Modelling Of Reinforced Polymer Composites Subject To Thermo-Mechanical Loading
INTERNATIONAL JOURNAL FOR NUMERICAL METHODS IN ENGINEERING(2005)
摘要
A coupled finite element model is developed to analyse the thermo-mechanical behaviour of a widely used polymer composite panel subject to high temperatures at service conditions. Thermo-chemical and thermo-mechanical models of previous researchers have been extended to study the thermo-chemical decomposition, internal beat and mass transfer, deformation and the stress state of the material. The phenomena of heat and mass transfer and thermo-mechanical deformation are simulated using three sets of governing equations, i.e. energy, gas mass diffusion and deformation equations. These equations are then assembled into a coupled matrix equation using the Bubnov-Galerkin finite element formulation and then solved simultaneously at each time interval. An experimentally tested 1.09 cm thick glass fibre woven-roving/polyester resin composite panel is analysed using the numerical model. Results are presented in the form of temperature, pore pressure, deformation, strain and stress profiles and discussed. The maximum normal stress failure criterion is used in order to establish the load-bearing capability of the composite panel. Significant pore gas pressure build-ups (to 0.8 MPa and higher) have been perceived at high thermo-chemical decomposition rates where the material experiences a complex expansion/contraction phenomenon. It is found that the composite panel experiences structural instability at elevated temperatures up to 300 degrees C but retains its integrity even under moderate external loading. Copyright (c) 2005 John Wiley & Sons, Ltd.
更多查看译文
关键词
finite element method, glass reinforced plastics, high temperatures, pyrolysis, thermo-chemical, thermo-mechanical
AI 理解论文
溯源树
样例
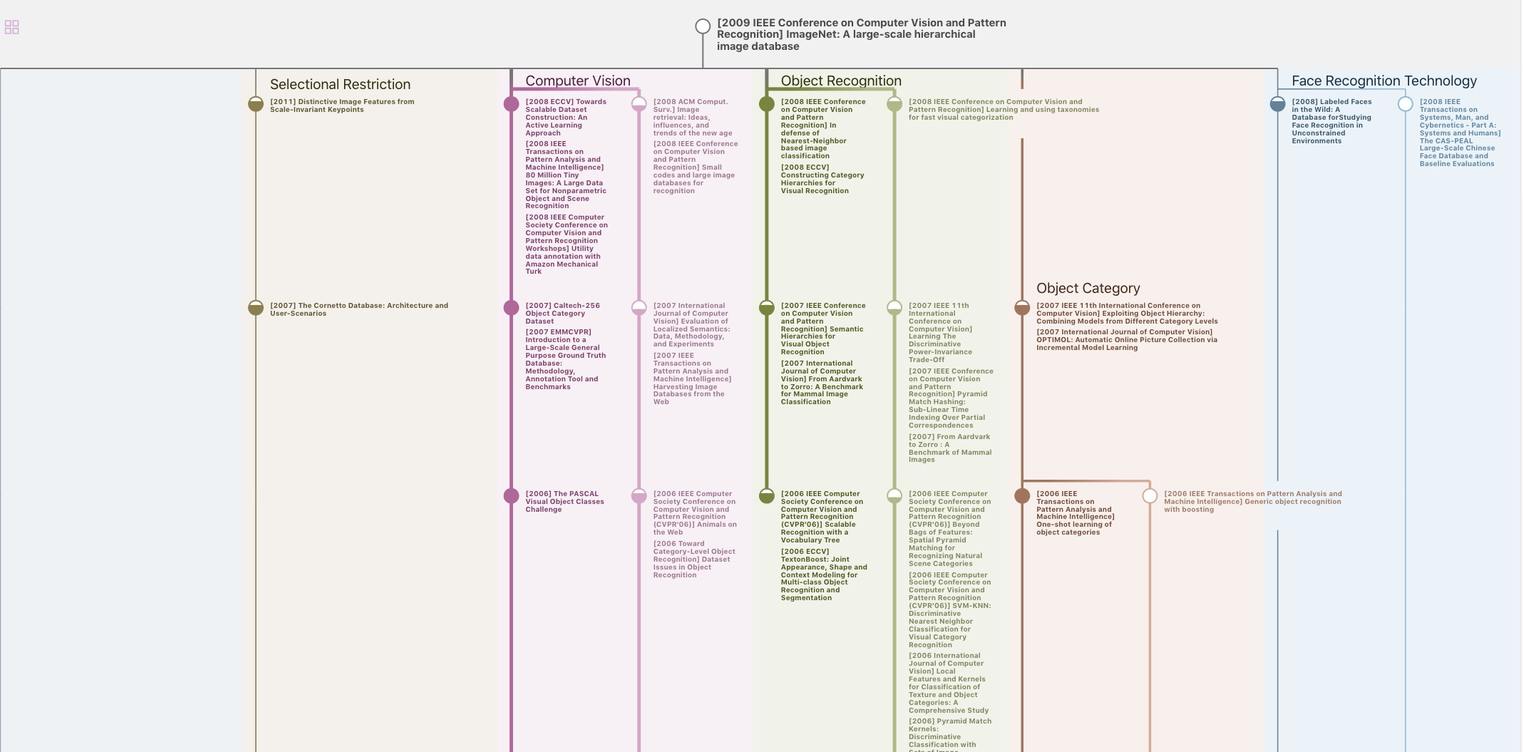
生成溯源树,研究论文发展脉络
Chat Paper
正在生成论文摘要