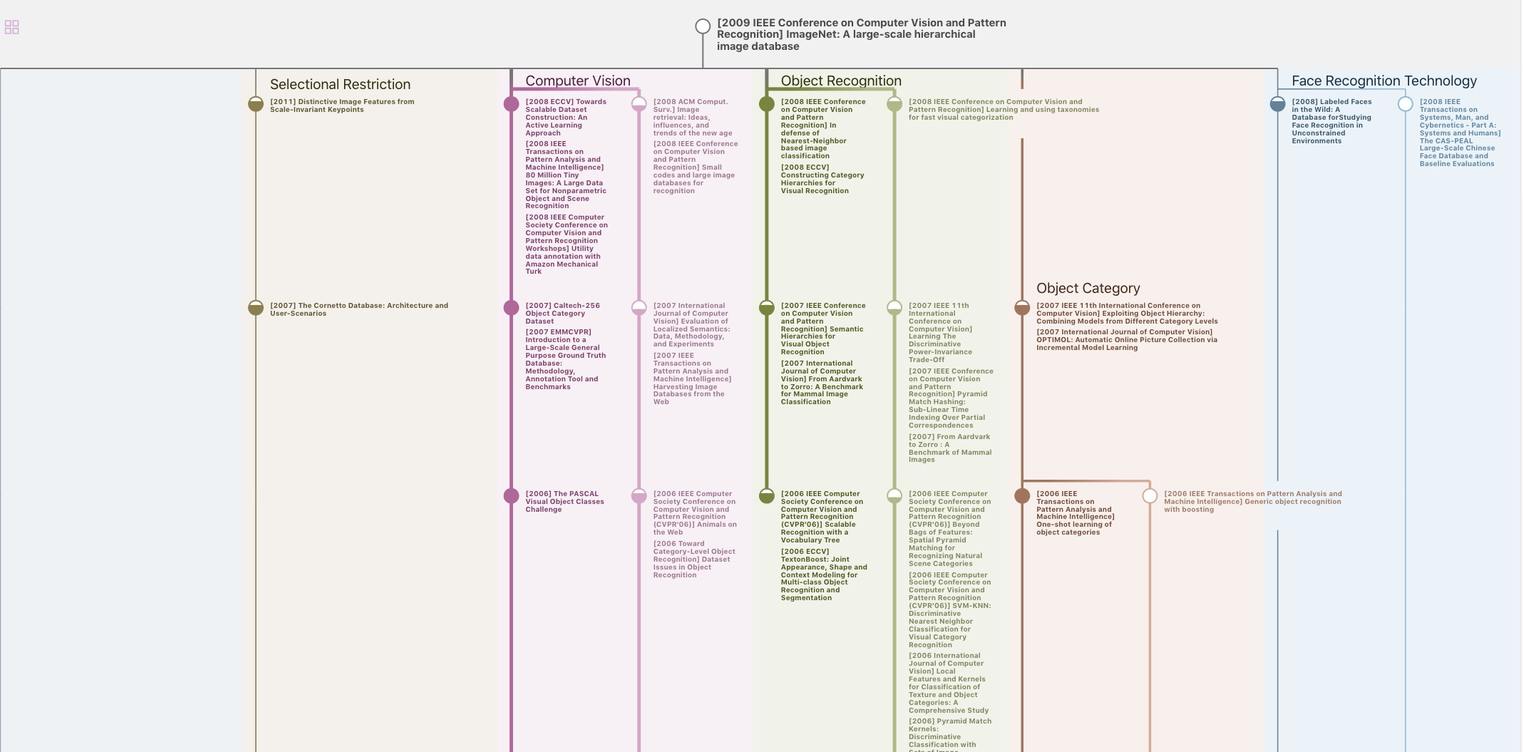
生成溯源树,研究论文发展脉络
Chat Paper
正在生成论文摘要