Structural design of groove and micro-blade of the end mill in aluminum alloys machining based on bionics
The International Journal of Advanced Manufacturing Technology(2016)
摘要
In aerospace manufacture industry, cutting vibration is a key factor for surface quality and tool life during milling of thin-walled aluminum alloy parts, and the high-efficiency machining is limited seriously for this reason. In this research, the cutting layer’s deformation was inhibited to reduce cutting vibration by optimal design of cutting edge structure. Base on the observation and imitation of corn leaf’s teeth, the structure of groove and micro-blade of peripheral cutting edge was designed. The orthogonal cutting models were developed to analyze the cutting process by ABAQUS. Furthermore, comparative experiments of milling aluminum alloy 7050-T7451 were carried out to analyze the cutting force, vibration, surface roughness, and residual stress. The test and simulation results showed that the designed solid cemented carbide end mill based on bionics had a good effect for inhibiting the cutting layer’s deformation. The fluctuations of cutting force, cutting vibration, surface residual stress, and surface roughness were reduced effectively.
更多查看译文
关键词
Groove,Micro-blade,FEM,End mill,Aluminum alloy
AI 理解论文
溯源树
样例
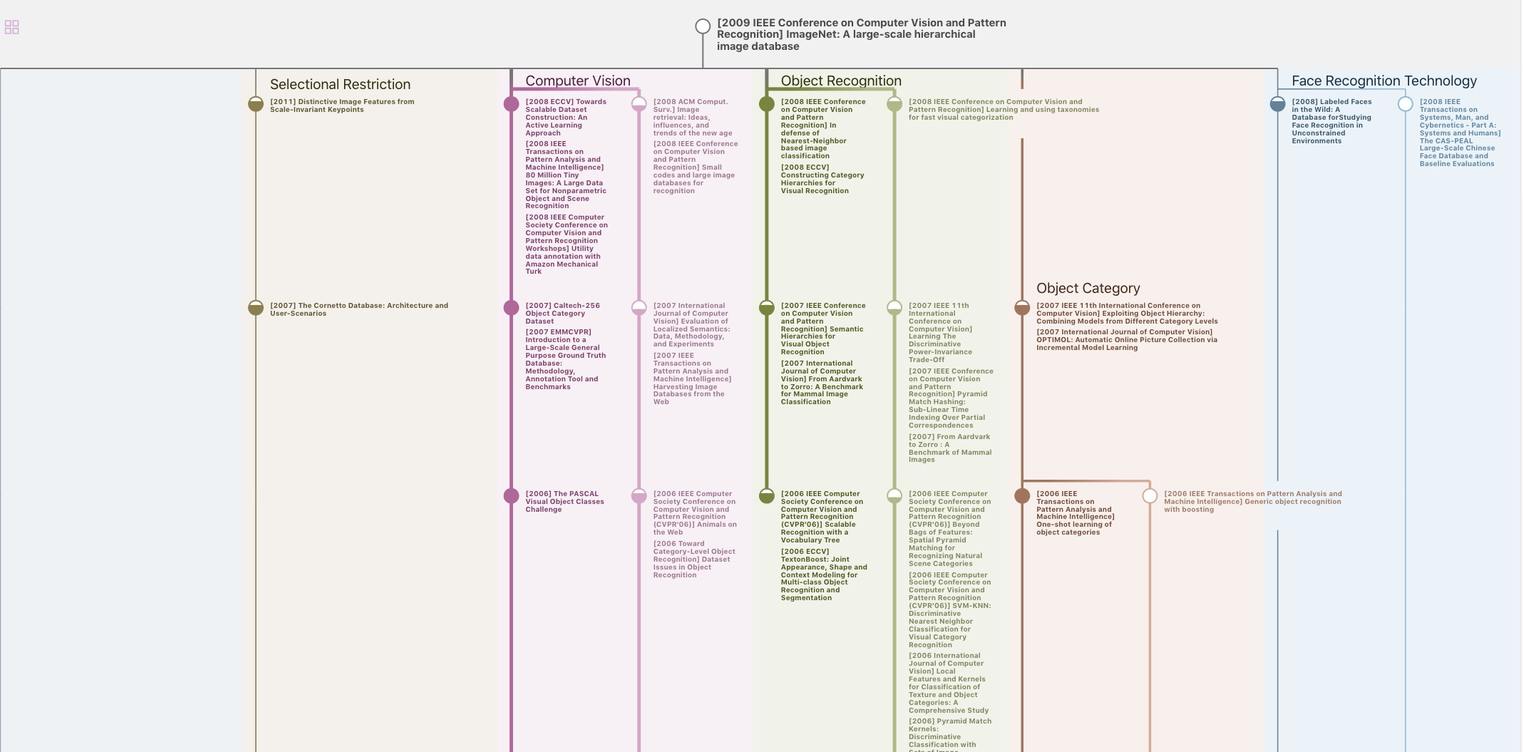
生成溯源树,研究论文发展脉络
Chat Paper
正在生成论文摘要